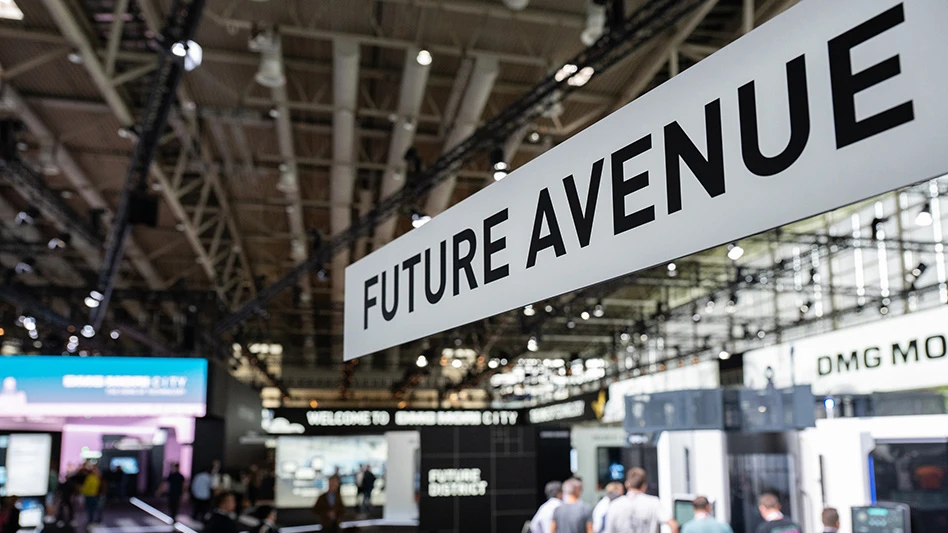
CREDIT: EMO Hannover 2023 | Rainer Jensen | VDW
EMO Hannover 2023 was held under the banner of Innovate Manufacturing. The key topics at this year’s leading trade fair for production technology were automated production, sustainability, and the networking of machines with other production systems. Visitors were once again treated to a large number of major developments that are set to shape and change the face of metalworking in the coming years.
The shortage of skilled workers is now impacting the metal industry, too. Manufacturers are increasingly responding by adding appropriate automation solutions to their machine tools. More and more digital aspects are also finding their way into production facilities. The capture of production data represents the basis for documenting and monitoring production processes. This applies not only to the quality of the manufactured products, but also to their ecological footprint. Many exhibitors addressed the topic of sustainability at the event. Establishing and maintaining contacts and incorporating fresh ideas from start-ups are also of fundamental importance for the future orientation of the industry. And noticeably more importance is now attached to the initial training of junior employees and the further training of existing staff. The highlights from various topic areas at this year's EMO Hannover are presented below. They illustrate not only the innovative potential of the companies, but also the diversity of the relevant topics.
Networked machine tools and components – key requisites for automation
The largest exhibitor at EMO Hannover 2023 was DMG MORI from Bielefeld, Germany. The German-Japanese manufacturer presented its innovations in its own exhibition hall: DMG MORI City. DMG Mori's product portfolio includes systems of all sizes. The 39 machines on display included several world premieres. DMG MORI presented its INH 63, a machine tool for the 5-axis machining of parts weighing up to 1,000kg. The coolant and lubricant system is designed for particularly resource-saving and sustainable operation. The machine has been specially designed to be integrated into automated production systems. The same applies to one of the company's new automation solutions: the flexibly expandable PH Cell 800 pallet system, which is specially designed for connection to DMG MORI machine tools. It can automatically insert workpieces into the machine, and then remove them subsequently.
The trend towards highly flexible, unmanned production is also reflected in the UH-AMR 2000 autonomous robot system, which was also on show. The platforms move autonomously and can transport blanks, finished workpieces, chip containers and tools as required. A robot is also mounted on the platform; it can load workpieces and tools directly into the machine. In terms of digitalization, DMG MORI presented its new CelosX system, which facilitates the process-oriented management of production data. Thanks to the integration of the Xchange cloud solution, it is also able to evaluate this data across different machines.
