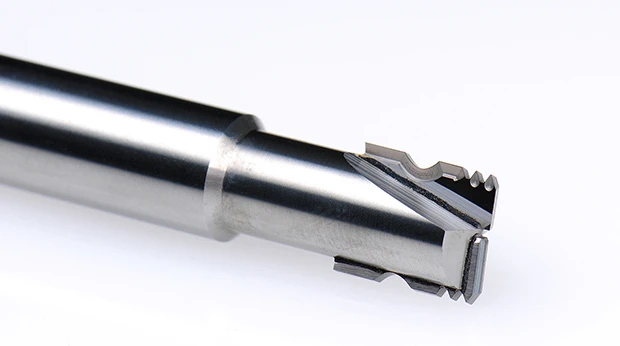
Rollomatic, developer and manufacturer of CNC machines for grinding cutting tools, cylindrical grinding and the laser machining of very hard materials, offers precision and functionality for the user.
(Photo right) Measurement of the cutting edges in three different laser cutting processes – with and without defined cutting edge radius.
Processing ultra-hard materials such as natural diamond, PCD, or CVD diamond remains a challenge that tool manufacturers can overcome with the right machine and the right technology, such as the Lazersmart 500, which produces extremely good surface quality on the cutting edge and has consequently already proved its worth in all sectors.
"Its users are thoroughly impressed," says Philippe Uebelhart, managing director at Rollomatic SA. "Not only does it allow very high-grade cutting edge quality and surface quality on inserts and cylindrical tools, it is highly accurate in profiling too. This ensures huge competitive advantages for users."
With 5-axis interpolated, the diameter range can reach 75mm for all operations in one single chucking. Furthermore with the excellent surface quality and extremely sharp cutting edges, there is no need for subsequent cleaning.
(Photo right) The Lasersmart 500 produces PCD profile tools in one chucking.
At this year's GrindTec, Rollomatic will present a new HSK63 clamping system for the high-precision laser machine center. Another particular highlight will be the possibility of also producing a cutting edge with a defined radius. This option opens up completely new possibilities for the customer.
High-precision (non-) cylindrical grinding
High-precision, state-of-the-art cutting tools are unimaginable without completely true running blanks. Rollomatic has developed the right machines for their efficient production – the ShapeSmart NP3 cylindrical grinding machines and the five-axis NP5 for peel grinding process tools in a grinding diameter range of 0.025mm to 25.0mm. NP3 and NP5 are now designed in such a way that they reliably grind bars with a length of 450mm (or a grinding length of 400mm) and diameters of up to 16mm.
"In what is a particularly practical feature, ten different tool profiles can be programmed and produced with a single setting – the operator doesn't have to intervene or select any further settings,” Uebelhart says. “In addition, both ShapeSmart machines allow the simultaneous rough and finish grinding of blanks and finished tools. After a short process time and in a single chucking, the user receives perfectly processed tools with a mirror finish surface."
(Photo left) The ShapeSmart NP5's newly patented grinding process is used for the high-precision production of non-round punches.
Rollomatic will also present a newly patented grinding process at GrindTec, which will greatly benefit ShapeSmart NP5 customers. This cylindrical grinding machine will allow the production of non-cylindrical punches as well as stamping and forming tools with complex forms and a diameter-length ratio of over 200x D in one chucking. The NP3 machine will be presented with features including an expanded robot loader capacity.
Tool grinding made easy
Loader capacities have also been increased on the GrindSmart 629XS/XW and 529XS/XW machines. This enables more tools to be loaded, thereby doubling the time in which the machine works autonomously. The flexible grinding wheel changer also contributes to this by automatically changing the wheel packs. In addition, a practical job manager allows the uninterrupted production of different tool geometries from the same blank size. "Thanks to our practical software with monitoring systems, the facilities can run unmanned at weekends, thereby reliably ensuring production with tolerances within fewer µm," Uebelhart says. Constant measuring ensures that temperature fluctuations, grinding wheel wear and other deviations are discovered and immediately offset.
Trade fair visitors will also have the chance to take a closer look at the new GrindSmart 529XF – a focal point of the Rollomatic stand. "The new 6-axis grinding center with integrated 3D simulation module offers unlimited tool production possibilities. However, this all-rounder is specifically designed for processing extremely long drilling tools," says Philippe Uebelhart. To be more exact, the 529XF grinds drilling tools with a cutting length of up to 300mm, diameters of 0.2mm to 12mm and a diameter-length ratio of up to 200x D. The developers have also put some thought into the design – the compact GrindSmart 529XF offers up to 25% in space savings compared to similar systems.
(Photo right) Rollomatic is developing a humanoid robot aimed at supporting workers.
In addition to the grinding machines, Rollomatic will also present the latest version, 1.19, of the VirtualGrindPro software. This offers extra flexibility in tool development, for example, in the form of new calculations and algorithms for drilling tools and the integration of the BurCalc rotating burs program. Benefiting grinding process precision and reproducibility, the software includes optimized functions for tool checking as well as a new module for measuring the grinding wheels during the process.
Well prepared for Industry 4.0
Who wouldn't want to receive machine or production statuses and notifications of monitoring or repair procedures – at any time, via any device or medium, from anywhere? Something that production managers can currently only dream of could soon be a reality. Rollomatic is making its contribution to the industry's latest generation of machines with its new machine monitoring systems, Rmonitor and Rconnect. When used on their tool and cylindrical grinding machines, they display data such as current tool in production, end of production, or graphic status history and other relevant parameters. Visitors to GrindTec will be granted a sneak preview of the system.
The use of industrial robots that no longer function as mere machines but as partners is also fast approaching. Rollomatic is working intensively on highly developed, humanoid robots aimed at supporting traditional robot units and increasing the productivity and profitability of customer-specific processes. The dual-arm NEXTAGE robot is able, to a certain extent, to take on demanding and laborious tasks and carry out easy and repetitive activities. Several hundred of these robots are already being used in various factories. A model of the cooperative NEXTAGE robot will be on display at the trade fair.
(Photo right) The Rmonitor and Rconnect machine monitoring systems ensure maximum productivity.
From March 16–19, 2016, Rollomatic will present its latest innovations in hall 5, booth 5102, at GrindTec in Augsburg.
Fast and reliable tool and cylindrical grinding, high-precision laser machining and state-of-the-art software – Rollomatic's solutions are able to satisfy and even exceed this challenging market's demand for ever increasing productivity. In hall 5, booth 5102 at GrindTec in Augsburg, the company will present some of its high-efficiency grinding machines with new equipment features and software updates for precise tool production.
Source: Rollomatic SA
Latest from Today's Medical Developments
- THINBIT’s MINI GROOVE ‘N TURN Acme threading inserts
- CMMC Roll Out: When Do I Need to Comply? webinar
- Metabolic research uses Siemens gas analyzers to deliver results with 99.9999% resolutions
- Mazak’s SYNCREX 38/9 Swiss-type production turning machine
- Current economic and geopolitical realities demand decisive action
- Collaboration to advance pediatric medical technologies
- Guyson's TR-1000 Custom Vertical Blast System
- Intelligent data for the digital factory