
CREDIT: MINUS K TECHNOLOGY
As the need for nano-precision has become increasingly important in many fields of research and manufacturing – such as microelectronics fabrication, laser/optical system applications, life sciences, materials, aerospace and biological research – so has the need to implement vibration isolation technology for stabilizing academia’s and industry’s most critical instrumentation to facilitate operation under extremely precise requirements operating at atomic-scale resolutions.
The need to eliminate vibration
The need to provide adequate vibration isolation presents an increasingly important and complicated challenge, particularly at very low frequencies.
Vibration influencing high-resolution sub-micron instrumentation can be caused by a multitude of factors. Within the building itself, the heating and ventilation system, fans, pumps and elevators are just some of the mechanical devices that create vibration. How far away sensitive instrumentation is from these vibration sources, and where in the structure the equipment is located, will determine how strongly the equipment will be influenced. External to the building, the equipment can be influenced by vibration from adjacent road traffic, nearby construction, aircraft, and even wind and other weather conditions that can cause movement of the structure.
These internal and external influences cause low-frequency vibration in the 0.5Hz to 50Hz range, which is transmitted through the structure and into sensitive parts of instrumentation, compromising resolution, image quality, and the integrity of data.
Inadequate isolation
Many vibration isolators, particularly at frequencies below 10Hz, deliver limited isolation vertically and even less isolation horizontally. In fact, such isolators create vibration isolation problems in the region of their resonant frequency. All isolators will amplify at their resonant frequency then start isolating above this frequency. Pneumatic isolators, for example, will amplify vibration in a typical range of 1Hz to 4Hz. Sensitive instruments, which are typically manufactured with internal pneumatic isolation, are, therefore, often subject to problems with vibration.
Another option in use is active feedback electronic-force cancellation systems, which incorporate the use of sensors, actuators, and control algorithms to detect and mitigate vibration.
Active systems have limited dynamic range, however. They have a tough time dealing with vibration input that is either too large or too small. Vibrations that are too large can cause the system to go into positive feedback. Vibrations that are too small may not even be detected.
To achieve a high level of precision in vibration-critical applications, feedback electronic-force cancellation systems must balance a complexity of inertial feedback in response to incoming vibrations. This can be challenging for active systems when the inertial feedback is applied to incoming low-frequency vibrations horizontally.
As sub-micron research continues to advance at an accelerated rate, the need to protect sensitive instrumentation – like electron microscopes, scanning tunneling microscopes, laser interferometers, and optical profilers – with better vibration isolation is critical.
Negative-stiffness – the technology behind sub-micron advanced technology
There is a more advanced vibration isolation technology in use when it comes to protecting sensitive sub-micron instrumentation to low-Hertz vibrations. Introduced in the mid-1990s by Minus K Technology, Negative-Stiffness vibration isolation has been widely accepted for vibration-critical applications, largely because of its ability to effectively isolate lower frequencies, both vertically and horizontally.
Used in a broad spectrum of applications including microscopy, nanotechnology, biological sciences, semiconductors, materials research, zero-g simulation of spacecraft, and high-end audio, Minus K’s Negative-Stiffness isolators are supplied to leading manufacturers of scanning probe microscopes, micro-hardness testers and other vibration-sensitive instruments and equipment. Negative-Stiffness isolators are being used in more than 300 leading universities and government laboratories in 52 countries.
Negative-Stiffness vibration isolators are unique in that they operate purely in a passive mechanical mode. They do not require electricity or compressed air. There are no motors, pumps or chambers, and no maintenance because there is nothing to wear out.