Nürtingen-based company Heller presented its new F6000 machine, the first machining center in the 5-axis F series. The new machine includes various innovative features. The rotary table which holds the workpiece forms the central component of the machine. The high-torque motor also allows it to be used for turning operations. Heller is thus following the trend towards complete machining in a single machine, doing away with the need for reclamping.
Rounding off the overall development program, an extra-wide chip conveyor prevents downtimes due to chip jams, even in autonomous operation. The machine is controlled by a Siemens One machine control system featuring a large 24" screen.
The Heller Service Interface Global (HSI-Global) system detects the wear of spindles and axes using special test cycles, avoiding any need for time-consuming intervention by technicians. This allows time and cost-intensive maintenance to be planned and downtimes to be reduced to a minimum.
INDEX, based in Esslingen, Germany, exhibited its G300/G320, a freely configurable modular machine tool system. The options include main and counter spindles, milling spindles, as well as multiple tool turrets and freely selectable steady rests. The integrated tool magazine can be expanded by connecting an external unit; this allows long operating times to be achieved without the need to reload tools.
Like almost all machine tool manufacturers, INDEX, too, has added a comprehensive automation system to supplement its machine tools. The iXcenter robot cell is compatible with the G300/G320 and includes not only a robot for loading and unloading workpieces, but also cells for automatic inspection, cleaning, deburring, laser marking and storage.
WFL from Linz, Austria, exhibited its M80X Millturn machine tool under the banner of Clamp Once – Machine Complete. It can machine large components up to a diameter of 1,000mm and is a prime example of the WFL Millturn series. The Millturn machining centers can perform conventional machining processes such as turning and milling (machining with geometrically defined cutting edges, in accordance with DIN 8589-0) in a single machine. However, the machine also incorporates a grinding unit, including a grinding wheel dressing unit. A total of more than 20 technology cycles can be carried out in one machine, including deep drilling and the production of internal gears. It also features quality checking based on a measuring probe in the machine itself, rounding off WFL’s concept of complete machining without reclamping in a single machine.
Another manufacturer which presented its latest automation solutions on its stand was Grob-Werke, from Mindelheim, Germany. It exhibited the G550T 5-axis milling/turning machining center, with the PSS-R900 rotary pallet storage system connected to it. This helps users to implement unmanned operation. Grob-Werke also premiered a driverless transport system (AGV - Automated Guided Vehicle) which can supply various machine tools by transporting both workpieces and tools. The floor-driving vehicle can be used in a human environment and be deployed as part of a fleet system.
Australian grinding machine manufacturer ANCA made the journey to EMO Hannover 2023 to present several world premieres. Its most important innovation was in the field of ultra-precise tool production. ANCA ’s FX Ultra series is specifically designed for grinding extremely small tools with diameters from 0.1 mm. To achieve this, a special control system was implemented with axis resolution down to the nano range. Further accuracy enhancement measures include temperature compensation of the machine and concentricity compensation of the spindle. These allow accuracy levels down to 0.002 mm to be achieved. Another world premiere from ANCA was a system for the industrial rounding of milling cutter edges. Precisely rounded cutting edges help extend the service life of milling tools. The EPX-SF cutting edge rounding system allows milling tools to be prepared in series production. These developments are complemented by a comprehensive automation system that facilitates completely unattended production processes, even over longer periods of time.
Keba, a manufacturer of automation solutions, from Lahnau in Germany, presented a range of innovations. Of particular interest to visitors was the Force Feedback Touch, a control panel for production systems that captures haptic forces and can give user-defined haptic feedback. This allows the operator to concentrate on the machine area and not divide his attention between the operator panel and the machining task, as is usually the case. This solution combines multi-touch panels with conventional buttons, thus enhancing its user-friendliness and improving safety. Keba also presented a new approach to spindle bearings that permits spindle movements in five axes: the LeviSpin drilling spindle with magnetic bearings. These movements include oscillation for optimized chip breaking as well as compensation movements for deviations. The spindle also records process forces at maximum resolution, which can then be used to identify process irregularities and tool wear. Overall, this innovative approach can increase the metal removal rate, reduce tool wear, and improve machining quality.
