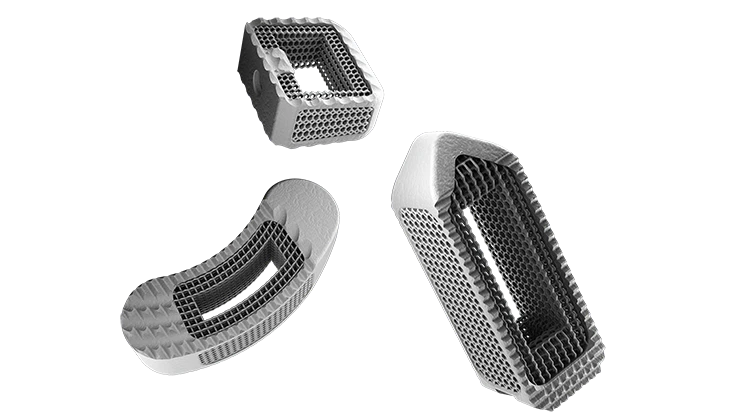
Nexxt Spine
“Additive is booming,” says Alaedeen Abu-Mulaweh, director of engineering at Nexxt Spine a medical device company focused on designing, manufacturing and distributing innovative spinal implant solutions.
In a release from the company, which designs and manufactures 100% of its implants from its facility in Noblesville, Indiana, only began its additive manufacturing (AM) journey two years ago – and in that time has come a long way. So, the company is taking delivery of its fourth and fifth Concept Laser Mlab 100R machines.
Established in 2009 and initially producing specialty spinal screws, rods, and plates using conventional subtractive manufacturing techniques, Nexxt Spine’s first investment in metal additive manufacturing (MAM) was the acquisition of its a Concept Laser Mlab 100R in 2017.
“We used the first Mlab primarily for R&D purposes, but we soon realized that further investment in additive technology could add value not only to our overall growth strategy, but also at a clinical application level with the ability to develop implants with very intricate micro-geometries that could maximize healing. Over the past two years, we have made a seamless jump from R&D to serial production and in doing so have significantly accelerated the time from concept to commercialization,” Abu-Mulaweh says.
The investment in Concept Laser Mlab machines has allowed the Nexxt Spine team to take ownership of the entire design, production, and distribution process in-house, eliminating the need for contract manufacturers and accelerating the speed of development and commercialization.
Focus on core science
The team at Nexxt Spine are pioneers in the design and development of spinal fusion implants that incorporate interconnected micro-lattice architectures with the goal of promoting osteoconduction, osteointegration, and bony fusion.
Launched in 2017 was its Nexxt Matrixx System – a collection of porous titanium spinal fusion implants that interweave highly differentiated surface texturing technology with novel 3D-printed cellular scaffolding. Deviating from the status quo, where other medical manufacturers have used AM to develop devices that directly mimic bone’s trabecular geometry, Nexxt Spine blends cellular porosity, inspired by natural bone biology, with core engineering fundamentals to develop structurally sound devices, optimized for fusion.
“Titanium – porous or otherwise – is physically incapable of biological remodeling, so using additive to directly mimic the structural randomness of bone doesn’t make a whole lot of sense. Rather than simply looking like bone, Nexxt Matrixx was designed with functionality in mind to fulfil our vision of actively facilitating the body’s natural power of cellular healing,” says Abu-Mulaweh.
“We are seeing ongoing adoption of AM in the orthopedic industry and an exciting shift from research and development to serial production. Early innovators like Nexxt Spine are scaling up and there is a significant increase in production volumes,” says Stephan Zeidler, senior global and key accounts director for the medical sector at GE Additive.
Additive opens new frontiers
With design, manufacturing, and distributions functions in-house, combined with the shift to serial AM production, Nexxt Spine is well-placed to service and scale to meet the growth in demand for spinal fusion device.
Latest from Today's Medical Developments
- Midwest DISCOVER MORE WITH MAZAK
- Reshoring survey to provide insight for US industrial policy
- NB Corporation of America's ball splines
- Zimmer Biomet to acquire Paragon 28
- Industrie 4.0 award for Paul Horn GmbH
- CMMC requirements and your business
- Stryker exiting spinal implant business
- Perfecting the manufacture of microscopically thin films for tech, medical applications