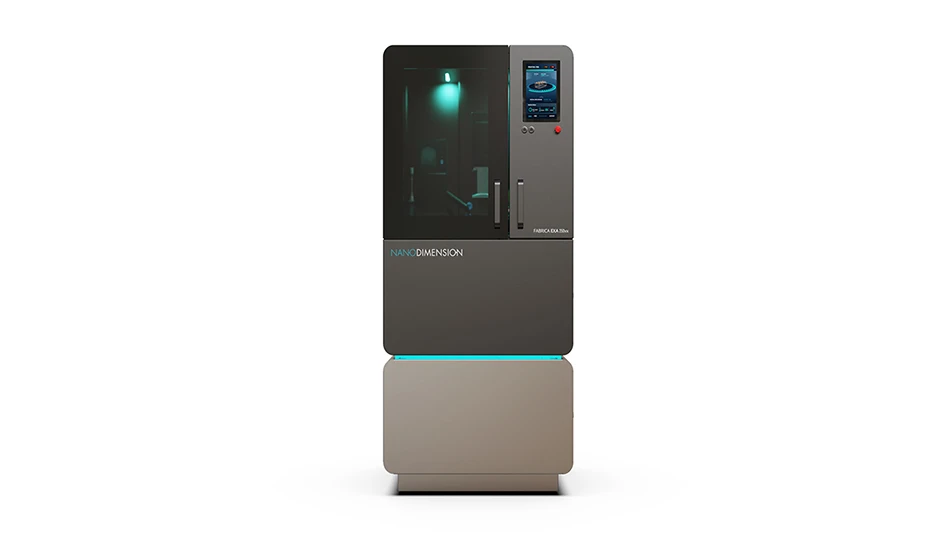
CREDIT: NANO DIMENSIONS
Nano Dimension has launched its Exa 250vx digital light processing (DLP) 3D printer for micro applications which was developed to enable the creation of superior resolution micro parts at high production throughput.
Designed using insights gathered from users of Nano Dimension’s proven and established Fabrica Tera and Fabrica Giga systems, the Exa 250vx has been engineered to deliver the highest productivity in the industry for exceptionally precise micro parts. Built to support the demands of service bureaus and OEMs alike, the Exa 250vx Micro 3D printer provides a reliable and cost-effective alternative to traditional micro-manufacturing methods, including micro-injection molding and micro-CNC.
Leveraging resin-based DLP technology to achieve precise layer heights and exceptional surface finishes, the Exa is an ideal solution to meet the exacting needs of manufacturers across an array of vertical sectors and applications. These include connectors and other miniaturized components for electronic devices; medical devices like micro needles, micro filters, and components for minimally invasive surgeries; plus applications for optical uses and micro-decorative items - including gold coated – for the jewelry sector.
Further benefits are assured due to Exa’s compatibility with Nano Dimension’s range of resins for high resolution micro parts, starting with D-810. This enables the production of durable, rigid parts with high structural integrity – perfect for creating intricate and precise components in the aforementioned application areas. As with the other Fabrica systems, there is an open system policy, allowing users to work with third party resins.
“Manufacturers producing micro parts are facing a trade-off between precision and productivity,” says Nir Sade, senior vice president of additive manufacturing at Nano Dimension. “As part of Exa’s development, we worked closely with customers to address a host of needs such as high-volume parts production with micro level detail for parts larger than the 50mm build limit we currently have on the Tera. The result is a system that provides the perfect balance of quality, productivity and cost, making it a game changer for the industry.”
With its larger 100mm x 100mm x 70mm build volume, 7.6µm XY resolution, and layer thickness of just 10 microns, the Exa combines sought after attributes that deliver rapid production and high resolution, allowing manufacturers to produce the specific micro parts to meet their particular engineering requirements.