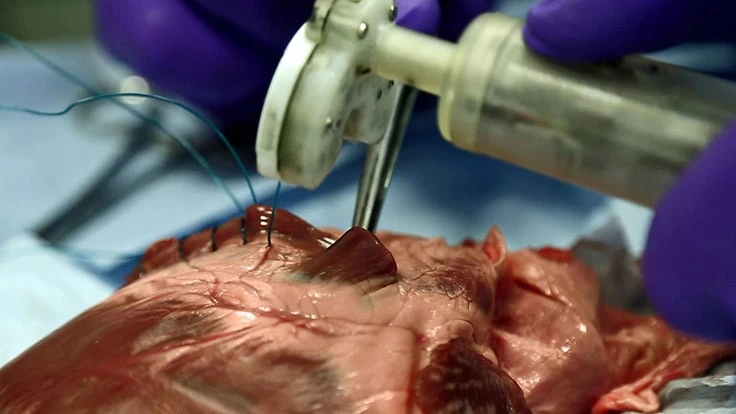
Medical stitching by hand can be problematic as it relies on the ability, dexterity, training, and alertness of the practitioner. Sutrue engineers solved the problem by developing two automated stitching devices, transforming the manual process into a simpler, quicker, and more accurate automated process, reducing the margin for human error. There have been more than 10,000 patent attempts to produce a device that sutures wounds and Sutrue is the first to successfully achieve it.
Developers produced 38 different prototypes and designed and tested more than 1,500 parts, involving 15,000 hours of design work, resulting in the creation of a patented automated suturing mechanism that consistently works across both types of devices – handheld and endoscopic/robotic.
Robotic/endoscopic device
For more than eight years, design engineers worked closely with Richard Trimlett, cardiothoracic surgeon and head of mechanical support at the Royal Brompton Hospital to develop both devices. Trimlett sees the device as being very influential to the future of robotic surgery, believing it could help significantly reduce the number of open operations undertaken in the future as it enables sutures to be carried out endoscopically, removing the need to open up a patient.
“It’s true to say that the majority of operations we’re doing today are still open and that’s not because the patient wants them open, it’s because of the limitations of the technology and so there are many improvements to technology that we need to get to the point where we can do everything as a keyhole operation and I see this [Sutrue device] as one of them,” Trimlett says.
Engineering
The engineering process involved in the creation of the Sutrue devices has been significantly faster than traditional methods due to the use of cutting edge 3D printing technology provided by GE Additive.
“Rapid prototyping has significantly reduced the cost of the creation of the devices, probably by a factor of 50. It has also shaved years off the time it would have otherwise taken. We’ve taken a create, print, test, tweak, reprint approach to solving the problem. We even coined our own term for the working process and called it Multi-typing, which is the ability to loosely design the same component in three or four different ways, have them printed within a few hours and then test and learn from each prototype. This approach has been instrumental in allowing a small start-up company likes ours to maximize our output in terms of creativity and problem solving,” says Alex Berry, MD of Sutrue.
3D printing
Concept Laser – now a part of GE Additive – has been working with Sutrue for almost three years with the printing of the very small and detailed parts that the automated suturing devices require.
“By using the high-resolution capabilities of our Mlab cusing R 3D printer, Sutrue has been able to successfully speed up the engineering process involved in the creation of their medical devices, through a process called rapid prototyping,” says Stephan Zeidler, business development manager for the medical sector at Concept Laser. “Once designed by Sutrue, the structurally superior parts were printed by our team before Sutrue assembled them into numerous medical prototypes – sometimes straight from our printer with minimal post processing. This in turn saved considerable time and cost and has resulted in the completion of a series of fully-functioning medical prototypes. Sutrue’s success in having achieved this is a fantastic example of what is possible with our DMLM machines and additive manufacturing technology. We are delighted that both devices are now mechanically sound and are ready for testing within medical industry.”
Suture quickly, reproducibly, cleanly
This slender suturing device is inserted via a conventional endoscope the size of a drinking straw during the heart operation and moved into position. Its head can rotate and be pivoted in order to find any desired batch of tissue. The needle rotates softly and with pinpoint precision during suturing. This is possible thanks to a complex miniature gear mechanism that drives the needle. The entire gear mechanism is an AM assembly. What this innovation actually means for the operator is that the suture is pulled through quickly and cleanly and the stitch is automatically set in place. A few small stitches in arteries or in delicate structures are now possible. Each stitch can be performed with reproducible accuracy using the suturing device. Complicated operations in particular can be performed faster and more safely. Thanks to the suture device, up to three rotations of a needle per second are now possible, instead of one stich per 25 seconds while doing by hand. This reduces the risk associated with the operation for both, patients and surgeons.
