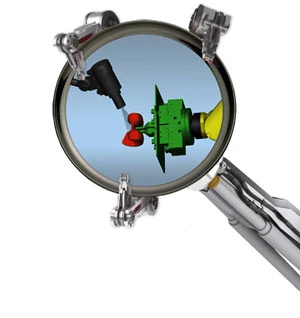
Blast cabinets are a common sight in most medical manufacturing plants where metalworking and machining processes are performed. While some people may regard "sandblasting" as an unpleasant, but necessary process, the technology continues to evolve, and there are signs that media-blast equipment is poised for a major shift toward automation and robotics. The prevalence of cabinet blasting is due in part to the wide variety of engineered shot and grit media now available, enabling blast techniques to be used for many different purposes.
One of the most widespread applications in the production of medical equipment, implantable devices and surgical instruments is cosmetic finishing, in which media such as glass beads, ceramic shot or stainless steel beads are used to blend-in tool marks and superficial imperfections to produce an overall satin sheen appearance that prevents glare and reduces the reflectivity of surfaces. In some cases, such bead-blasting is a specified pretreatment for anodizing, plating or other chemical finishing processes.
Nondestructive blast cleaning is a common requirement for investment cast, forged, brazed, welded, heattreated, laser-cut or laser-drilled medical components. Blasting can also be a fast and effective method of deburring precision components using non-abrasive or semi-abrasive media.
Certain high-stress orthopedic components benefit from metallurgical shot-peening, for which specialized automatic blasting equipment is used.
Finally, abrasive blasting is a primary technology used to prepare surfaces for advanced coatings or critical bonding operations. In this type of technical surface preparation work, it is necessary to produce a specified surface texture or a measurable roughness so the blast system may have special features to ensure that the particular surface condition can be generated repeatedly.
BLASTING TECHNIQUE
A number of factors determine the quality of the blasted surface finish, including the media, the blast equipment and the technique of the operator.
Assuming the blast equipment is adequate, however simple or sophisticated, the factors that have the greatest effect on surface quality center on "the business end" of the machine, inside the cabinet, where the stream of media is directed at the workpiece.
The blast pressure is a key parameter, both because it determines the kinetic energy imparted to the surface in the impact treatment process and because excessive pressure can dramatically increase the fracture rate and attrition of media. Inadequate air pressure can mean insufficient energy to do the work, and pressure that is too high may result in damage to component surfaces. To ensure that the blast pressure is maintained within an established range, the media delivery system may be equipped with sensors to detect a loss of air supply pressure or advanced features to automatically regulate the blasting pressure.
The distance that the blast gun is held from the target surface has a direct effect on the intensity of impact energy, as well as the blast pattern or area of coverage. Holding the nozzle too close or too far away from the part can make the blast finishing process ineffective or alter the blast exposure time required to produce the desired finish.
Another parameter that significantly influences the surface condition produced by blasting is the angle at which the gun is held in relation to the target surface. Media particles that impinge on the surface at the wrong angle can result in shadowing effects, where features of the part interfere with complete coverage. The blasting angle has an especially pronounced effect when grit media are being used to increase surface roughness and produce a specified profile or anchor pattern.
The last factor of blasting technique that has a major impact on the quality of finishing results is surface speed.
Assuming the correct blast pressure, distance and angle are maintained, the motion of the blast nozzle in relation to the target surface translates into exposure time or dwell. Close inspection of the surface finish often makes it obvious which areas of an individual component were underblasted or over-blasted.
AUTOMATED BLASTING
Increasingly, medical manufacturers consider automated blasting as a way to eliminate variation in surface treatment processes and ensure consistent surface quality. Depending on the geometry of the parts, the finishing application, the available cycle time, and the flow of work, a variety of different types of automatic blast machines are used in medical component manufacturing, including tumble-blast, conveyor, rotary table and spindle blast systems. Selection of the appropriate type for a particular blasting application is a careful process, based on the user's requirements.
As compared to manual blasting, an automated blast system brings almost all of the key process parameters under control and provides a high degree of repeatability, as long as the geometry of the components is relatively simple. Bearing in mind the fundamentals of blasting technique, some parts can present a challenge for automated blasting with regard to blast angle, offset and surface speed.
