
MICROCARE
The production of electronic medical devices, especially those having intricate printed circuit board assemblies (PCBAs), requires strict quality control measures to guarantee best performance, reliability, and safety. Due to these devices’ pivotal role in patient care, process validation becomes a critical phase in manufacturing. It ensures consistent adherence to production procedures, thereby confirming the products consistently meet rigorous quality standards.
Within this framework, careful cleaning procedures are essential to cut contaminants potentially compromising device functionality and integrity. Vapor degreasing stands out as a highly effective cleaning method, offering numerous advantages compared to traditional methods, such as aqueous cleaning, and ensuring compliance with regulatory standards.
The vital role of cleaning
Process validation is crucial in the manufacturing of electronic medical devices to ensure consistent and reproducible outcomes throughout all production stages. Cleaning plays a vital role in this process, especially for devices incorporating intricate miniaturized PCBAs.
Electronic medical devices often feature complex designs and delicate PCBAs extremely sensitive to contamination. The cleaning procedures implemented during manufacturing are specifically designed to remove a variety of contaminants, such as organic residues, flux remnants, and particulates. These contaminants can affect device performance, reliability, and the overall success of the validation process.
The presence of contaminants on PCBAs can lead to electrical failures, corrosion, and malfunctioning devices.
Moreover, they can disrupt later manufacturing steps, potentially reducing the operational lifespan of the device and compromising patient safety. In manufacturing, contamination poses significant challenges to quality control processes, often resulting in increased rejection rates and decreased production efficiency. For implantable medical devices, the risks are even higher, as contaminants can interfere with crucial sterilization procedures.
Regulatory bodies, including the U.S. Food and Drug Administration (FDA), International Organization for Standardization (ISO), and IPC International, have set up stringent guidelines for cleaning and validation practices in medical device manufacturing. Adherence to these standards proves regulatory compliance and ensures products consistently meet the exacting performance requirements of the healthcare industry. Effective cleaning processes, when properly integrated into the overall validation strategy, contribute significantly to keeping product integrity throughout the manufacturing lifecycle.
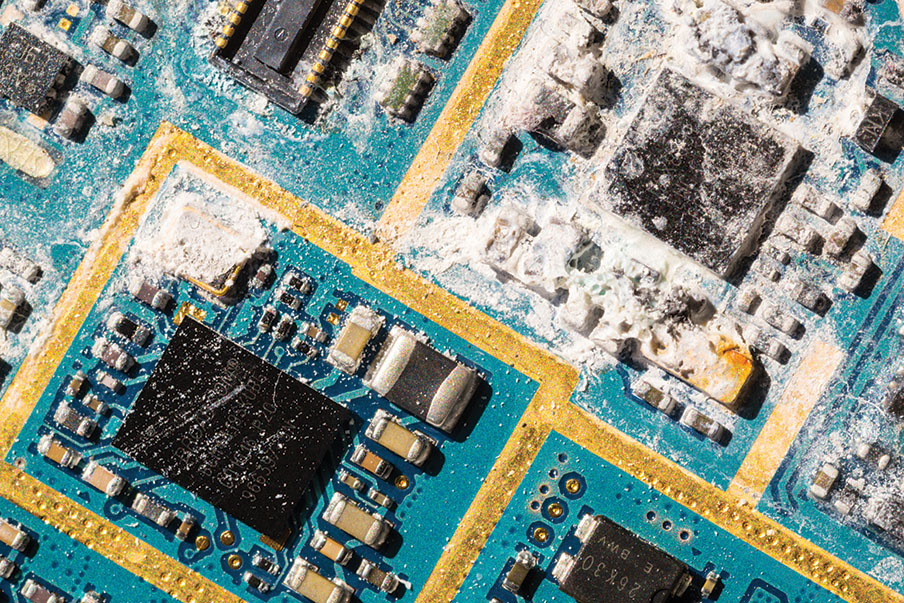
An effective cleaning approach
Vapor degreasing is a highly effective and sophisticated cleaning technique for electronic medical devices. This method uses a closed-loop system including two chambers: the boil sump and the rinse sump. A specially formulated cleaning fluid is heated to produce vapor in the boil sump. The components are immersed in the heated fluid for cleaning and then moved to the rinse sump for a final rinse and drying phase. This process ensures the assemblies come out clean, dry, spot-free, and ready for any further manufacturing stages, including assembly, finishing, sterilization, or final packaging.