Idea of stabilizing the heart muscle during the operation
In Great Britain alone, around half a million people live with a heart defect. Treatment with drugs only delivers very minor improvements to patients and often an operation on the heart is the only way to save a person’s life. In Great Britain, cardiovascular disease is the second most common cause of death, accounting for 27% of deaths, after cancer, which accounts for 29% of all deaths. During open-heart surgery, the surgeon needs the heart muscle to be stabilized for an intervention to be made.
(Right: Automated suturing device from Sutrue. The head can be rotated and pivoted to place sutures in any position you want.)
Trimlett outlines the task: “We're doing a beating heart operation so the heart is in use by the body but we need to hold the small area that we're working on still. With the chest open we can put a big suction device in but when we're doing keyhole surgery we need very small parts that we can pass in and out. What we don't want to do is disadvantage the patient by offering them an inferior stability of the heart so that the quality of the operation isn't as good when you do it as a keyhole. I said to Alex, 'could you make something that comes apart in pieces, pass through a very small incision that we can use to hold the heart stable? Could we make it to throw it away and even customize it to the different shapes and sizes?’”
For Trimlett it was clear that the heart stabilizer should be small, be capable of being dismantled, and be designed with exposed channels pre-assembly. The role of the stabilizer is to keep the heart muscle still at the precise point where the surgeon wants to make an intervention. Alex Berry took on the task and presented a biocompatible prototype of the heart stabilizer: one part made of plastic (SLS) and one part made of metal (LaserCUSING). The component consists of a rod on which the U-shaped heart stabilizer is inserted, like a stamp. The surgeon presses the stabilizer onto the operating site that he wants to keep still to make an intervention.
Short development time and care for the patient
The heart stabilizer was successfully developed in just three months. Previously, it was not uncommon for such a new development to take up to ten years. The component itself is printed by ES Technology on an Mlab cusing from Concept Laser in the space of three to four hours. It consists of a metallic basic body and several plastic suction points that aspirate by means of a vacuum. Both parts are joined together using a sandwich technique.
“The solution is estimated to have cost only around £15,000 to develop. Comparable conventional developments used to cost upwards of a million pounds,” says Berry to illustrate the relative sums involved.
But from Trimlett’s point of view, it is primarily the patient who benefits from the new instruments using in heart operations. Here he cites an average rehabilitation time for the patient of around six months following a conventional surgical intervention. “Initial experience indicates that patients undergo a demonstrably gentler procedure and can recover after just three to four weeks.”
“AM makes it possible to produce geometries that cannot be achieved using traditional manufacturing methods. In addition, the parts have greater performance capacity or functional precision, or else they are extremely delicate or small. This is often precisely what the surgeon was previously lacking,” explained Alex Berry.
Sutrue relies on machine technology from Concept Laser
ES Technology, Concept Laser’s UK distributor, manufactures the parts for the automated suturing device on an Mlab cusing machine using the LaserCUSING process, also known as 3D metal printing. The Mlab cusing is particularly suitable for manufacturing delicate parts where a high level of surface quality is demanded. The special thing about the compact machine is its very user-friendly, pull-out drawer system that is very safe at the same time. This includes both the build chamber with dose chamber and the storage container. It allows a rapid change of material without the risk of any contamination of powder materials. The patented drawer system is available with three different sizes of build envelope (50mm x 50mm x 80mm, 70mm x 70mm x 80mm, 90mm x 90mm x 80mm). Also available now is its big brother, the Mlab cusing 200R, which allows even greater productivity thanks to a doubling of the laser power from 100W to 200W. In addition, a larger build envelope has been created and this increases the build volume by as much as 54% (max. 100mm x 100mm x 100mm).
In this case, the machine technology from Concept Laser makes it possible to produce the teeth of the gear mechanism, which are just 0.4mm long. Up to 600 parts can be printed on one single build plate. After the tooth system has been removed from the powder bed, it does not require any finishing thanks to the very high accuracy of the metal-powder-based process. Stainless steel 316L is used. Alex Berry explains: “In addition to the restrictions on geometry, conventionally milled or cast parts have a few other drawbacks. It takes a great deal of time to get to the finished prototype. In addition, the costs are very high. In 3D printing the parts are produced very quickly and at a fraction of the previous costs of prototyping. But the potential for bionic designs, reproducibility, miniaturization and not least the reduction in the number of parts and outlay on assembly is also vast. If one looks at the full spectrum of optimizing manufacturing and product design coupled with an increase in functionality, 3D printing is capable of revolutionizing medical instruments.”
Latest from Today's Medical Developments
- Kistler offers service for piezoelectric force sensors and measuring chains
- Creaform’s Pro version of Scan-to-CAD Application Module
- Humanoid robots to become the next US-China battleground
- Air Turbine Technology’s Air Turbine Spindles 601 Series
- Copper nanoparticles could reduce infection risk of implanted medical device
- Renishaw's TEMPUS technology, RenAM 500 metal AM system
- #52 - Manufacturing Matters - Fall 2024 Aerospace Industry Outlook with Richard Aboulafia
- Tariffs threaten small business growth, increase costs across industries