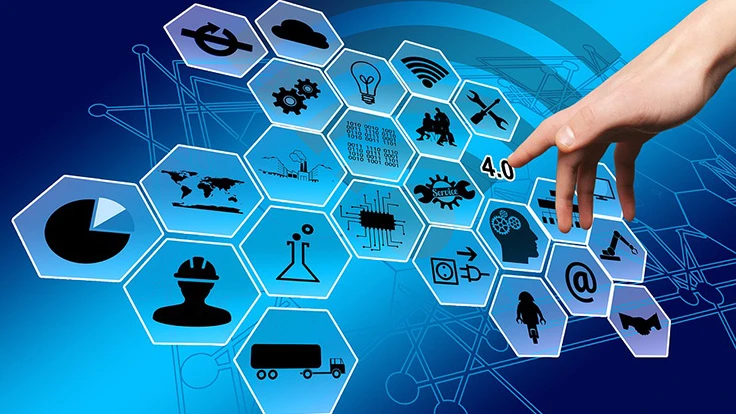
By Cory Vanderpool, Business Development Director, Magnum Energy
The Internet of Things (IoT) is no longer just a buzzword or emerging trend but is helping progress technology, resulting in innovative solutions to solve challenges; today it readily incorporates new sensors and other embedded platforms.
Data collection has changed. It used to require guidance from individual users whereas now sensors are programmed to record data without requiring any expertise and minimal interaction. Through the rise of automation and IoT, the number of connected devices has been growing along with the amount of data derived.
Sensors and the IoT
Data collected through sensors helps users measure and monitor valuable information. During product development, connected sensors on product componentry that can gather and deliver real-time information about the performance of the product or the individual components and materials is almost always considered and is being adopted tenfold. In fact, IHS forecasts that the IoT market will grow to an installed base of 30.7 billion devices in 2020 and increase to 75.4 billion in 2025.
And, more recently, Markets and Markets analysts reported that the IoT technology market is expected to be valued at $639.74 billion by 2022, growing at a CAGR of 25.1% from 2017 to 2022.
IoT and IIoT (Industrial Internet of Things, Industry 4.0) forecasts reflect a growing focus on driving results using sensor-based data and creating analytically rich data sets. IoT sensors and devices are expected to exceed mobile phones as the largest category of connected devices in 2018. From sensitive medical equipment to aircrafts and automotive engines, placing sensors on parts as they go through their design and development evolution delivers critical data related to performance, safety, durability, and more.
Remote condition monitoring
Based on the information received and analyzed, manufacturers can help customers and clients avoid breakdowns and performance problems. These companies could then use the data collected for their design-in engineering processes by revising the design of products and components to achieve more durable and higher performing technology. Furthermore, no longer would teams of people have to travel to visit production sites to record their findings manually. Data from the IoT could draw immediate attention, followed by corrective action, such as repair, maintenance, or replacement.
Manufacturers of really any type of equipment can leverage the IoT in nearly all stages of the manufacturing process. Data on how resources are used within the facility can help to optimize manufacturing production schedules and allow companies to better capitalize on opportunities for savings or plant improvements. Using sensors to collect data can also help companies to benchmark their equipment once it leaves their facility. They can log and compare data from equipment in different locations or where equipment is placed in different operating environments and see how they perform comparatively. This process could unearth hidden operational inefficiencies that would otherwise go undetected until a fatal failure occurs. Lastly, manufacturers could use and analyze the data they receive to offer more appropriate preventative maintenance and warranty programs. Instead of only getting calls when things go wrong, sensor data could help manufacturers to get alerts for service when something is needed, based on the performance of the equipment going out of the prescribed parameters for optimal performance.
This aspect of IoT and manufacturing is often referred to as remote condition monitoring (RCM). RCM is one of a number of basic services that can have a fundamentally positive impact on customer service quality. The ability to access product status information in real time is invaluable for support services, especially because it makes for much more efficient root cause analysis and solution development. The obvious next step becomes predictive maintenance where the use of sensors for things like thermal imaging, vibration analysis, sonic and ultrasonic analysis, and emissions allow for the detection of problems before they even occur.
Security, privacy issues
Although the promise of IoT is strong, there are still challenges that exist. One of the primary concerns is related to security and privacy. When left unsecure, connected devices that are more continuously transmitting can open doors to attacks, endangering not only the consumer but also the companies utilizing the IoT on their assembly lines.
Another topic of discussion, which is prevalent across many sensor technologies, is standardization. Original equipment manufacturers (OEMs) looking to deploy innovative, IoT solutions need to navigate an ever-growing list of connected technology to determine which solutions are compliant and which are best for integration into their ecosystem. This is no easy feat. One of the other concerns, which is a bit more nebulous, is determine how to effectively use the data provided. Collecting copious amounts of data is not challenging, the magic lies in what that data means to not only the user, but even more importantly, to the manufacturer.
Conclusion: Sensors in the IoT are affective
We can see there are tremendous possibilities for manufacturers to take advantage of sensors to extract information from the field. And with the growth of the IoT – now and in the long-term – it’s ever more vital for these interconnected devices and equipment to share performance data. While there are a few albeit addressable concerns, by taking a smart approach, manufacturers can successfully track performance – leading to better product performance. And in the long run, this benefits everyone.
Latest from Today's Medical Developments
- Coating could make medical devices safer for patients
- How robots and cobots can work for you
- Renishaw receives Industry Partner Award
- norelem's modular clamping systems for metrology
- IMTS 2024 Booth Tour: INDEX Corporation
- Robot watched surgery videos then performed with skill of human doctor
- Master Bond’s EP21LSCL-2Med two component non-cytotoxic epoxy
- IMTS 2024 Booth Tour: Tornos Technologies