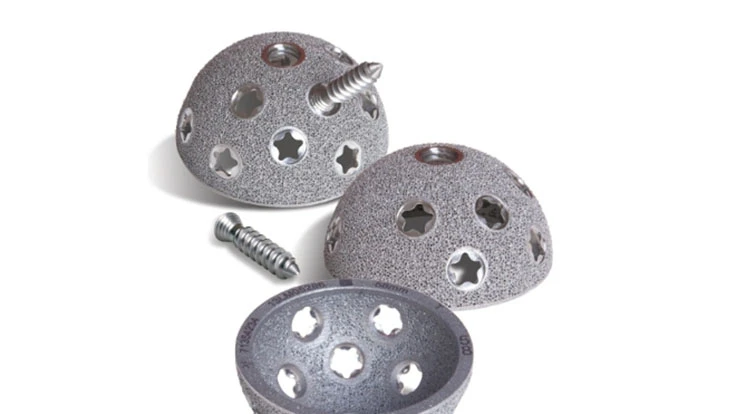
Orlando, Florida – Smith & Nephew, the global medical technology business, showcased the REDAPT Revision Acetabular Fully Porous Cup with CONCELOC Technology at last week's American Academy of Orthopaedic Surgeons (AAOS) Annual Meeting in Orlando.
The new REDAPT cup is designed for use in revision cases where compromised bone makes implant fixation and stability more difficult. To allow ingrowth, an additive, or 3D, manufacturing process is used to produce an entirely porous implant that mimics the structure of cancellous bone and new variable-angle locking screws can be used to enhance implant stability and minimize micromotion after surgery.
"We're excited about the creative possibilities this new manufacturing process holds for surgeons and their patients," said Mike Donoghue, vice president of global reconstruction at Smith & Nephew. "Bringing to market a 3D-printed titaniumacetabular cup for difficult revision procedures is just one example of the potential of this remarkable technology."
The CONCELOC Advanced Porous Titanium technology is an alternative to external porous coatings, such as sintered beads or fiber mesh used in other uncemented implants, to allow bone ingrowth securing the implant in place.
Successful fixation of a porous implant requires that the implant remains in steady, stationary contact with the bone as it heals and new bone grows. For this reason, the new REDAPT cup also uses the new REDAPT Variable Angle Locking Screws, which work within the implant's unique geometry to provide both compression and a rigid construct to the acetabular shell, as well as traditional, non-locking screws.
"This fully porous cup gives surgeons flexibility in ways that simply weren't possible before," said Craig Della Valle, MD, professor of orthopaedic surgery at Rush University Medical Center in Chicago, who participated on the surgeon design team for the new REDAPT cup. "The locking screws, screw-in trials, purpose-built liners and screw hole patterns optimized for hard-to-access areas really set it apart during a revision procedure. This cup builds on good technology and turns it into something spectacular."
Smith & Nephew received Food and Drug Administration 510(k) clearance for the REDAPT Revision Acetabular Fully Porous Cup with CONCELOC Technology in November 2015.
About 3D manufacturing
The 3D manufacturing process used to build each new REDAPT cup begins by precisely aiming a laser onto a thin layer of titanium (Ti-6Al-4V) powder. The heat generated by the laser fuses the powder together, building upward, layer-by-layer, until a fully formed titanium implant is produced. This manufacturing method allows for complex design geometries that would be difficult, expensive or impossible to achieve with traditional manufacturing methods. For example, solid reinforcements can be built directly into the porous structure to provide extra strength in precise locations.
About Smith & Nephew
Smith & Nephew is a global medical technology business dedicated to helping healthcare professionals improve people's lives. With leadership positions in Orthopaedic Reconstruction, Advanced Wound Management, Sports Medicine and Trauma & Extremities, Smith & Nephew has around 15,000 employees and a presence in more than 100 countries. Annual sales in 2015 were more than $4.6 billion. Smith & Nephew is a member of the FTSE100.
Source: Smith & Nephew
Latest from Today's Medical Developments
- Fed’s soft landing may ignite manufacturing technology market growth
- Platinum Tooling named North American distributor for Dunner
- Bridging the Skills Gap: A Solution for Today’s Labor Shortage
- Machine Solutions acquires Alpine Laser LLC
- OSG USA’s PHOENIX PFDC indexable face mill cutter & inserts
- IMTS 2024 Booth Tour: Fagor Automation Corp.
- How Robotics and Automation are Transforming Manufacturing
- Quasar Medical acquires Ridgeback Technologies