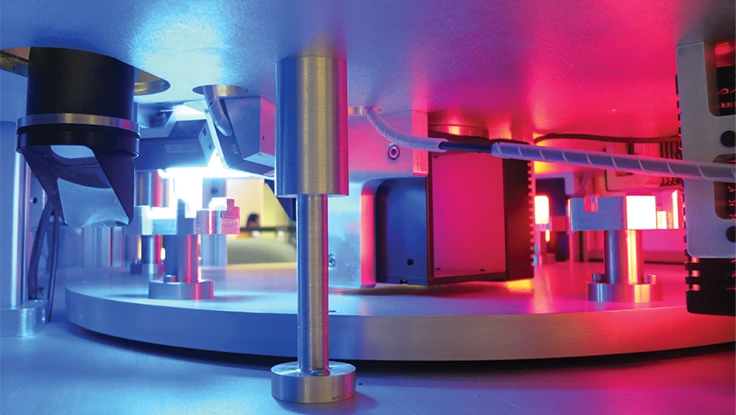
Flex (formerly Flextronics) builds an insulin pump – about 4cm x 3cm x 1cm – that attaches to the patient’s skin. A program running on the patient’s personal digital assistant (PDA) controls the pump and keeps track of when an insulin injection is needed. When the PDA gives the command, a small needle pops out of the device and injects insulin into the patient. The device typically remains attached to the patient for about three days and while attached, the patient can shower or swim. Inside the device is a complex mechanism that safely inserts the needle into the patient’s skin. Six different areas of the pump interior need close-tolerance inspection to ensure safe operation.
When production began, 20 to 25 quality control inspectors with microscopes manually inspected the interior of the insulin pump just before the case was sealed. Inspections include the position of the needle, the track that the needle rides on, and the mechanism that traps the needle. With the inspection criteria primarily subjective, it was possible for one inspector to pass a part that another inspector would reject. The product’s critical nature makes it essential to reject assemblies if there is the slightest possibility they might not perform their function. The result is that only 85% of production initially passed manual inspection
Latest from Today's Medical Developments
- Season's greetings
- Best of 2024: #7 Article – Synchronized machining processes for medtech
- Best of 2024: #7 News – 3D printing could revolutionize treatment for cataracts, other eye conditions
- Best of 2024: #8 Article – Perfecting the CMP process for surgical blades
- Best of 2024: #8 News – Johnson & Johnson to acquire Shockwave Medical
- Best of 2024: #9 Article – Strategy Milling combines old and new for precision dental restorations
- Best of 2024: #9 News – Global robotics race
- Best of 2024: #10 Article – Designing medical devices for every user