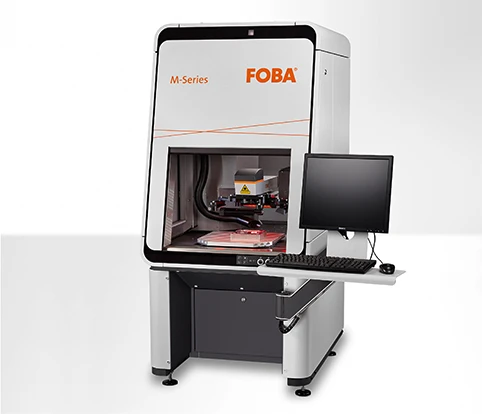
Selmsdorf, Germany – More and more industries require reliable traceability and safety for their industrial products. FOBA, a technology leader in product identification and direct part marking, offers solutions that guarantee a reliably traceable, permanent mark in zero-defect quality – especially when FOBA’s integrated vision technology is used. In addition to that, FOBA laser marking systems contribute to increased productivity by decreased production costs and a lower scrap rate. FOBA showcases a M2000 and M1000 laser marking workstation – both with integrated through-the-lens vision technology – at IMTS, America’s largest manufacturing show.
Many industries such as the electronics, medical, plastic processing and automotive industries, are obliged to mark their products permanently and precisely in order to meet the high standards of product safety, process reliability, traceability and quality assurance. Manufacturers of medical devices for example have to meet the demands of the FDA’s Unique Device Identification (UDI) system. All other industries also depend on permanently readable marks on the parts and products that they manufacture in order to reliably trace them throughout their entire life cycle. Any marking content has to be perfectly positioned to achieve highest product quality, minimum scrap, and a lean production.
At this year’s IMTS, FOBA showcases its high precision and cost-effective laser marking workstation FOBA M2000 with integrated IMP vision (Intelligent Mark Positioning). The integrated high-speed camera system looks with the laser beam onto the product and is capable of automatic part detection and mark positioning and alignment. With IMP, manufacturers achieve zero-defect marking quality which grants them a decisive advantage in a market as competitive as the medical sector.
FOBA’s vision solutions are part of the closed-loop laser marking process HELP (Holistic Enhanced Laser Process) which covers pre- and post-mark verification. HELP is a three-stage process. The first stage includes part validation, pre-mark verification and mark alignment. After the second stage, the laser marking, follows the third stage with mark verification, optical character verification OCV and the validation of the 2D or 3D matrix code including UDI.
Source: FOBA