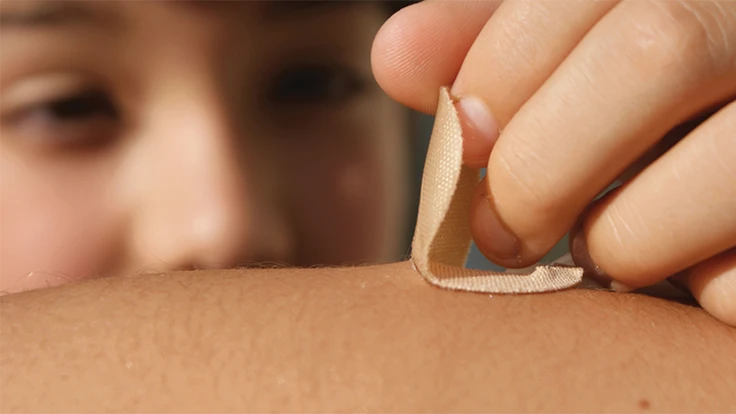
Demand is booming for wearable medical devices used in diagnosis, monitoring, and drug delivery, with the global market projected to reach $612 billion by 2024, according to a 2016 report by market research firm Grand View Research – (see medical infographic, pg. 8).
To achieve success, wearable device designers and manufacturers must deal with a daunting range of clinical and business issues. Two of these – promoting efficacy and gaining a competitive advantage – illustrate how silicone adhesives and elastomers contribute important benefits.
Comfort, ease

The efficacy of a wearable diagnostic or therapeutic device depends directly on patient compliance, which relies on comfort during wear and removal. Many designers are turning to silicone pressure-sensitive adhesives (PSAs) with stronger adhesion and soft skin adhesives (SSAs) featuring lower peel adhesion for delicate or fragile skin.
Silicone PSAs and SSAs deliver a more comfortable patient experience than competitive adhesive technologies, such as acrylics that can cause skin sensitization and polyurethanes that have very low breathability.
Another aspect of efficacy is ease of use, which promotes better results. For example, testing for sleep apnea typically requires an overnight session in a hospital or clinic because the complicated polysomnogram equipment must be operated by a professional technician. Home testing for sleep apnea, while it cannot diagnose as broad a range of disorders, has the advantage of enabling the patient to self-test under normal sleep conditions, which may deliver more-accurate results. Home tests, which combine a belt around the chest to measure respiratory effort, and a blood oxygen sensor and breath sensor attached to the nose with adhesive, are less cumbersome and allow patients to sleep in their preferred position.
In a related example, the ability to use a skin-adhered device when taking part in everyday activities, including sports and recreation, also supports efficacy. Several times more breathable than other organic polymers, the material also conforms well to body contours for improved fit and can be formulated with higher strength to accommodate body movements during vigorous sports activities.

Competitive differentiation
Another factor in the success of a medical device is standing out from competitors. Differentiation may hinge on a superior design, higher performance, or a lower price. Material technology plays a big role in designing wearable medical devices that are well received in the marketplace.
Higher performance: Medical-grade silicones are biocompatible and have been used in medical device applications for 70 years. They are non-cytotoxic, non-irritating, and non-sensitizing to skin. Their mechanism of action combines low interfacial bonding for reduced impact on the skin with high flowability for stable adhesion via a mechanical interlock with skin pores. Silicones also spread easily to form films over the skin.
Silicone adhesives offer significant performance advantages compared to competitive adhesives. For example, although acrylic adhesives provide a strong, secure bond with the skin, they cannot be repositioned, and removal can cause pain and skin trauma in elderly or neonatal patients. Acrylic adhesives are also known to cause skin sensitization. Polyurethanes, which deliver medium adhesion, are more hydrophilic than silicones. Their moisture absorption can reduce adhesion to skin. These adhesives have very low breathability compared to silicones, and can leave a residue when removed.
Greater design freedom: With silicone technology, key properties such as adhesion level, conformity to the skin, peel strength, and permeability, transparency, and even processing parameters can be tailored to meet a medical device’s requirements.
Overmolding of silicone elastomers inclusive of adhesion components is a proven method for enhancing product design and consolidating parts. Instead of joining two components mechanically, overmolding provides a strong, enduring bond. A growing array of substrates suitable for overmolding with silicone elastomers offers designers new choices.
Silicones in wearables

Identifying the best silicone adhesive or elastomer for a given application requires guidance from the silicone supplier regarding its chemistry (for example, solvent-based vs. solventless adhesive); performance properties such as tack, adhesion level, and dynamic shear; performance under different wear conditions; and, in the case of self-bonding elastomers, suitability for bonding with different plastic substrates.
Silicone suppliers such as Dow offer extensive testing, application development, and regulatory compliance expertise and resources to assist medical device designers and manufacturers with material selection, processing parameters, and other issues.
The continued expansion of wearable technology is tied to a host of variables, including correct and compliant patient use and the ability of manufacturers to create products that can stand out in a highly competitive and fast-moving marketplace. Advanced silicone adhesives and elastomers play a key role by supporting efficacy and helping produce efficient, cost-effective, next-generation designs.
The Dow Chemical Co.
www.dow.com
Latest from Today's Medical Developments
- Tariffs threaten small business growth, increase costs across industries
- Feed your brain on your lunch break at our upcoming Lunch + Learn!
- Robotics action plan for Europe
- Maximize your First Article Inspection efficiency and accuracy
- UPM Additive rebrands to UPM Advanced
- Master Bond’s LED415DC90Med dual-curable adhesive
- Minalex celebrates 60 years of excellence in miniature aluminum extrusions
- Tormach’s Chip Conveyor Kit for the 1500MX CNC Mill