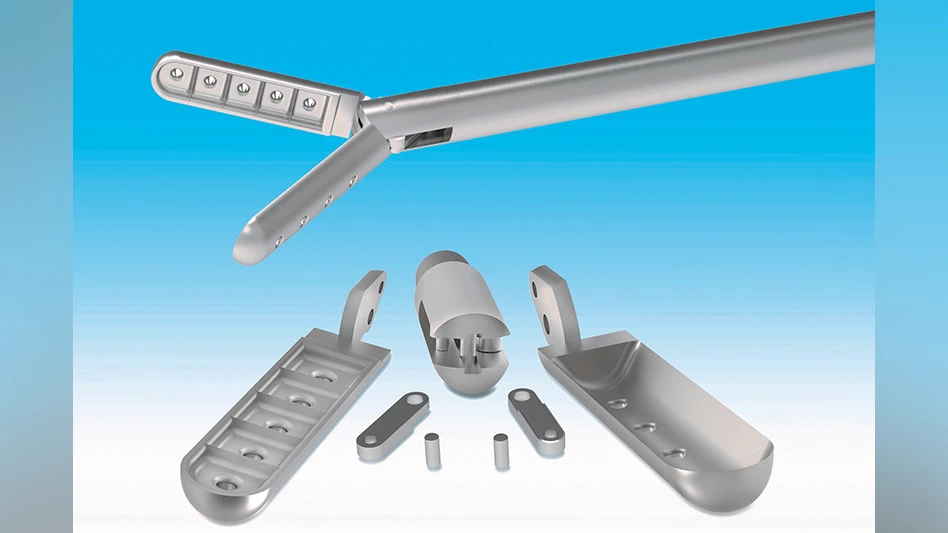
Smith Metal Products
Medical designers are looking for streamlined processes and to reduce time-to-market and are now able to verify a product before committing to expensive mold design and building. Smith Metal Products advanced 3D Binder-Jet Metal Printing additive production system is cost-effective alternative to building test molds or CNC machining prototype parts.
Smith Metal Products quick-turn 3D Binder-Jet Metal Printing provides customers the ability to evaluate, modify, and verify their product/components using a MIM-like process. Designers can see, touch, and evaluate prototype MIM-like parts comparable to Metal Injection Molded parts in as little as 1 to 2 weeks. Available part materials for Smith’s 3D Binder-Jet Printing include stainless steel and other alloys upon request.
Once a design is finalized and approved for production, Smith Metal Products Metal Injection Molding is often a preferred process to achieve small precision medical device components. That’s because MIM parts are precise, net-shaped and can be produced faster than machining and usually with no secondary operations. If a high tolerance needs to be held and cannot be entirely MIM molded, Smith uses CNC machining equipment to achieve tighter specifications while still being more competitive than complete machining of parts.
The MIM process is suitable for components with complicated geometries in annual volumes of 10,000 pieces or more and a finished part weight of less than 100g (3.5oz). All dimensions of the component should be 3" or less, and the maximum wall thickness should be 3mm (0.125") or less.
Latest from Today's Medical Developments
- TDK Ventures invests in ANYbotics
- Our first webinar of 2025 highlights additive manufacturing
- Costa Rica, a global magnet for medical devices
- PhD student helps develop medical device for children with congenital heart defects
- Happy New Year
- Best of 2024: #1 Article – 2024 Forecast
- Best of 2024: #1 News – 6 trends impact medtech in 2024
- Best of 2024: #2 Article – Cybersecurity in medical devices