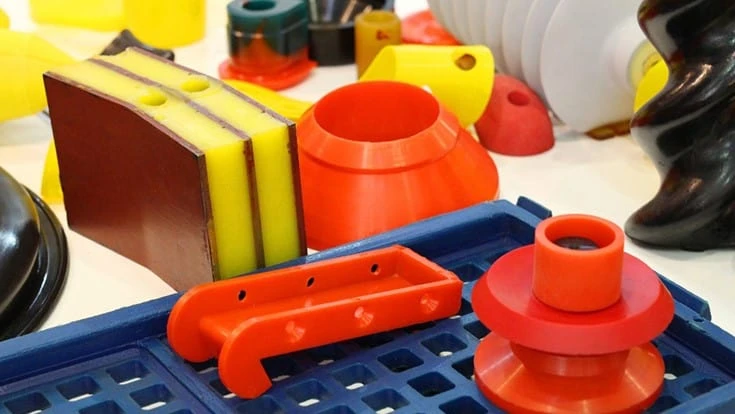
TPC Inc
Changing things up a bit for this weekend blog as I have a guest post from Will Bennett at TPU Inc. He's discussing the uses of polyurethane in medical devices and how versatile the material is. Happy reading and happy weekend!
Medical devices, implantables and polyurethane use - insights to consider about this versatile material
Polyurethane is a versatile material used in the medical industry in general materials such as catheters, medical gloves, and wound dressings. It’s also commonly found in larger devices such as medical beds and surgical tables.
Polyurethane is also compatible with the human body. It’s flexible, strong, and resistant to abrasions and chemicals. This is why polyurethane is used in short-term implant devices like feeding tubes, dialysis devices, intra-aortic balloon pumps, and surgical drains. The durability of polyurethane makes it useful for devices that rub against other materials.
Because polyurethane is non-allergenic, it is a safe alternative for people who have latex allergies. There is very little that polyurethane cannot do to improve upon most medical devices.
Molecular structure benefitting the human body
Polyurethane is made of elastomers, which have molecules that resemble human proteins. These elastomers are called thermoplastic polyurethanes or TPUs, and their unique molecular structure makes them unlikely to be absorbed by the human body. This makes polyurethane devices ideal for use in and around the human body.
Researchers found that polyurethane elastomers have properties that make them biomimetic and antithrombotic, so they are useful in the body.
So how does this benefit the human body?
When pacemakers and artificial hearts are made of polyurethane, the body is less likely to reject the implants. The newest artificial hearts have a combination of animal tissue coated with a special polyurethane called Angioflex to make the device smaller and less likely to be rejected.
Helping the medical communityPolyurethane devices make the medical community more reliable. The material is easy to work with and is noticeably strong.
Compare this to silicone or PVC, which have proven to be less reliable and not as easy to manage. Silicone does not bond with non-silicone materials. And PVC will leach toxic plastics over time, and it will become brittle when temperatures drop.
Polyurethane can be used in a soft form, as a foam, and in a semi-rigid and rigid form. It retains its shape and does not lose durability in any state. But, only devices that have been approved by the U.S. Food and Drug Administration (FDA) can be used in the medical industry.
Polyurethane, on its own, has not been approved by the FDA, but items made from it have been. To help polyurethane devices become FDA approved, the polyurethane supplier has to know the toxicology of its polyurethane formula. Devices that come in contact with tissue have to have substantial toxicology information.
Polyurethane might be more expensive than other polymers. But, the material works in ways that other polymers do not. Because they have so much versatility and compatibility with the human body, the higher price-per-pound is worth it for manufacturers.
Polyurethane medical tubing
One commonly used polyurethane medical device is the tube. Medical-grade polyurethane tubing is used in everything from catheters and balloon pumps to surgical drains and feeding tubes. Polyurethane tubing resembles both plastic and rubber, but without the toxicity and fragility that they both have.
Many versions of polyurethane medical-grade tubing work with a hydrophilic coating, which allows the tubes to function in moist areas of the body. This coating also makes it easier for medical professionals to insert tubes and move them once within the body.
Polyurethane tubing is universally used in the medical community because of the way it reacts with the body. Since polyurethane softens at body temperature, medical professionals can easily insert catheters and feeding tubes.
The biocompatibility of polyurethane lets patients remain comfortable, even when products are inserted into their bodies.

Manufacturing considerations
To mass-produce medical tubing, manufacturers look for the least expensive and most efficient methods. Most commonly, manufacturers use the extrusion method to get a consistent diameter both inside and outside of the tube.
Some manufacturers will co-extrude to mix materials, usually to combine a pressure-resistant material with a puncture-resistant one. Some materials only need to be 1/1000th of an inch thick.
Polyurethane balloon pumps
Another commonly used polyurethane medical device is the intra-aortic balloon pump. The biometric properties of polyurethane make this material useful for this device which is inserted into the aorta. The pump is a long catheter with a balloon at one end.
Surgeons insert the device into the femoral artery in one leg, so it can be pushed to the center of the aorta. Doctors use an X-ray to watch the device move through the body.
Once the device reaches its destination, the balloon at the end begins to inflate and deflate with the rhythm of the heart. The balloon lets the heart pump more efficiently by taking some of the heart’s workload.
There are risks attached to using the intra-aortic balloon pump. One is an infection, which happens to less than one percent of patients. Most infections are due to issues at the incision site, not because of the pump itself.
There have been cases of sepsis and bacterial infections from improperly inserted pumps. But, overall, the material makes the device safe.
Artificial heart
Hearts beat more than 2 billion times in an average lifespan. So, creating an artificial heart that could last that long was the dream of many scientists. Researchers discovered that the only artificial material that could replace human heart tissue was called segmented polyurethane. This material had shape memory as well as strength and flexibility.
Segmented polyurethane makes up nearly all of the artificial hearts that have been implanted since the first transplant in 1982. The polyurethane used in artificial hearts rarely fails, and it eliminates the cause of heart failure when implanted.
What separates segmented polyurethane from other forms of polyurethane is the material’s ability to return to its original shape. It does this by having a mixture of hard and soft segment copolymers that work together.
The closest non-medical use of segmented polyurethane is Spandex and Lycra, which also holds its shape despite the rubbing, heat, and movement of the humans who wear it.
In fact, it was the shape memory of Spandex that inspired researchers to use segmented polyurethane for artificial hearts.
Latest from Today's Medical Developments
- MedTech Innovator welcomes five new industry partners
- First Article Inspection for quality control
- The manufacturing resurgence is here – are you ready?
- Workholding solutions for your business
- ZOLLER events will showcase the company’s cutting-edge innovations
- THINBIT’s MINI GROOVE ‘N TURN Acme threading inserts
- CMMC Roll Out: When Do I Need to Comply? webinar
- Metabolic research uses Siemens gas analyzers to deliver results with 99.9999% resolutions