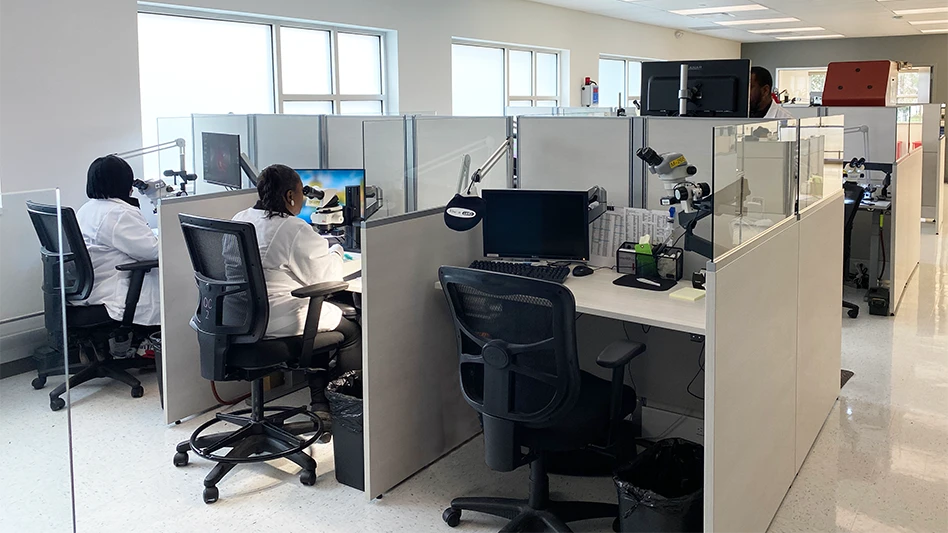
Norman Noble
Norman Noble Inc., the world’s leading contract manufacturer of next-generation medical implants, has expanded their In-Process and Final Inspection department. The new dedicated space in Noble’s Medtech I Facility combines two Quality Control Labs into one larger lab. The move increases total lab space by approximately 20% and allows for a more efficient layout and product flow. With this updated lab, Norman Noble has improved delivery time of nitinol shape-set implants, including vascular stents, transcatheter heart valve components, neurovascular flow diverters and more.
“We’ve invested in streamlining our quality control processes to support customer projects,” says David Saletrik, director of quality assurance of Norman Noble. “Consolidating the quality control labs and relocating them adjacent to our Shipping/Receiving Department will allow us to better serve our customers and improve delivery times.”
Norman Noble supports customers with ultra-precision micromachining of medical devices from initial prototype through all stages of FDA approval to full-scale manufacturing. The company’s quality control labs are essential to its customers’ ability to bring next-generation medtech devices and implants to market quickly, while meeting quality, delivery, and regulatory requirements.
Latest from Today's Medical Developments
- Auxilium Biotechnologies prints medical devices on the International Space Station
- KYOCERA SGS Precision Tools’ APEX Application Expert
- North American robotics market holds steady in 2024 amid sectoral variability
- Evident’s DSX2000 digital microscope
- Ferrocene becomes first Rust toolchain to achieve IEC 62304 qualification
- Germany expects a major decline in production in 2025
- Learn what you need to comply with CMMC requirements
- VersaBuilt’s CNC automation possibilities