Japanese company THK, a well-established expert and pioneer in linear technology used in machine tools and the packaging industry, presented its superior linear motion guide at EMO Hannover 2023. There is constant demand for process times to be shortened, in turn requiring higher speeds from the production components. The FHS super high-speed LM guide with its maximum speed of 15m/s was specially developed for this purpose and is also designed for high speeds over longer periods of use.
Sustainability and technical innovation in tools and clamping technology
CERATIZIT from Austria presented pioneering products in the field of sustainability at this year's EMO Hannover. At the start of the trade fair, CERATIZIT announced that it would be reporting the product carbon footprint of all its products with immediate effect; this would allow its customers to take preemptive action aimed at meeting all regulatory requirements concerning the monitoring of individual emissions. These include the CO2 footprints of all raw materials, as well as of the production processes used in manufacturing the tools. Tool innovations were also on show. The Maximill milling head features integrated flank cooling and indexable inserts; the milling head consists of an additively manufactured base body with internal coolant channels. This ensures even wetting of the free cutting edge surfaces and thus helps extend tool life while facilitating increased cutting parameters.
Oerlikon Balzers, the coating expert company from Liechtenstein, presented its new Balinit Mayura ta-C coating for processing non-ferrous materials such as aluminum, polymers and copper at the Hanover event. It is characterized by its high hardness and smoothness levels, yet it is thinner than other comparable coating systems on the market. This allows sharper cutting edges to be achieved. Exemplary studies have shown that the coating’s properties can reduce wear in the drilling of aluminum by 20%.
The transition to electric vehicles requires the adaptation of tools and tool concepts. Above all, the switch from combustion engines to sustainable drive systems will reduce the number of components. At the same time, it will bring about changes in the type and form of the components and the associated requirements. Some battery trays and gearbox housings require larger workpieces to be machined, for example. At the same time, thin-walled aluminum housings are increasingly being used.
Mapal from Aalen, Germany, positioned itself at EMO as a complete supplier of tools for the machining of electric vehicle components. Its stand featured an illustrative example of the motor axle of an electric car, showing the relevant tools required for its manufacture. The tool manufacturer also presented its Mega-Deep-Drill-Steel drilling tool for the efficient deep drilling of steel and cast materials with lengths up to 40x their diameter. What makes the drill exceptional is its crowned cutting edge and four guide chamfers. As a technical innovation, the diameters of the drill’s cooling channels are 20% larger, which reduces tool wear and improves chip evacuation.
At the start of EMO Hannover 2023, the Japanese specialist in threading tools, OSG, presented a special tool innovation. The GreenTap thread former has a unique tool design that was developed using CAE methods. The new shape maximizes tool stability, fracture strength and cutting edge stability. It generates lower torque levels and axial forces during machining which, in combination with an enhanced cooling effect and reduced friction, can significantly extend tool life. In addition, the thread forming taps in the GreenTap series are manufactured using a new production process that halves energy consumption during production. This enhances the tool’s sustainability credentials both during manufacture and then later in use.
As one of the largest manufacturers of cutting tools, Iscar from Israel presented various innovations in precision tools. At the 2023 event, the focus was on the Heli3Mill shoulder milling cutter and the Micro3Feed fast-feed milling cutter, which are designed as indexable insert milling cutters. The milling cutters are available from diameters of 6mm and 8mm respectively. Previous indexable inserts could only be used for milling tools with a larger diameter. This improves cost and resource efficiency compared to solid carbide tools. In addition, there is no need for regrinding and the time-consuming logistics this involves.
