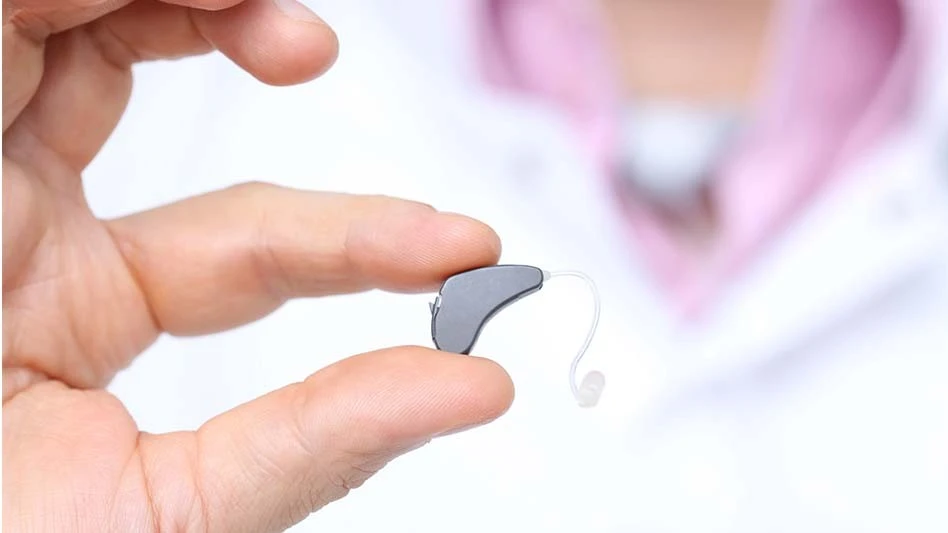
Sumitomo (SHI) Demag UK
By 2026 the global micro injection molded plastic market is projected to reach US $1.7M, at a CAGR of 11.2% from 2021. This boost is largely attributed to activities and developments in the medical, health care, and wellbeing sectors.
Aside from the pandemic, growth is being driven by advances in the home healthcare sector and an aging population. UK medical specialist at Sumitomo (SHI) Demag, Sam Carr, explores how the company’s smaller tonnage IntElect machine is responding to evolving production requirements.
Manufacturing small, high-precision thermoplastic components with micron tolerances is difficult because components can be as small as a single grain of granulate. The limit of what can be molded can be as light as 0.0003g, with walls as thin as 0.0004" and dimensional tolerances to ±0.0005".
Typical items being micro molded using this technique can comprise a wide range of surgical, endoscopic, point of care testing, diabetes management, drug delivery, and DNA research and sequencing devices. The expanding market includes catheter components, hearing aids, dental prosthetics, microfluidics, vials, caps, specimen cups, vacuum blood and serum collection tubes, syringes, and IV parts. These applications all have diminutive size and the need for total accuracy and zero defects during the molding process.
The process of micro injection molding isn’t dissimilar to creating larger parts. Shot-to-shot precision is where the main difference lies. If more material is allowed under the check valve on a 10g part, it isn’t a huge issue. However, if the part weight is 0.1g, it becomes a problem.
Historically, micro injection molders would have invested in specialist plunger systems or hydraulic machines. The latter meant dealing with variations in oil temperature and compressibility. These drawbacks are removed with the new generation of all-electric machines. Offering control not previously attainable, the IntElect delivers maximum precision whilst offering full mold safety, ensuring the sensitive cores and mold details aren’t damaged.
The Männer pipette exhibit which the SHI medical team collaborated on last year is testament to the level of control that can be accomplished with the latest generation of all-electric molding machines. Equipped with dynamic drive motors, the ready-to-go cleanroom IntElect S 130T molding cell is one of the few compact all-electric machines on the market with the mold space to accommodate a 64-cavity cluster tool and demolding robotics.
As well as the mid-size range, the IntElect thrives in the smaller tonnage, with the ability to supply screw sizes as small as 14mm on the 50T and 75T machines. This combination enables users to accomplish small shot weights with fine control required with micro molded components. For increased production capacity, some molders opt for a larger screw and barrel to allow them to mold larger parts, demonstrating the flexibility the IntElect offers without compromising the precision to the application.
Latest from Today's Medical Developments
- Stretchable, flexible, recyclable – this plastic is fantastic
- Discuss the upcoming year in manufacturing with GIE Media editors
- TDK Ventures invests in ANYbotics
- Our first webinar of 2025 highlights additive manufacturing
- Costa Rica, a global magnet for medical devices
- PhD student helps develop medical device for children with congenital heart defects
- Happy New Year
- Best of 2024: #1 Article – 2024 Forecast