One of the most significant advantages of vapor degreasing is cleaning components and PCBAs with complex geometries and delicate parts without causing damage. The cleaning fluids used in vapor degreasers are engineered with low boiling points, low surface tension, and low viscosity. These characteristics enable the cleaning fluid to penetrate tight spaces, dissolve contaminants, and evaporate without leaving residues. This thorough cleaning is crucial for ensuring functional reliability of medical devices.
Vapor degreasing’s consistency and repeatability also makes it an excellent choice for process validation. Once refined, the vapor degreasing process stays stable for thousands of cycles, minimizing the need for frequent monitoring, tracking, and maintenance.
Vapor degreasers are also highly scalable, accommodating different batch sizes and assembly geometries. This flexibility allows for consistent cleaning results regardless of the size or complexity of the components. Stable and repeatable cleaning processes simplify validation requirements, ensuring all procedures are adhered to.
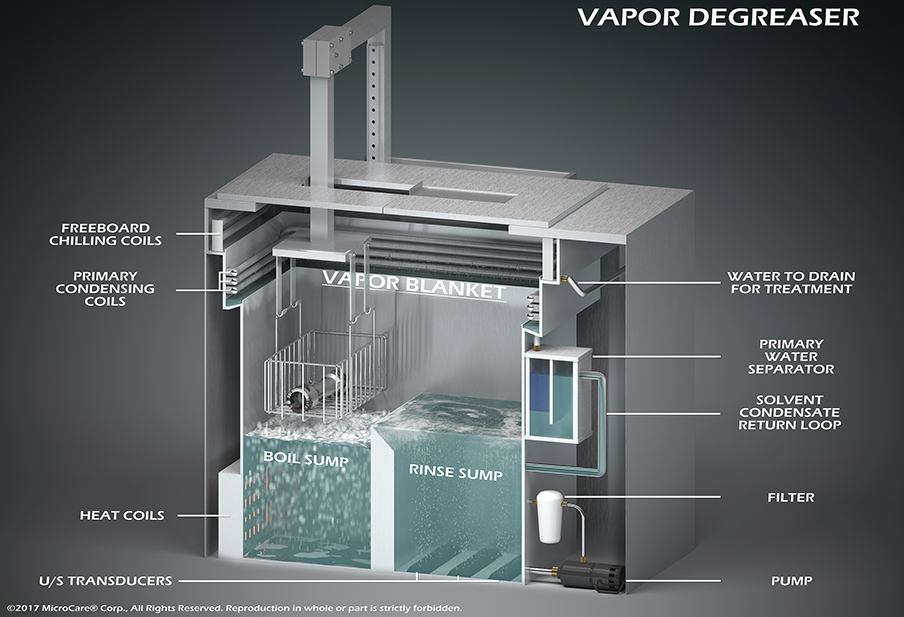
Meeting regulatory standards
Process validation in medical device manufacturing must adhere to stringent regulatory standards. The FDA’s Quality System Regulation (21 CFR Part 820) and ISO 134851, for example, emphasize the importance of validated processes in ensuring consistent product quality. When properly implemented, vapor degreasing can contribute to meeting these regulatory requirements.
The FDA defines process validation as “establishing by objective evidence that a process consistently produces a result or product meeting its predetermined specifications”2. Vapor degreasing aligns well with this definition due to its consistent and reproducible performance. This cleaning method can be precisely controlled, checked, and documented to prove process control.
Ensuring reliability, quality assurance
Process validation proves the cleaning method consistently achieves the desired level of cleanliness. It verifies process parameters, such as cleaning agents, temperature, time, and equipment, are properly controlled and optimized to consistently achieve the required level of cleanliness for the device throughout the manufacturing process.
Effective cleaning protocols help manufacturers ensure PCBA performance and prevent adverse effects resulting from residues or contaminants. This quality assurance aspect is critical in ensuring the long-term reliability and safety of electronic medical devices.
