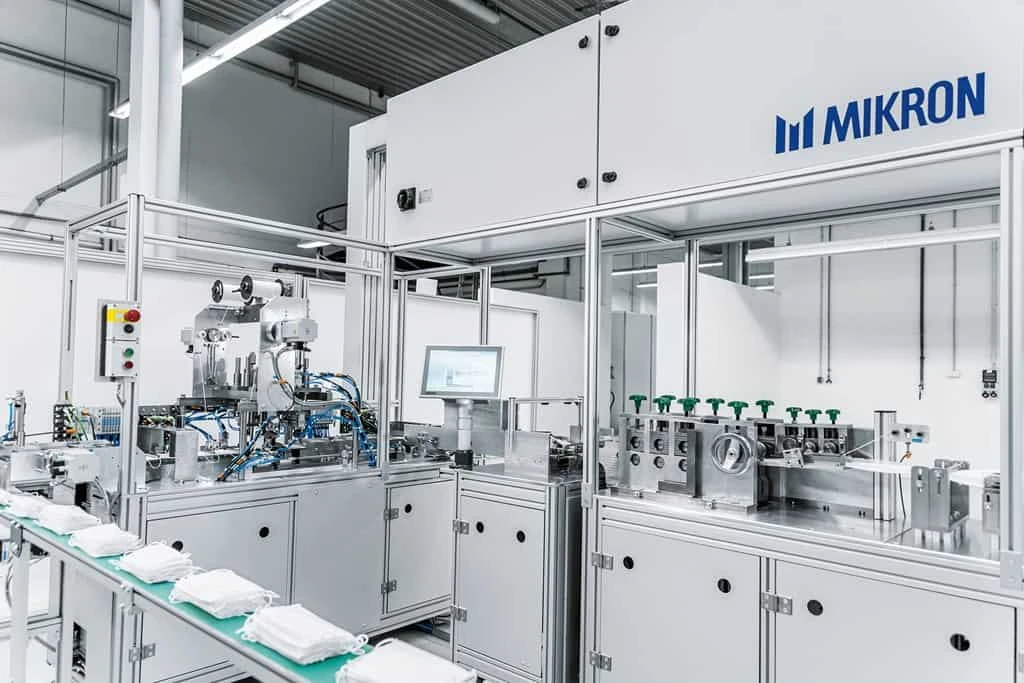
Disposable protective nasal-and-mouth masks are in short supply, but a manufacturing system from Swiss company Mikron could help fix this. The scalable system produces 50 to 100 face masks per minute, depending on the version. With engineering support from Festo, Mikron developed the system in just six weeks.
Mikron’s system fits in a 20ft shipping container which can also act as a clean room. The factory in a box could be located in front of a hospital, next to a shopping center, or near a school. The integrated air-conditioning system with air purification filters makes production possible even in places with high risk of viral contamination. With adequate raw materials, the system can operate autonomously for more than two hours.
“This reduces the number of people required to operate the system, and as a result, lowers the risk of infection,” explains Nils Rödel, general manager of Mikron Berlin. “The mini factory can produce protective masks in remote areas or even in crisis zones where meeting hygiene standards is most challenging.”
Just one system makes it possible to produce two million protective mouth-nose masks each month. The masks are based on meltblown non-woven fabric, which consists of many layers of fine fibers and thus filters out even the smallest particles such as bacteria and viruses from the air.
“Using official statistics, we calculated that medical personnel in Germany alone need at least 50 million disposable protective mouth-nose masks per month,” Rödel reports. “We could meet this demand with 25 containers.”
Eliminating the need for transport makes the end product less costly. The system, depending on how it is configured, can make packs of ten masks or individual ones, shrink-wrapped for cleanliness and packaged in printed bags and boxes if required.
“Packaging masks involves docking an automated station developed by pi4 robotics GmbH, Berlin, a project partner,” Rödel says.
Reliable supply of system components
Electric and pneumatic components from Festo ensure reliable transport, clamping, unwinding, shaping, and folding of the non-woven fabric. An ultrasonic sealing station seals the edges. The servo drives CMMT from Festo for controlling the electric drives EMMT are used in the application because they can be easily connected to programmable logic controllers (PLCs) from major manufacturers, including Beckhoff, Siemens, and Rockwell.

Pneumatic components from the Festo core product range installed in the system – such as the compact cylinder ADN, guided drive DFM, and round cylinder DSNU – are in stock worldwide and available for shipment within 24 hours. Global availability enables quick and reliable manufacture of systems for producing masks within a condensed timeframe. The pneumatic drives are actuated by MPA valves, and the safety valve MS6-SV-E ensures that safety-critical system components are exhausted and de-energized as quickly as possible in the event of a sudden emergency stop.
Thanks to its international production and sales network, products from Festo are available in 176 countries and enable systems to be built at locations around the world. This is entirely in keeping with the global open-source approach of Project CAROLA, which provided the impetus for designing the mask production system in a shipping container.
“The current travel restrictions make it extremely difficult for commissioning technicians to go where the systems are to be built,” Rödel says. “Mikron came up with a digitized solution. We use Microsoft HoloLens, which enables commissioning to be done virtually using an interactive 3D projection.”
Latest from Today's Medical Developments
- Turnkey robotic systems are already behind the times
- You can still register for March’s Manufacturing Lunch + Learn!
- HERMES AWARD 2025 – Jury nominates three tech innovations
- Vision Engineering’s EVO Cam HALO
- How to Reduce First Article Inspection Creation Time by 70% to 90% with DISCUS Software
- FANUC America launches new robot tutorial website for all
- Murata Machinery USA’s MT1065EX twin-spindle, CNC turning center
- #40 - Lunch & Learn with Fagor Automation