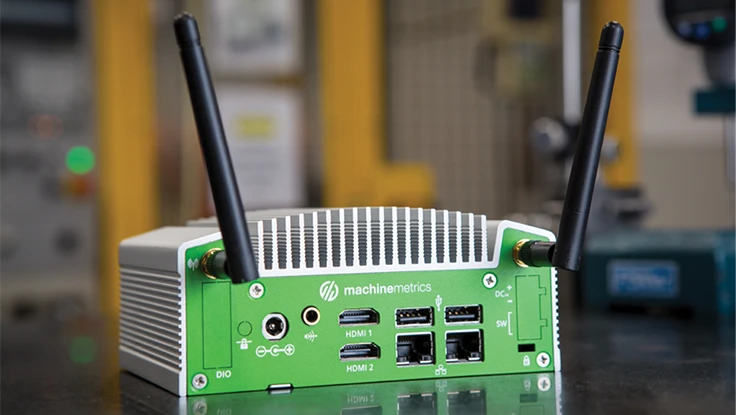
Connecting machinery to computer and communications can boost productivity by offering insights into operations. Eric Fogg, co-founder and COO at software provider MachineMetrics identified these critical benefits in an interview with Today’s Medical Developments.
1. What are the risks when a company connects machine tools for monitoring?
Fogg: Connecting equipment for monitoring can present a security risk when not done correctly, however doing so securely does not have to be expensive. MachineMetrics has worked and consulted with information technology (IT) security experts to make sure our system is safe.
2. What are the benefits when connecting machine tools for monitoring; how does that outweigh the risks?
Fogg: Those that connect to machine monitoring are increasing production by making better decisions driven by data, enabling better, real-time communication between management and the shop floor.
3. What are some hesitations heard when considering implementation of a machine monitoring system?
Fogg: Security is usually the top concern. After that, customers worry if they are ready to handle all the data and if they have the time and staff to act on it.
4. What steps should a machine shop take in order to protect equipment it plans to monitor?
Fogg: Since we pull data directly from machine controls, and our system is cloud based, all computers in the plant are separate from the monitoring system. Though it’s good practice to keep up with updates, password protection, etc., it has no impact on the security of MachineMetrics. All a shop has to do is run network cables to each machine (wireless is available as well) and MachineMetrics takes it from there.
5. How do machine monitoring, dashboards and data transparency save money, increase competitiveness, and improve employee morale?
Fogg: The transparency of the system allows companies to acutely understand problems, bringing problems to the surface much quicker than before.
MachineMetrics increases machine utilization by 15% to 25% in most shops by allowing customers to understand how well their investments are working for them and where they should be investing further.
Employees can be approached about problems within minutes or hours of an event, not the end of the day or week when the problem is inflated. This turns the conversation between management and employees from frustrated or angry when a job is late to more helpful when the problem has just occurred and can be worked through for improvements.
With setup times varying by operator and shift, job changeovers are the biggest source of lost production time for a business. Using monitoring systems enables a business to track setup time by incorporating it into the workflow when dispatching jobs.
The software’s Operator View allows operators to start and stop jobs, categorize downtime, and reject parts for quality assurance. Operators also gain confidence that supervisors are going to address problems proactively and involve them in the process, and supervisors gain confidence that their employees are engaged.

6. What have machine tool companies responses been when job shop owners realize they don’t need to invest in more equipment once they have data and have learned how to improve production with current machines?
Fogg: Machine tool companies like machine monitoring software because they know that their customers’ success and profit is good for them in the long haul when equipment performs up to stated specifications or better.
7. What is the minimum improvement a shop can expect to see once implemented?
Fogg: We usually see a minimum of 10% increase in productivity as well as more confidence in quoting and capital expenditure decisions. Information such as cycle times, performance, number of parts produced, rejects, downtime reasons, and reject reasons can be collected for each part operation. This information allows managers to quickly identify issues related to specific operations and measure the effectiveness of process improvements.

8. How is MachineMetrics set apart from market competitors?
Fogg: We are focused on building simple software that focuses on providing a human context to data, something no one else is currently doing. In addition, by being cloud based, our software is dynamic with new features and updates weekly.
About the author: Elizabeth Engler Modic is editor of Today’s Medical Developments and can be reached at emodic@gie.net.
Latest from Today's Medical Developments
- High precision, productivity in combined punching and shearing systems
- GROB G550T 5-axis mill-turn universal machining center
- Betacom, Siemens launch 5G network platform to accelerate manufacturing innovation
- Starrett’s AVR400 CNC vision system
- US cutting tools orders decreased 2% from November 2024
- SMW Autoblok's Manual Jack connection kit
- MedTech Innovator welcomes five new industry partners
- First Article Inspection for quality control