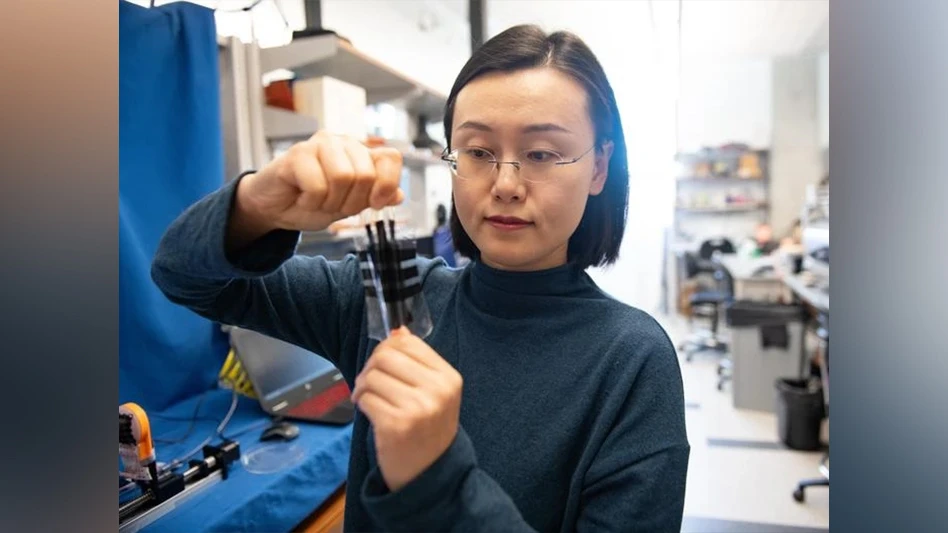
The University of Texas at Austin
A first-ever stretchy electronic skin could equip robots and other devices with the same softness and touch sensitivity as human skin, opening up new possibilities to perform tasks that require a great deal of precision and control of force.
The new stretchable e-skin, developed by researchers at The University of Texas at Austin, solves a major bottleneck in the emerging technology. Existing e-skin technology loses sensing accuracy as the material stretches, but that is not the case with this new version.
"Much like human skin has to stretch and bend to accommodate our movements, so too does e-skin," said Nanshu Lu, a professor in the Cockrell School of Engineering's Department of Aerospace Engineering and Engineering Mechanics who led the project. "No matter how much our e-skin stretches, the pressure response doesn't change, and that is a significant achievement."
The new research was published in Matter.
Lu envisions the stretchable e-skin as a critical component to a robot hand capable of the same level of softness and sensitivity in touch as a human hand. This could be applied to medical care, where robots could check a patient's pulse, wipe the body or massage a body part.
Why is a robot nurse or physical therapist necessary? Around the world, millions of people are aging and in need of care, more than the global medical system can provide.
"In the future, if we have more elderly than available caregivers, it's going to be a crisis worldwide," Lu said. "We need to find new ways to take care of people efficiently and also gently, and robots are an important piece of that puzzle."
Beyond medicine, human-caring robots could be deployed in disasters. They could search for injured and trapped people in an earthquake or a collapsed building, for example, and apply on-the-spot care, such as administering CPR.
E-skin technology senses pressure from contact, letting the attached machine know how much force to use to, for example, grab a cup or touch a person. But, when conventional e-skin is stretched, it also senses that deformation. That reading creates additional noise that skews the sensors' ability to sense the pressure. That could lead to a robot using too much force to grab something.
In demonstrations, the stretchability allowed the researchers to create inflatable probes and grippers that could change shape to perform a variety of sensitive, touch-based tasks. The inflated skin-wrapped probe was used on human subjects to capture their pulse and pulse waves accurately. The deflated grippers can conformably hold on to a tumbler without dropping it, even when a coin is dropped inside. The device also pressed on a crispy taco shell without breaking it.
The key to this discovery is an innovative hybrid response pressure sensor that Lu and collaborators have been working on for years. While conventional e-skins are either capacitive or resistive, the hybrid response e-skin employs both responses to pressure. Perfecting these sensors, and combining them with stretchable insulating and electrode materials, enabled this e-skin innovation.
Lu — who is also affiliated with the Department of Biomedical Engineering, the Chandra Family Department of Electrical and Computer Engineering, the Walker Department of Mechanical Engineering, and the Texas Materials Institute — and her team are now working toward the potential applications. They are collaborating with Roberto Martin-Martin, assistant professor at the College of Natural Sciences' Computer Science Department to build a robotic arm equipped with the e-skin. The researchers and UT have filed a provisional patent application for the e-skin technology, and Lu is open to collaborating with robotics companies to bring it to market.