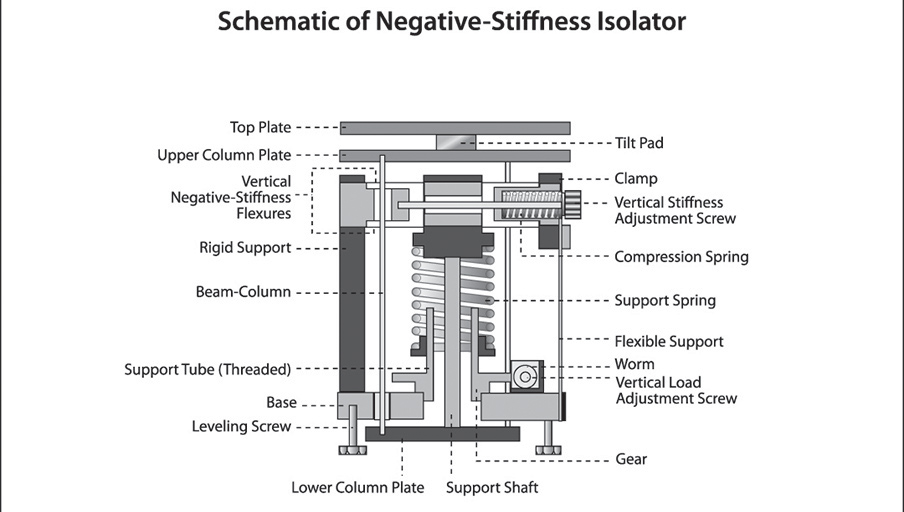
“Vertical-motion isolation is provided by a stiff spring that supports a weight load, combined with a Negative-Stiffness mechanism,” says Erik Runge, vice president of engineering at Minus K. “The net vertical stiffness is made very low without affecting the static load-supporting capability of the spring. Beam-columns connected in series with the vertical-motion isolator provide horizontal-motion isolation. A beam-column behaves as a spring combined with a negative-stiffness mechanism. The result is a compact passive isolator capable of very low vertical and horizontal natural frequencies and high internal structural frequencies.”
Negative-Stiffness isolators achieve a high level of isolation in multiple directions, with the flexibility of custom-tailoring resonant frequencies to 0.5Hz vertically and horizontally (with some versions at 1.5Hz horizontally)*. When adjusted to 0.5Hz, the isolators achieve approximately 93% isolation efficiency at 2 Hz; 99% at 5Hz; and 99.7% at 10Hz.
(*Note that for an isolation system with a 0.5Hz natural frequency, isolation begins at 0.7Hz and improves with increase in the vibration frequency. The natural frequency is more commonly used to describe the system performance.)
Minus K’s Negative-Stiffness vibration isolation has become a preferred system for research into sub-micron advanced technology. From the discovery of exoplanets to the characterization of nanoparticles, much of our most advanced technological research has relied on ultra-sensitive Negative-Stiffness vibration isolation systems capable of reducing motion to less than 0.5 Hertz and enabling precision research at the sub-atomic level.
Negative-stiffness isolation and the search for exoplanets
Astronomers have confirmed more than 5,000 exoplanets orbiting distant stars. There are a few aspects that are needed to characterize an exoplanet. One is the size of the planet, and the other is the mass of the planet.
The Keck Planet Finder (KPF) has emerged as a powerful tool, both for the discovery and follow-up of planets, and for unprecedented insight into stellar behaviors. Located at the W. M. Keck Observatory on the summit of 13,796ft Mauna Kea in Hawaii, KPF is the world’s most advanced high-resolution spectrometer for visible wavelengths. KPF saw first light in November 2022.
“KPF was designed from the ground up to track the spectral fingerprints of stars to better than one-part-per-billion precision,” says Kodi Rider, project manager of KPF at UC Berkeley Space Sciences Lab. “This scale of measurement represents a significant technological challenge and required every layer of the KPF system be optimized to maximize performance.”
“We became concerned about vibrations when measuring at this level of precision,” explained Rider. Such as external vibrations from pumps and machines, and from the Keck 10-meter diameter mirrors themselves rotating. KPF’s tolerance for mirror motions is less than an angstrom, which for scale is half the width of a hydrogen atom.
“After a considerable search, we were able to find only one technology with the capability to completely isolate vibrations at the level required for the KPF spectrometer,” Rider adds. “That technology is Negative-Stiffness vibration isolation.”
Negative-stiffness isolation and dynamic mapping of neuronal wave patterns in the brain
Professor Jian-Young Wu, Ph.D., with the Department of Neuroscience at Georgetown University Medical Center has for the past 20 years been researching epilepsy and brain processing functions in the mammalian neocortex, shedding new light into neuronal propagating wave patterns and neurological conditions such as epilepsy.