Schunk from Lauffen a.N., Germany, exhibited various automation solutions for clamping and gripping technology at EMO. Examples included zero-point clamping systems with electrical status detection, and electrically driven power clamping blocks with jaw position detection. Schunk also presented a hydraulic expansion chuck with real-time sensor technology. These products are digitally networked and can be incorporated into an automated production system that integrates process and quality monitoring. Mechanical enhancements were also on show, such as the first coolant-proof polygon clamping device. This tool extension makes it possible to reach challenging, low-lying areas on the component with existing tools.
Haimer from Igenhausen, Germany, exhibited a world first in the field of clamping devices in the shape of its new Hybrid Chuck system. It combines hydraulic expansion chucks and shrink fit chucks, thus yielding the advantages of both systems. The patented product offers the high clamping force and precision of a shrink chuck combined with the vibration-damping properties of a hydraulic expansion chuck. Haimer also presented various automation solutions. Among these, the Automation Cube One automatic shrinking cell attracted particular attention. The robot cell is used for shrinking and unshrinking as well as for measuring tools; it also adds a cooling system. Tools with varying holders and diameters undergo the process with no need for human interaction. The tool data can then be transferred to the machine tool and fed into the tool management system.
At this year's EMO, workholding device manufacturer Römheld from Laubach in Germany demonstrated how clamping technology, too, is now going digital. Many of the clamping devices on show – such as lever clamps, swing clamps and bore clamps – not only hold workpieces securely in place but can also use sensors to detect the exact clamping status and output this via display elements or interfaces such as IO-Link. This allows errors in the production process to be detected and rectified before production downtimes occur. Römheld has introduced a small version of an electric swing clamp which can take care of clamping tasks in confined spaces. Apart from a 24V power supply, the electric drive requires no other units. It can apply a clamping force of up to 2.7kN to the workpiece despite its compact size. Römheld also showed that it is possible to optimize classic clamping devices such as the machine vise. The UC125 machine vise applies the clamping force to the clamping jaws from above and thus achieves a high degree of dimensional accuracy that cannot be guaranteed with conventional machine vises.
AMF Maier from Fellbach in Germany also demonstrated how the range of tasks performed by clamping devices today goes far beyond the simple securing of workpieces. The manufacturer's robot-based automation solution combines the automatic clamping of workpieces with storage. AMF has created a complete solution in a small space by ensuring optimum coordination of the overall system. In addition to automated clamping, the fixing of workpieces with complex geometries was a further highlight on the AMF Maier stand this year. The arrival of 3D printing and workpiece topologies optimized by artificial intelligence (AI) means that workpieces now have to be secured that are impossible to grip firmly using conventional clamping devices. AMF Maier’s modular clamping system consists of over 100 different elements that can be used to create customized clamping configurations for any workpiece geometry.
Intelligent, high-precision measuring and testing technology
The increased demands in terms of product quality and sustainability require a full range of measuring and testing technology at the various stages of production. This trend was also evident among the exhibitors at EMO Hannover 2023, who presented methods which are faster and offer ever greater precision and automation for performing a wide range of measuring and analysis tasks.
ZEISS from Oberkochen in Germany has developed the Scanbox Series 5, which is an automation solution featuring a 3D scanner. Several components can be measured simultaneously in the Scanbox; the measurement sequences are executed automatically and are adapted to the specific elements being measured. The customer can train the system using a SmartTeach function. The high degree of quality assurance automation helps save costs and time and ensures high quality standards. In addition, ZEISS presented the ZEISS Prismo, a new generation of coordinate measuring machines that can take measurements more quickly while consuming significantly less power. New scanning parameters were developed for this purpose, with ZEISS integrating an intelligent control unit and a PowerSaver for greater energy efficiency.
