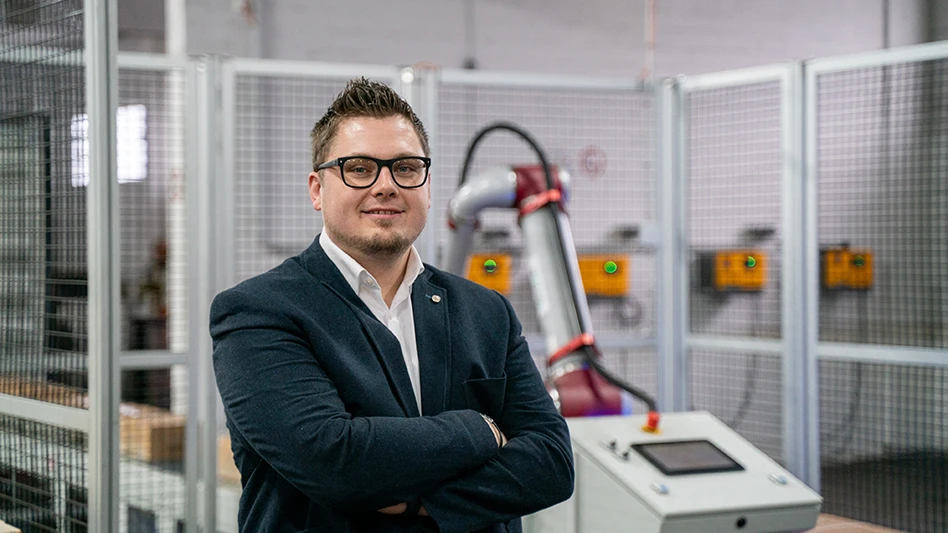
CREDIT: ONROBOT
If you needed to buy a device to provide transportation from point A to point B, you wouldn’t buy a motor and then try to turn it into a vehicle. But many manufacturers who need a device to load and unload machines or stack pallets take exactly that approach when they buy a robot arm. That’s especially true of manufacturers who are the primary targets for the ease-of-use, DIY marketing claims from many robot providers.
Unfortunately, what these manufacturers end up with – for tens of thousands of dollars – is just a robotic arm.
It’s a component. An important one, certainly, but the device they need to tend their machine or stack their pallets is a complete robotic system. That includes – at a minimum – the robot arm, one or more grippers, user interface, and programming. To deploy that robot arm (and in addition to the cost of it), they need to hire someone to scope, buy, integrate, and program all the other pieces to create the actual system they need. This process can take weeks or months, at a cost that can be multiple times the cost of the robot itself.
What’s worse, when the robotic system is delivered, it can do only what it was initially programmed to do. Every time products change, and a new part needs to be machined or a new size box palletized, the integrator must return to reconfigure and reprogram the system, at additional cost and potential downtime for the manufacturer.
The rise of turnkey robotics – and new alternatives
This realization has prompted many manufacturers to look for what integrators and machine builders began calling “turnkey” systems. These systems are engineered and branded for a specific common automation application such as machine tending or palletizing. The system typically includes all the necessary components for those applications, although some may be options at an additional cost. The robot arm may already be specified, which can limit the manufacturer’s choice, even if they’ve standardized on a different robot brand for consistency of parts, training, etc.
Finally, although these systems are referred to as turnkey, only part of the system has been pre-engineered. It must still be customized, programmed, integrated, and deployed onsite, and workpiece changes down the road still require the integrator to return and redeploy the system at additional cost. And despite the implication that “turnkey” means an immediately available product, these partially engineered systems can have lead times almost as long as a fully custom solution.
Certainly, there’s a place for turnkey robotics, and it’s a strong step towards simplifying otherwise complex automation. But new alternatives are also arising.
Complete, off-the-shelf robotic systems meet evolving needs
What many manufacturers need – and what many integrators and machine builders would love to be able to offer – is a complete, off-the-shelf robotic system that is pre-built, pre-configured, with immediate availability. Because it’s a complete product, all costs have been defined so pricing is fully transparent. And the system is designed to meet the needs of a specific defined application such as machine tending, palletizing, or packaging. For most manufacturers, the only flexibility they need is built-in capabilities for fast, easy in-house redeployment for standard production changeovers for a new box size or pallet setup, or to load and unload a different workpiece.