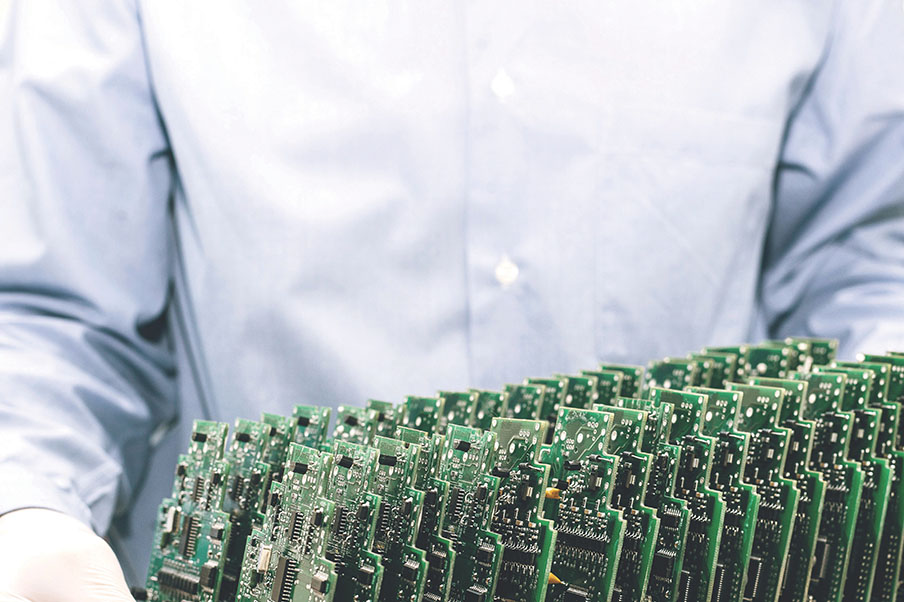
Environmental and operational benefits
Modern cleaning fluid technology has advanced to make vapor degreasing an environmentally sound and operationally efficient choice. These fluids follow local and national air quality regulations and operator safety requirements. Vapor degreasers are energy-efficient and occupy a small footprint in cleanrooms, reducing overall operational costs. Additionally, they don’t generate dust, fumes, or moisture, helping support cleanroom conditions and minimizing bioburden risk. These environmental and operational advantages contribute significantly to meeting validation protocols.
Developing standard operating procedures
Defining cleaning protocols is the first step toward successful process validation. Manufacturers must set up clear, detailed cleaning procedures outlining each step of the vapor degreasing process. Ensuring they align with regulatory standards and are carefully documented is crucial.
An essential part of process validation is the development and implementation of standard operating procedures (SOPs). SOPs are detailed, written instructions describing how to perform a specific task or process consistently and effectively. In the cleaning of electronic medical devices, these SOPs work with established cleaning protocols to ensure a thorough and compliant cleaning process.
- SOPs should outline step-by-step instructions for the vapor degreasing process, including equipment setup, operation, and maintenance.
- They should specify the exact parameters to be used, such as cleaning fluid type, temperature, and cycle times.
- SOPs must include quality control checkpoints and acceptance criteria to ensure consistent cleaning results.
- Regular review and updating of SOPs are necessary to reflect process improvements or changes in regulatory requirements.
Implementing well-documented SOPs ensures consistency in the cleaning process, helps personnel training, and supports regulatory compliance. These procedures form a critical part of the overall quality management system, support regulatory compliance, simplify audits, and contribute significantly to the success of process validation.
Validation for reliability
Process validation through effective cleaning procedures ensures consistent quality and reliability in electronic medical device manufacturing. Vapor degreasing used with modern cleaning fluids is an effective method that cleans complex PCBAs. By incorporating vapor degreasing into validation protocols, manufacturers can achieve reproducible cleaning results, ensure compliance with stringent regulatory standards, and enhance product integrity. As the medical device industry advances, the emphasis on validated cleaning processes remains critical in safeguarding patient safety and driving innovation in healthcare technology.
MicroCare
Get curated news on YOUR industry.
Enter your email to receive our newsletters.Latest from Today's Medical Developments
- EMI completes installation of 128-axis CNC turning & milling machine
- Ottobock invests in innovative technologies from MIT start-ups
- Air Turbine Technology's high-speed live tools for Swiss Lathes
- Sandvik announces several software acquisitions
- Dart Controls’s EZ VFD, variable frequency drives
- #55 - Manufacturing Matters - A Primer on Defense Contract Manufacturing
- Sound waves for stable cleanliness in manufacturing
- Boston Scientific to acquire SoniVie