Taking an holistic approach, Pro-Micron, based in Kaufbeuren in Germany, tackled various problems in the areas of turning, milling, drilling, reaming and grinding. The company has developed a system that uses a tool holder (spike_mobile) or a spindle attachment (spike_inspindle) to record the process forces and evaluate the data. The resulting forces and torques of the processes can be recorded separately in detail and assigned to each individual cutting edge on the tool. This allows tool wear to be detected at an early stage, providing information about the resulting workpiece quality. Data processing and evaluation help predict quality during production and can also be used to create a digital twin. Identifying tool failure at an early stage allows rejects to be avoided and process optimizations to be implemented based on real data.
Previously, gear wheels were subjected to sample statistical checks using a tactile sensor. At EMO Hannover, the US-based Gleason Corporation presented an automated inspection system for the complete measurement of gears using laser scanning to analyze waviness in profile and lead. This means that each gear can be individually checked to see whether it is within the tolerance band. Such requirements are becoming more common due to the switch to electric vehicles. Engine noise is now minimal, bringing the remaining acoustic signals into the foreground which can then be perceived as obtrusive. Complete gear inspections are required. Subsequent evaluation of the point cloud provides information about potential dimensional deviations. The latter can lead to unwanted noise during vehicle operation.
In order to ensure maximum precision in tool manufacture, the Swiss company Walter, part of the United Grinding Group, has developed the world's most accurate optical measuring system – Helicheck nano – for measuring milling tools. The repeatability of less than one micrometer is unprecedented. The entire measuring process is fully automatic, allowing even non-specialists to operate the Helicheck Nano with its simple graphic interface. It can be used in conjunction with an automation cell, enabling the automated measurement of entire tool pallets.
Connectivity, digitalization, and automation
The IIP Ecosphere project presented the results of three and a half years’ work on its stand in the Future of Connectivity Area. The aim of the BMWK-funded lighthouse project was to facilitate the use of artificial intelligence in production. The VDW (German Machine Tool Builders' Association) project partner provided support, particularly in the area of standardization, and with umati, ensuring that the requirements of the machine tool industry were addressed in the project. A key result of the project is an open IIoT platform. The platform is based on open standards, can be used independently of manufacturers and is conceived to supplement existing resources and systems. Currently available IIoT solutions can be integrated into the platform, which natively supports the use of AI. Companies have a high degree of control over the system, as it is highly configurable. A platform demonstrator on the trade fair stand provided an example of visual quality control based on cobots, component identification and condition monitoring. Everything was fully integrated into the IIoT platform. The key innovation here was the platform's ability not only to distribute the models automatically to different edge devices and industrial PCs, but also to update them flexibly as required. It is planned to continue operating the platform in the future under the name Oktoflow. Another development of the Ecosphere project is an assistance system that supports machine operators in the parameterization and monitoring of machining processes, covering not only classic turning and milling, but also complex processes such as gear skiving for gear production. Another highlight was the IIP-Ecosphere closing symposium, which was also held during EMO Hannover. A key topic here was the improvement of data availability in the production environment. Various promising approaches were presented, including the concept of federated learning and the generation of synthetic image data.
Spanflug, a company based in Munich in Germany, showcased its “Spanflug make” software solution, which simplifies the process of creating and sending quotes for companies. It is basically a system for the management of offers and orders. The software can also automatically evaluate uploaded CAD files, and thus provide an immediate estimation of the production complexity and costs. This significantly reduces the time and effort involved in preparing quotations. The “Spanflug buy” platform uses this technology to offer not only in-house solutions, but also a procurement platform where customers can upload their design files and receive a binding offer. Spanflug then takes care of placing the order with one of the more than 5,000 affiliated contract manufacturers in Germany and Austria, thus guaranteeing that quality standards and delivery dates are met.
Umati, the cross-manufacturer initiative for standardized machine data communication, made its first major appearance at EMO Hannover 2019. It is now in widespread use. On the technical basis of OPC UA, umati connects not only machine tools but also systems from all areas of production technology. The OPC UA companion specifications for different types of devices are organized by VDW and VDMA.