Sound like a pipe dream? It’s actually where the industry is going.
It’s where it must go, because manufacturers have been frustrated too many times by automation promises that are never quite fulfilled and budgets that continue to rise.
At the same time, integrators are frustrated by long sales and development cycles for what should be basic, well-understood systems for common applications, as well as ongoing, less-profitable, and hard-to-staff support for basic changes for months and years after installation. Many integrators would rather keep selling additional complete systems that build on customers’ automation successes than must keep re-engineering the ones they’ve already sold.
Yes, automation technology has improved in leaps and bounds. Robot arms are easier to program, grippers and tools are more intuitive and easier to integrate, and development tools are appearing that can speed integration by skilled technicians. Importantly, the intuitive concept of turnkey or complete systems versus components is beginning to take hold. But there’s another critical step that needs to occur.
Integrators and machine builders need a development platform that lets them quickly create complete, off-the-shelf robotic systems. This will allow them to develop competitive products specific to their customers’ business needs, with standard-product economies of scale such as lower cost, immediate availability, and lower risk than customized systems.
Their customers get an immediate, low-risk solution for their automation needs. If it’s off-the-shelf, delivery and setup should be within a day. And when business needs change, as they always do, they can respond with quick adjustments for new workpieces with existing staff – no costly and time-consuming programming.
Change is already happening
Dutch integrator Just Automate is already reaping the benefits of this new approach, using the D:PLOY development platform from OnRobot to create successful robotic products. Just Automate’s off-the-shelf robotic palletizer, called MoveComponents, is being used by WEMAS Absperrtechnik GmbH, a leading German provider of road safety products to unload pallets of heavy batteries.
Julian Döring, head of materials management at WEMAS says, “There are plenty of options in the market that claim to offer easy palletizing solutions, but once you see a demo, it often becomes clear they don't live up to the promise. With the MoveComponents solution powered by D:PLOY, it was a completely different experience. What was demonstrated to us is exactly what we got – a smooth, same-day installation that delivered on our standards and expectations."
Another MoveComponents customer, beverage producer Schrobbelèr B.V., saw similar benefits in the palletizing of heavy bottles.
Jan Eijsermans, commercial director at Schrobbelèr says, “Right from the start, everything was clear and straightforward. We got detailed technical specs for the entire solution, a full list of components, and a simple, no-surprises price. It made the whole process easy to understand and gave us confidence in what we were getting."
Schrobbelèr had the complete system up and running in one day during active production, with no disruptions, and product changeovers are easily managed in-house.
Eijsermans explains, “Our liquor comes in various bottle sizes, and I manage the palletizing system entirely on my own. I don’t have a technical background, so having an easy-to-use solution was crucial for us. The palletizing system, powered by the D:PLOY platform, is incredibly straightforward and intuitive. It allows me to independently redeploy the system whenever we switch to new bottle sizes in production.”
Off-the-shelf robotics promises to boost automation success
Like every other innovation in every other industry – from cars to computers – early versions of robotic systems were custom, expensive, complex, and time-consuming. Eventually, common customer needs have been defined, components and development approaches improved, and standard products can now be developed and proven over many deployments. The economies of scale of this change also make those products more affordable and accessible.
We’re on the cusp of a new generation of off-the-shelf robotics. This change will give manufacturing customers and machine builders/integrators powerful new options that promise to drive their individual success as well as industry growth.
Latest from Today's Medical Developments
- You can still register for March’s Manufacturing Lunch + Learn!
- HERMES AWARD 2025 – Jury nominates three tech innovations
- Vision Engineering’s EVO Cam HALO
- How to Reduce First Article Inspection Creation Time by 70% to 90% with DISCUS Software
- FANUC America launches new robot tutorial website for all
- Murata Machinery USA’s MT1065EX twin-spindle, CNC turning center
- #40 - Lunch & Learn with Fagor Automation
- Kistler offers service for piezoelectric force sensors and measuring chains