Other authors on the paper are Kyoung-Ho Ha and Sangjun Kim of the Walker Department of Engineering; Zhengjie Li, Heeyong Huh and Zheliang Wang of the Department of Aerospace Engineering and Engineering Mechanics; and Hongyang Shi, Charles Block and Sarnab Bhattacharya of the Chandra Family Department of Electrical and Computer Engineering. Ha is now a postdoctoral researcher at the Querrey Simpson Institute for Bioelectronics at Northwestern University, and Block is now a doctoral student at the University of Illinois at Urbana-Champaign’s Department of Computer Science.
The new stretchable e-skin, developed by researchers at The University of Texas at Austin, solves a major bottleneck in the emerging technology. Existing e-skin technology loses sensing accuracy as the material stretches, but that is not the case with this new version.
"Much like human skin has to stretch and bend to accommodate our movements, so too does e-skin," said Nanshu Lu, a professor in the Cockrell School of Engineering's Department of Aerospace Engineering and Engineering Mechanics who led the project. "No matter how much our e-skin stretches, the pressure response doesn't change, and that is a significant achievement."
The new research was published in Matter.
Lu envisions the stretchable e-skin as a critical component to a robot hand capable of the same level of softness and sensitivity in touch as a human hand. This could be applied to medical care, where robots could check a patient's pulse, wipe the body or massage a body part.
Why is a robot nurse or physical therapist necessary? Around the world, millions of people are aging and in need of care, more than the global medical system can provide.
"In the future, if we have more elderly than available caregivers, it's going to be a crisis worldwide," Lu said. "We need to find new ways to take care of people efficiently and also gently, and robots are an important piece of that puzzle."
Beyond medicine, human-caring robots could be deployed in disasters. They could search for injured and trapped people in an earthquake or a collapsed building, for example, and apply on-the-spot care, such as administering CPR.
E-skin technology senses pressure from contact, letting the attached machine know how much force to use to, for example, grab a cup or touch a person. But, when conventional e-skin is stretched, it also senses that deformation. That reading creates additional noise that skews the sensors' ability to sense the pressure. That could lead to a robot using too much force to grab something.
In demonstrations, the stretchability allowed the researchers to create inflatable probes and grippers that could change shape to perform a variety of sensitive, touch-based tasks. The inflated skin-wrapped probe was used on human subjects to capture their pulse and pulse waves accurately. The deflated grippers can conformably hold on to a tumbler without dropping it, even when a coin is dropped inside. The device also pressed on a crispy taco shell without breaking it.
The key to this discovery is an innovative hybrid response pressure sensor that Lu and collaborators have been working on for years. While conventional e-skins are either capacitive or resistive, the hybrid response e-skin employs both responses to pressure. Perfecting these sensors, and combining them with stretchable insulating and electrode materials, enabled this e-skin innovation.
Lu — who is also affiliated with the Department of Biomedical Engineering, the Chandra Family Department of Electrical and Computer Engineering, the Walker Department of Mechanical Engineering, and the Texas Materials Institute — and her team are now working toward the potential applications. They are collaborating with Roberto Martin-Martin, assistant professor at the College of Natural Sciences' Computer Science Department to build a robotic arm equipped with the e-skin. The researchers and UT have filed a provisional patent application for the e-skin technology, and Lu is open to collaborating with robotics companies to bring it to market.
Other authors on the paper are Kyoung-Ho Ha and Sangjun Kim of the Walker Department of Engineering; Zhengjie Li, Heeyong Huh and Zheliang Wang of the Department of Aerospace Engineering and Engineering Mechanics; and Hongyang Shi, Charles Block and Sarnab Bhattacharya of the Chandra Family Department of Electrical and Computer Engineering. Ha is now a postdoctoral researcher at the Querrey Simpson Institute for Bioelectronics at Northwestern University, and Block is now a doctoral student at the University of Illinois at Urbana-Champaign’s Department of Computer Science.
Latest from Today's Medical Developments
- The manufacturing resurgence is here – are you ready?
- Workholding solutions for your business
- ZOLLER events will showcase the company’s cutting-edge innovations
- THINBIT’s MINI GROOVE ‘N TURN Acme threading inserts
- CMMC Roll Out: When Do I Need to Comply? webinar
- Metabolic research uses Siemens gas analyzers to deliver results with 99.9999% resolutions
- Mazak’s SYNCREX 38/9 Swiss-type production turning machine
- Current economic and geopolitical realities demand decisive action