In the future, cooperation with the US-based MT-Connect initiative will further expand the functionality and compatibility of umati. Using umati, the direct communication of machine data via OPC UA to the Asset Administration Shell (AAS) was demonstrated together with the Industrial Digital Twin Association (IDTA) and the Institute for Control Technology of Machine Tools and Manufacturing Systems (ISW) at the University of Stuttgart. VDW, VDMA and Deutsche Telekom were also able to demonstrate the versatility of umati with other partners. Here, a federated data room for the exchange of data used for monitoring the service life of cutting tools was implemented as a prototype reference for the German government's Manufacturing-X initiative.
Fanuc, the Japanese supplier of control systems, robots, and machines, had its own stand at the event, but was also involved in many other stands. Attracting great interest were the CRX series cobots (collaborative robots), with their maximum load capacity of 30 kg. These are ideal automation solutions, for example in conjunction with machine tools and systems for loading and unloading, palletizing and quality control. They are easy to control and require no programming knowledge, making them attractive propositions for first-time users of robots. Cobots therefore represent an effective way of combating the shortage of skilled workers and can be used in human environments. Sensors in each axis detect imminent collisions with people or objects and stop any further movement. The torque-guided movements also allow the cobots to compensate for tolerances in the workpiece and the environment and to take over coordinative tasks from humans. The robots can also be upgraded with a vision sensor system, further increasing the range of applications. In summary, cobots represent a major new trend in production technology. They can help significantly increase the degree of automation in various processing tasks.
With its new UH spindle series, GMN from Nuremberg, Germany, is pursuing greater energy efficiency and placing a firm focus on digitalization. For the first time, the drive is powered by a synchronous motor, offering superior performance and low operating temperatures. The high-power density and the compact design allow it to be accommodated in a small installation space; maximum speeds can also be achieved with increased dynamic rigidity and smooth running. Further important aspects include data acquisition and the digital IO-Link interface. Integrated data acquisition and evaluation can be achieved using the Idea-4S embedded system. This is an electronic system that can be integrated into spindles and connected bidirectionally to all machine controllers via IO-Link. Sensors are also used in the spindles to record temperature, speed, tool clamping, vibrations, and axial displacement. These spindle process values can then be transmitted to the machine control and production networks.
Technical solutions for enhanced sustainability in production
Sustainability is gaining in importance not only in industry in general, but also in the machine tool industry as a result. One of the Future Insights therefore focused on Sustainability in Production. Rising energy costs are an important factor here, but so, too, is the fact that more and more manufacturing companies are keen to show their customers how many resources they are using in production. The operation of machine tools and production systems can be made sustainable using various methods. Principal measures already offered by most manufacturers include the measurement of energy consumption, which then provides a pool of information which can be used for energy-saving machine operation. Switching off individual units when they are not needed also helps to significantly reduce standby power consumption. Optimized filtering of cooling lubricant, which allows it to be used for longer and therefore disposed of less frequently, is also increasingly being used.
In the dedicated Sustainability Area, the EMO Hannover exhibitors showcased the latest developments for increasing sustainability. The enclosure manufacturer Rittal demonstrated how a digital twin can be used to optimize the design of enclosures not only in terms of their functionality, but also regarding their energy consumption. The LiquidMate system of em machines GmbH from Rahden analyzes the consumption of cooling lubricant.
Sensors permit the continuous monitoring of ingredient and impurity concentrations during operation, with the system only making changes if necessary.
The exhibition also featured a presentation of current research at the Karlsruhe Institute of Technology (KIT). This included a demonstration of the automatic disassembly of electric motors. Such technology not only makes it possible to recycle the different materials, but also allows intact components to be reused. Improved recycling concepts form the basis of an eco-friendly circular economy.
