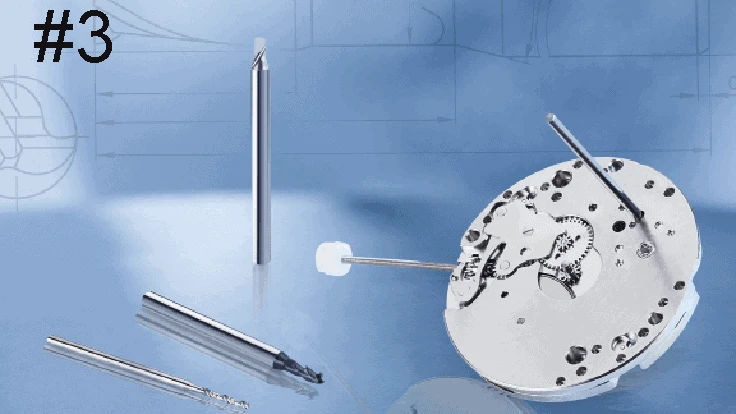
Big Kaiser
Micromachining, cutting where the volume of chips produced with each tool path is very small, is not a high-speed operation in relation to chip load per tooth. Rather, it involves a high spindle speed relative to cutter diameter. The part may be physically larger, but details of the part require ultra-small profiles achieved only by micromachining. In other words, micromachining is not limited in scope to only miniature parts.
Tool holding
In medical work, where tight tolerances are standard, dynamic runout (the measurement of the spindle at high speeds, performed using laser or capacitance resistance technology) and balance must be controlled to deliver and maintain viable tool life. Much of this burden falls on the holder. Balance doesn’t change as spindle speed increases, however the forces it creates increase exponentially alongside speed. The impacting results appear quickly in micromachining.
When runout occurs, the edge most affected takes over the bulk of the cutting. Uneven wear causes the tool to fail more quickly than if the tool rotates about the centerline as intended. In one customer application, we found that drilling into a steel workpiece 0.590" deep with a 0.118" diameter carbide drill in a holder with 0.00008" runout accuracy produced 2,300 holes. A holder with 0.00060" runout accuracy produced nearly two-thirds fewer holes, only 800. In this scenario, the shop could save hundreds of dollars a month in carbide costs – as well as labor costs due to less tool changing – by making one smart tool holder choice.
Holder attributes that can boost production include symmetrical design, a perfectly concentric collapse of the collet around the cutter, and a ball-bearing raceway nut with precision-ground threads.
Latest from Today's Medical Developments
- Auxilium Biotechnologies prints medical devices on the International Space Station
- KYOCERA SGS Precision Tools’ APEX Application Expert
- North American robotics market holds steady in 2024 amid sectoral variability
- Evident’s DSX2000 digital microscope
- Ferrocene becomes first Rust toolchain to achieve IEC 62304 qualification
- Germany expects a major decline in production in 2025
- Learn what you need to comply with CMMC requirements
- VersaBuilt’s CNC automation possibilities