Of course, there are many non-critical blast finishing requirements where this limitation is unimportant. However, when the shapes and contours of the components are complex, and the surface finish is critical, a conventional automated blast system may not be able to meet all of the requirements.
![]() Surface finish from a 90° blast angle |
![]() Surface from a 90° impact crater |
![]() Finish from an oblique blast angle |
![]() Cross section from peak flattening |
ROBOTIC BLAST SYSTEMS
There are two types of robotic blast systems that may be of special interest to medical product manufacturers.
In one type, the articulated robot arm manipulates the suction-blast gun, pressure-blast nozzle or an elongated lance nozzle. The end-of-arm tooling that actually holds the blast nozzle is designed to complement the robot's motions in coverage of target surfaces, and it is robustly fabricated to withstand the action of blast media.
The component may be fixtured on a rotating spindle or table that can be controlled as an additional axis of robotic motion, or the part may be mounted in a fixed position that enables the nozzle manipulator to follow its contours.
In the other type of robotic blast machine, the robot grasps and manipulates the component, presenting the part to a blast nozzle that is locked in a fixed position. This type of system normally requires custom designed end-of-arm tooling in the form of a gripper that will accommodate the full range of components to be blasted, and it utilizes what is called remote tool point motion programming.
The gripper assembly typically incorporates a deflector plate to shield the end-of-arm tooling from media over-spray. The part-manipulating robot may be located in an antechamber between the load/unload station and the blast enclosure.
While these industrial robots are supplied with a teach pendant for development of motion programs, there are now faster and more precise methods based on machine tool CAD/CAM technology. Robot motion programming begins with the creation of a parametric 3D model of the component that accurately represents all features of the part, as well as the end-of-arm tooling and structural features of the blast cabinet. The programming process is performed off-line, or even remotely, so production continues uninterrupted.
Parameters such as the distance from the nozzle to the part, the angle of the nozzle in relation to the target surface, and the speed at which the surface is traversed are set as rules of the CAD/CAM motion program. Unlike teach-pendant programming, the toolpaths of the blast gun are not based on the care and best reckoning of the programmer, but are among the most efficient execution of all the required nozzle movements.

A look at the cosmetic finish of a medical implant before and after blast-cleaning.
BENEFITS OF ROBOTIC BLASTING
Robotic blasting and advanced motion programming will have a dramatic impact on surface quality.
Even when blasting components of the most complex shape, the correct angle, offset and surface speed are constantly maintained. Operator errors in blast gun and part manipulation can be eliminated, and the limitations of conventional automatic blast machines can be overcome, resulting in a major improvement in the degree of consistency in quality.
There are many more advantages of robotic blasting that appeal to those who engineer and produce medical components. One of the foremost is that, once a complete process recipe is established for a particular component, it can be stored and recalled at will, and the need for most blast machine set-up and adjustment procedures is eliminated, no matter if a short or long run of a particular part is required.
Other obvious benefits of the conversion to robotic blasting are labor and re-work savings, and the fact that human operators are freed for other work that demands their intelligence and judgment.
Any process equipment change in medical manufacturing operations entails many costs related to validation, in addition to the investment in new machinery. In the cost/benefit analysis, the value contributed by robotic blasting in terms of product quality and production efficiency compares very favorably for critical surface finishing applications.
Guyson Corp.
Saratoga Springs, NY
guyson.net

Explore the July 2009 Issue
Check out more from this issue and find your next story to read.
Latest from Today's Medical Developments
- Global Industrie - A meeting to understand, anticipate and contribute to the industry of tomorrow
- Wintriss’ Tracker Hardware Solution for ShopFloorConnect Production Tracking Software
- Protolabs expands end-to-end manufacturing capabilities
- Sunnen’s HTE-1600W Tube Hone
- Researchers invent soft, bioelectronic sensor implant
- HEULE’s DL2 tooling
- Application Park shows off diverse robotics applications
- Join our editors for a look at the manufacturing industry in 2025