The micron-level research utilizes voltage-sensitive dye imaging for viewing the spatiotemporal patterns of neuronal populations in the neocortex. Recently, Dr. Wu’s lab has discovered a very early event in the development of epilepsy.
“In cortical tissue, epilepsy waves initiate from dominant sites,” Wu says. “The dominant sites form within minutes, and multiple sites take turns to initiate epileptic waves. We believe that a dominant site is the very early version of seizure focus. Preventing the formation of a seizure focus may help to stop epilepsy in its early stage.”
“We have been using four Negative-Stiffness vibration isolation units in our laboratory for many years to facilitate our research into dynamic mapping of neuronal propagating waves,” Wu explains. “Negative-Stiffness has enabled our lab to get vibration isolation down to a level of 0.5Hz. We have never been able to achieve this prior. This effectively cancelled out any vibration noise difficulties that were inhibiting our image and data readings. Negative-Stiffness vibration isolation has proven to be a necessary and critical support for enabling our research.”
Negative-stiffness isolation and the detection of gravitational waves from black holes
Albert Einstein predicted the existence of gravitational waves in 1916, but only in the last 10 years has technology become powerful enough to permit detecting these waves and harnessing them for science.
The GEO600 Ground-Based Interferometric Gravitational Wave Detector located at the Max Planck Institute for Gravitational Physics (also known as the Albert Einstein Institute) in Hannover, Germany, has played a pivotal role in the development and testing of new technologies for the detection of tiny space-time ripples of gravitational waves.
Most notably on September 14, 2015, when GEO600 technology was employed in the Laser Interferometer Gravitational-Wave Observatory (LIGO) in Germany to make the first detection of gravitational waves from a binary black hole merger, confirming Einstein’s vision of gravitational waves and allowing a fascinating and unique view into the dark side of the cosmos.
“With laser interferometry we can retrieve information from spaces in the universe that is otherwise not accessible, and we can look back in time much further,” says Dr. Harald Lück, Research Group Leader for the Laser Interferometry and Gravitational Wave Astronomy division of the Albert Einstein Institute.
The central elements in all gravitational wave detectors are mirrors used to direct the laser beams. A significant challenge in gravitational wave interferometry is to get rid of disturbances like air pressure and temperature fluctuations, as well as seismic vibrations of all sorts that would conceal a signal.
“The GEO600 mirrors are supported by Negative-Stiffness vibration isolators which have made this discovery possible, and provided pivotal support for GEO600’s continuing research into the nature of gravitational waves,” Lück adds.
Enabling a technological evolution
We are on the forefront of a technological evolution with sub-micron research in the fields of microelectronics, laser/optical systems, life sciences, materials, aerospace and biological research.
Unpinning this research is the necessity for extremely low-Hertz vibration isolation of our most critical instrumentation to facilitate its operation at atomic-scale resolution. This demands a very unique capability which is most adequately filled by Negative-Stiffness vibration isolation.
About Minus K Technology Inc.
Minus K Technology Inc. was founded in 1993 to develop, manufacture and market state-of-the-art vibration isolation products based on the company’s patented negative-stiffness technology. Minus K products are used in a broad spectrum of applications including microscopy, nanotechnology, biological sciences, semiconductors, materials research, zero-g simulation of spacecraft, and high-end audio. The company is an OEM supplier to leading manufacturers of scanning probe microscopes, micro-hardness testers and other vibration-sensitive instruments and equipment. Minus K customers include private companies and more than 300 leading universities and government laboratories in 52 countries.
Latest from Today's Medical Developments
- Sound waves for stable cleanliness in manufacturing
- Boston Scientific to acquire SoniVie
- Registration is open for April’s Manufacturing Lunch + Learn!
- Innovative medical solutions for surgical instruments
- ANCA Academy - elevate skills in operating ANCA CNC machines
- Aerospace Industry Outlook webinar is back by popular demand
- Automation Webinar with Visual Components
- Maximizing efficiency in today’s manufacturing environment