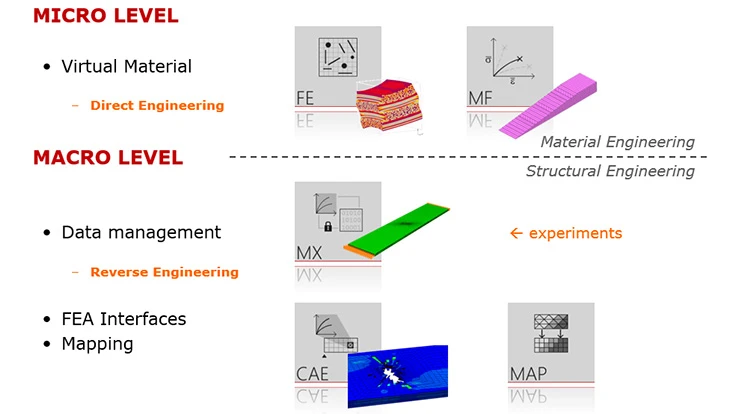
Additive manufacturing of plastics and composites is evolving from rapid prototyping to industrial production. Printer manufacturers, material suppliers, and end-users need predictive simulation tools to bring the additive manufacturing efficiency and performance to the next level required by the industry.
Digimat-AM, the latest edition to the Digimat platform, is the ultimate simulation solution for manufacturing process of Fused Filament Fabrication (FFF), Fused Deposition Modeling (FDM) and Selective Laser Sintering (SLS) of reinforced materials. For printer manufacturers and end-users, the part fidelity is the top challenge to overcome. Digimat-AM allows the engineer to predict warpage and residual stresses of a polymer part as a function of the manufacturing process parameters. With Digimat-AM, users can further optimize the process and minimize the part deformation right at their fingertips. Virtual engineering is the solution to minimize printing trial and errors because it enables the user to explore the process sensitivity to manufacturing parameters.
By applying multi-scale material modeling techniques to the additive manufacturing of polymers (unfilled and reinforced), Digimat’s virtual material compounding and characterization is a key enabler for customers developing new materials. Virtual engineering allows the engineer to significantly reduce physical tests, understand the key parameters driving the material’s behavior, and easily create new material systems, such as lightweight lattices.
“With solutions for materials development, process simulation, and printed part performance, Digimat Additive Manufacturing is a completely innovative solution that’s fully dedicated to reinforced plastics and composites, allowing its users to ‘print it right the first time” says Roger Assaker, CEO of e-Xstream engineering, chief material strategist of MSC Software.
Digimat’s latest release not only opens new horizons and a new way of designing but also brings some nice additional features. Digimat material model reverse engineering capabilities have been extended for creep and crash performances to better support material engineers. Structural engineers now benefit from significant CPU reduction when simulating the as-manufactured performance of MuCell components, or when simulating creep of plastic parts.
Latest from Today's Medical Developments
- Soft joint model for robots
- TANAKA PRECIOUS METAL TECHNOLOGIES’ Visi Fine
- Auxilium Biotechnologies prints medical devices on the International Space Station
- KYOCERA SGS Precision Tools’ APEX Application Expert
- North American robotics market holds steady in 2024 amid sectoral variability
- Evident’s DSX2000 digital microscope
- Ferrocene becomes first Rust toolchain to achieve IEC 62304 qualification
- Germany expects a major decline in production in 2025