Startups and training – two key aspects for maintaining and raising competitiveness
The special show for training was organized by the Youth Education and Development Foundation for Mechanical Engineering. The companies and educational institutions participating in the show launched the initiative to show young people the kinds of training opportunities that are available in mechanical engineering, and thus actively counteract the shortage of skilled workers. Students and trainees were able to talk to company representatives in a separate area. The participants were given an insight into the typical elements in a process chain by being given the task of building a Formula 1 model car. The required parts had to be collected from the stands of the various companies, where they also had the opportunity to find out more about the design and production stages of the individual components. The show was also complemented by a stage program. The entire special show for training received no support in the form of subsidies and was financed by the participating companies themselves.
The Startup Area organized by VDW and VDMA offered young (especially smaller) companies the opportunity to present their products and services at EMO Hannover. The ideas emerging from such young companies are in great demand from established providers. The innovative approaches of the start-ups mostly centered around digital aspects of production technology. The spectrum of the software solutions presented ranged from simulation tools for process optimization through to platform solutions aimed at simplifying planning and sales.
Tetralytix GmbH from Hanover in Germany showcased various solutions for digital process and tool development. These included the Toolyzer simulation solution, which can be used for the rapid development and optimization of cutting tools and cutting processes. Tetralytix presented various examples of applications such as the full analysis of multi-axis gear skiving processes and the evaluation of manufactured workpiece geometry. Collision-free tool movement angles were calculated for ramping and drill milling operations. The company also showed how to include machine-specific properties such as speed and acceleration limits of the axes in the simulation.
FoxBase GmbH from Düsseldorf, Germany, has developed a software platform that enables companies to digitalize their knowledge-based sales processes with the help of artificial intelligence and render them scalable. The tool allows customers and sales staff to identify suitable products, systems, and services. The software identifies individual customer needs via an interactive user interface and calculates specific product recommendations. The system thus does away with the need for time-consuming consultations at the customer’s premises. This speeds up the processes and reduces the pressure on the sales department.
The young company Vibrocut, a spin-off of the Fraunhofer Institute for Machine Tools and Forming Technology, Chemnitz, Germany, showed how its Vibrodrill ultrasonic tool holder can be used to make drilling tools vibrate at high frequency. They have a frequency of approx. 20 kHz and an amplitude of 10µm to 20µm. The positive effects include reduced friction, longer tool life and increased cutting parameter potential. The start-up has also developed the Vibroturn tool holder, a system for turning processes that operates in the low-frequency range at frequencies of 100Hz and amplitudes of up to 0.5mm. The drive is taken from the turret of the lathe used. Chip breaking during turning often represents a problem which can be significantly improved by the use of tool oscillation, thereby increasing process reliability. The young company has already sold its first products and now intends to market its innovative technologies more widely.
Conclusion
EMO Hannover 2023 provided an impressive demonstration of how suppliers of production technology are responding to the current economic, technical, and social challenges. Alongside automation and digitalization, sustainability is increasingly coming to the fore. The companies are responding to the demand for greater cost and resource efficiency and are countering the shortage of skilled workers. In addition, they are prioritizing the gradual refinement and optimization of existing systems and concepts.
Authors
Heiko Blech, M.Sc. Institute of Production Engineering and Machine Tools (IFW), Leibniz Universität Hannover,
Tel. 49 511 762 19848, e-Mail blech@ifw.uni-hannover.de
Timo Rinschede, M.Sc., Institute of Machining Technology, Technische Universität Dortmund, Tel. +49 231 755 90171, e-mail timo.rinschede@tu-dortmund.de
Latest from Today's Medical Developments
- Humanoid robots to become the next US-China battleground
- Air Turbine Technology’s Air Turbine Spindles 601 Series
- Copper nanoparticles could reduce infection risk of implanted medical device
- Renishaw's TEMPUS technology, RenAM 500 metal AM system
- #52 - Manufacturing Matters - Fall 2024 Aerospace Industry Outlook with Richard Aboulafia
- Tariffs threaten small business growth, increase costs across industries
- Feed your brain on your lunch break at our upcoming Lunch + Learn!
- Robotics action plan for Europe