
CREDIT: MOTIONARRAY | SEVENTYFOUR, PROVIDED BY CETEC
Medical device startups face unique challenges, from stringent regulatory requirements to complex production processes. Implementing an ERP (enterprise resource planning) system tailored to their needs is crucial for ensuring compliance, efficiency, and scalability.
Whether you are an OEM (original equipment manufacturer) building your own medical equipment, a new contract manufacturing organization (CMO), or a startup manufacturing your own product lines, you will need a structured system to handle both the business complexities and challenges of startup, in addition to those necessities particularly tricky and difficult for medical device companies.
Here are five essential ERP features that medical device startups should prioritize:
1. Traceability
In the medical device industry, traceability is paramount. The ability to track every component of a product from raw materials to finished goods ensures compliance with regulatory standards and facilitates quick and effective responses to recalls or quality issues.
For a medical device startup, full traceability means that if a defect is identified in a batch of products, you can trace back through the entire supply chain to identify where the issue occurred. This capability not only helps in managing recalls efficiently but also builds trust with regulatory bodies like the FDA. Moreover, full traceability supports internal audits and helps maintain a clear history of product lineage, crucial for maintaining high standards and compliance.
Two traceability functions are especially critical when considering an ERP system. First, the ability to track inventory at a lot (or serial) level. Many ERPs only track the quantity of an item and do not tie inventory back to a specific receipt. It is important to show all usage of raw material from the receipt-level as well as from the finished goods level, to track the lots/serials used to make the finished product. Second is the ability to align the ERP with your physical traceability practices in picking and putting away items. This is usually done with barcode scanning where a user prints a barcode label at receipt to be used downstream when inspecting that lot, transferring the product to the warehouse, and picking it to a work order.
2. Integrated quality control (QC) and quality management system (QMS)
Quality is non-negotiable in medical device manufacturing. An integrated QMS within your ERP and MES (manufacturing execution system) ensures that inspections and quality control are driving the reporting necessary to a QMS. Additionally, your production processes are housed in the ERP (assuming it has MES capabilities), meaning that your QMS documentation is tied directly to your use of the ERP. Simplifying this handoff as much as possible helps you gather critical data faster and more accurately and helps you pass audits more quickly, as there are less places to locate and validate the information an auditor is looking for. For example, a failed in-process inspection with the ERP/MES should trigger an NCR or CAPA in the QMS by pulling data automatically and linking back to the source object.
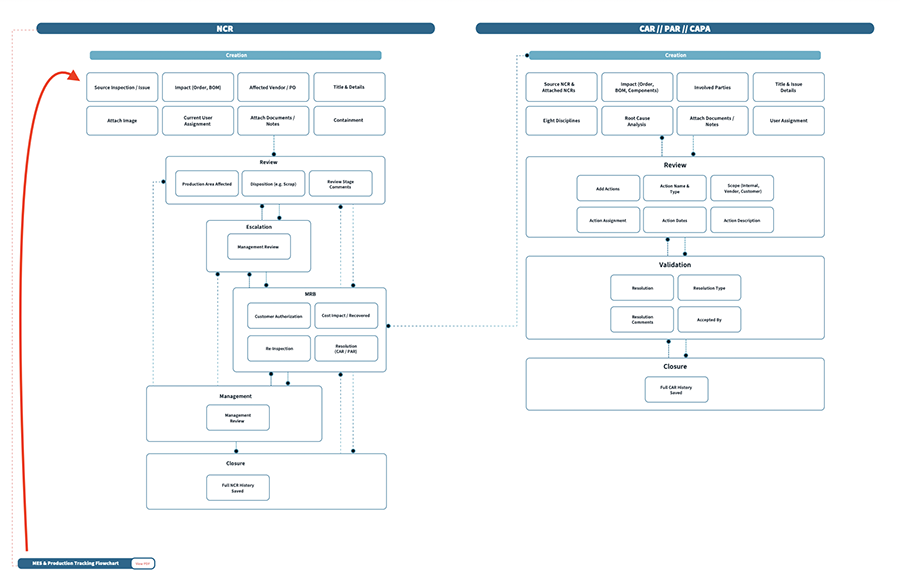
3. Document management and control
Medical device manufacturing involves extensive documentation, from design specs to regulatory submissions to audit portfolios of SOPs, training certs, and more. Efficient document management and control within an ERP system ensure that all documents are easily accessible, secure, and up to date.
A key example of this is work instructions. These are revision-controlled by your quality team but need to be accessed by your shop floor employees in the production process. Having a centralized system that allows for approved documents to be in circulation means you only must store the document once, and it is immediately accessible where it is needed.
