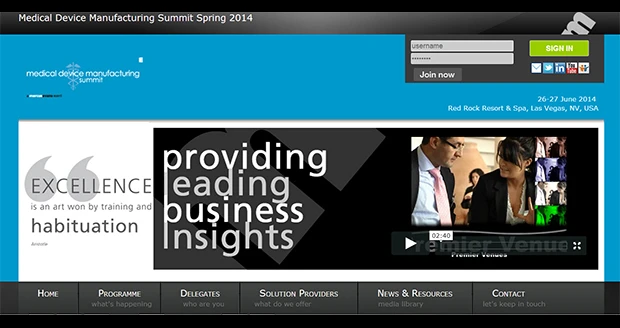
New York – “With pressure on costing and extended lifetime performance, medical device manufacturers need to focus on long-term costing and price stability for parts and components currently being designed,” advises Enrique Camacho of SIMTEC Silicone Parts LLC. Although cost is sometimes a deterrent for considering Liquid Silicone Rubber (LSR), it still pays off in the end, he explains.
SIMTEC Silicone Parts LLC is an American solution provider at the marcus evans Medical Device Manufacturing Summit Spring 2014 and the Medical Device R&D Summit Spring 2014, taking place in Las Vegas, Nev., June 26-27, 2014.
What is challenging medical device manufacturers today? How could LSR solve some of those issues?
In medical device manufacturing, the challenge is in finding an innovative, cost efficient solution while at the same time prioritizing safety and functionality. Medical devices need to perform perfectly every time; there is no room for error. Therefore, materials must be selected very carefully.
LSR is available in medical grades. It is biocompatible, hypoallergenic, flexible, durable, and transparent (unless pigmented); it can be autoclaved, and it is resistant to ultraviolet rays, stains, and extreme temperatures. All in all, LSR provides the level of performance that medical device applications demand.
What is LSR often not considered for, when in fact it would be ideal for the purpose?
For any new or existing application, where elastomers or rubbers are being considered. Any type of seal, gasket, membrane, coupler, housing, button, connector, valve, or dampener could potentially benefit from the superior temperature resistance, compression set, chemical resistance, and inertness that LSR offers.
Cost is always a factor when making a decision as to which materials to select for a medical device application, and occasionally cost is a deterrent in considering LSR. Medical OEMs sometimes make the difficult decision to compromise on part design and performance in order to save on up-front tooling costs. LSR is a material that pays off in the end, not only with improved part quality but also with the improved performance of the device. LSR stands up over time, even with repeated use. Its material price stability also allows for costs to be controlled over the lifetime of the program.
Could this material give manufacturers a competitive edge?
It certainly does, especially when the LSR or LSR 2-Shot (LSR/Thermoplastic) injection molding process is considered. The LSR 2- Shot injection molding process allows for the integration of multiple materials and functions, and for the production of complex components with one injection molding tool in one injection molding unit. By using this innovative technology, medical device manufacturers gain the competitive edge derived from combining the attributes of LSR (as mentioned earlier) and the material properties of a thermoplastic without the initial costs of several tools and the hassle of post-production assembly. The adhesion achieved, between the LSR and thermoplastic, when using this process, is unbeatable and only further enhances the performance of the end device.
What trends should manufacturers prepare for?
Whether it be wearable medical technology or advances in drug delivery systems, the medical industry is an ever-evolving and highly-innovative industry, and with the unique material characteristics of LSR the possibilities for this incredibly versatile material are endless!
Source: Marcus Evans
Latest from Today's Medical Developments
- Best of 2024: #8 Article – Perfecting the CMP process for surgical blades
- Best of 2024: #8 News – Johnson & Johnson to acquire Shockwave Medical
- Best of 2024: #9 Article – Strategy Milling combines old and new for precision dental restorations
- Best of 2024: #9 News – Global robotics race
- Best of 2024: #10 Article – Designing medical devices for every user
- Best of 2024: #10 News – 4 predictions for 2024: AI set to supercharge robotic automation
- Children’s National, FDA collaborate to advance pediatric device regulatory tools
- LK Metrology’s eco-friendliness CMMs