4. Production control and tracking
Effective production control and tracking are essential for managing the complexities of medical device manufacturing, from handling large bills of materials (BOMs) to coordinating with multiple suppliers and ensuring timely production.
Having an ERP that can handle production control in a native MES pulls your critical work instructions, required signoffs, and traveler operations directly from the BOM router (or labor plan). When you enter the work order, all that data is available and drives the actual processing of the work order.
You can schedule, you can see and track the movement of the work order through production, you can prevent the next operation from occurring until a required instruction is signed off on, and you can see a full history of who touched or moved this work order over time (for your device history record).
This of course is all in addition to the typical benefits of production tracking intimately integrated with the ERP – it unifies sales with scheduling with purchasing with accounting. And a manufacturing ERP will allow you to manage scenarios and pain points unique to manufacturing like scrap (or yield loss), efficiency data (such as OEE or employee efficiency), accurate cost accounting, and more.
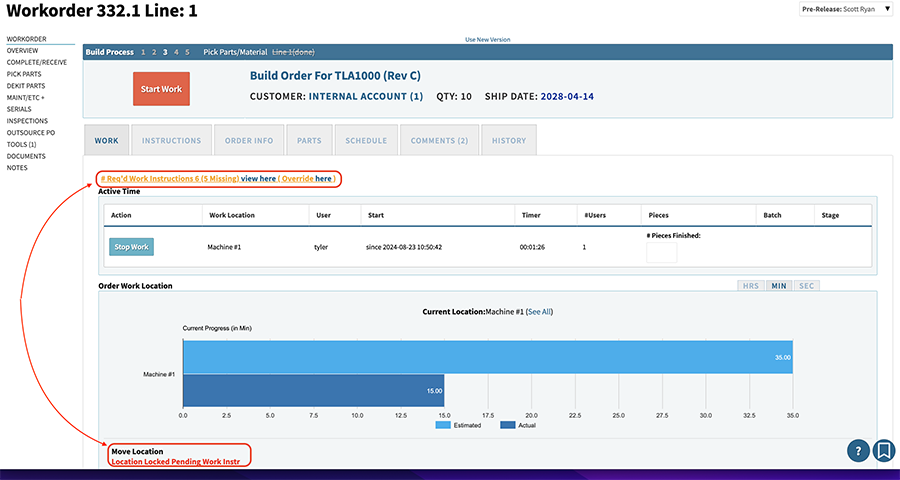
5. Scalability
Medical device startups must plan for growth. An ERP system that scales with your business allows you to add functionalities and users without significant disruptions, ensuring seamless transitions from startup phase to full-scale production. This refers to the technology “under the hood” (e.g. cloud-based solutions are scalable from a technical perspective) as well as the configurability of the system (how easy it is to add new modules or, for an out-of-the-box solution, implement new portions of the software).
Knowing that you are moving towards a system that is flexible to long term needs (it will grow with you) before you have years of history and ingrained process in your culture means the ROI is higher. It is more cost effective to implement earlier rather than later. This also means that your business is supported by a system focusing on best practices, ensuring that your company matures in the right ways.
Considering a cloud-based ERP system
Implementing the right ERP system can have a significant impact on the efficiency, compliance, and scalability of your medical device startup. However, getting set up with the necessary features upfront can be cost-prohibitive to many startup companies. Selecting a cloud-based system can be the solution.
Cetec ERP offers a comprehensive, web native suite of functionalities at a fraction of the cost of traditional ERP systems which makes it especially attractive for small to medium sized businesses. It combines ERP, MRP, CRM, and QMS capabilities in one affordable package, providing significant value without compromising on features.
Designed to streamline operations and grow with your business, the Cetec ERP system adapts seamlessly as your production scales up. This flexibility is essential for startups transitioning to larger-scale operations, and an implemented system helps startups achieve ISO compliance.
With a reputation of robust support and easy implementation, the Cetec ERP system is a practical and cost-effective option, built to handle the complexities of the industry, and tailored to the needs of startups and growing medical device manufacturers.
Get curated news on YOUR industry.
Enter your email to receive our newsletters.Latest from Today's Medical Developments
- Find out the latest developments in tool path strategies for machining
- Building, maintaining the Navy’s next generation of maritime platforms
- Pioneering battery-free cardiac implants
- KBC Tools & Machinery marks its 60th anniversary, Founder’s Day
- Address the challenges of machining high-temperature aerospace components
- Elevate your manufacturing operations with April’s Manufacturing Lunch + Learn
- AdvaMed statement on tariff announcement
- Collets – Not all are created equal