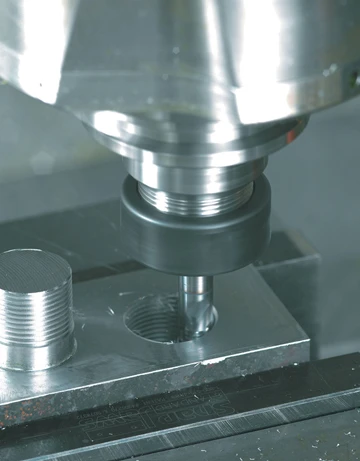
Tapping has generally been viewed as the most appropriate technique for the threading of small holes. However, within the medical industry, where stainless steel, titanium and high temperature alloys tend to be the materials of choice, tapping becomes problematic as the tap can often snap inside the workpiece especially in these materials. One answer to this problem is to switch to thread milling, which has historically only been considered for larger holes or those over 0.500 inches (12.7 mm). But, with the recent advent of smaller, improved solid carbide inserts such as Seco-Carboloy's TiCN-coated Threadmaster mills, threadmills are beginning to make their mark in many shops that thread holes as small as 10-32 or M4 ID thread (0.1575 inches).
However, to gain the full benefit of thread milling, a careful and deliberate system of application is mandatory. First and foremost, a CNC machine with the capability of helical interpolation is required. Next, is the issue of creating the sophisticated threadmill program. In the past, it was necessary for a machine operator or manufacturing engineer to write and understand the necessary computer program for thread milling. But today, cutting tool manufacturers offer easyto- use thread milling software for free. For example, Seco-Carboloy's Wizard program simply requires that the operator enter the type of thread, diameter, depth, and group of work materials that he is cutting. The software then generates the machine code automatically. It also recommends the best cutter for the job and selects the optimum cutting parameters. In addition, the software adds tricks of the trade in the logic of the software.
Next step is the milling of the hole. Since thread milling is much freer cutting, it does not require the same power that is needed for tapping. Compared to tapping, threads made by milling are much more accurate, and far superior. This can be illustrated by cross-sectioning a thread-milled hole and a tappedhole and looking at the results under magnification. The tapped hole will appear a bit jagged because, in tapping, the tap's flutes cut in where the chips tend to get caught and can jam the tap. Sometimes this will tear the thread. In contrast, a threadmill starts at the bottom of the hole and works its way up providing clear space into which the chips can fall. Additionally, thread milling can address a range of hole diameters instead of just one hole size and it can combine various hole-making operations into a single operation.
And, a threadmill can tweak the size of the thread with an easy CNC command. Thread milling provides 100% thread depth, so the machinist can actually leave some extra material on the stock - 0.0002 to 0.003 inches- and the threadmill will deal with it.
Lastly, thread milling is considered safer than tapping. If a threadmill insert breaks, it will drop down into the hole and needs to be picked out versus dealing with a jammed tap and a potentially wasted workpiece. So, you get fewer scrapped parts and increased profitability.
Overall, thread milling leads to improved quality, longer tool life (up to 500 percent increase as compared to tapping in certain applications) and it can be more economical. With the advent of smaller, solid threadmill sizes suited for medical applications and the availability of software to automatically create your thread milling programs, there shouldn't be any hesitation about converting your shop.
Seco-Carboloy
Warren, MI
carboloy.com

Explore the June 2006 Issue
Check out more from this issue and find your next story to read.
Latest from Today's Medical Developments
- Birk Manufacturing achieves ISO 13485 recertification
- SW North America's BA 322i twin-spindle CNC
- The role of robotics in precision medical device manufacturing
- Swiss Steel Group’s UGIMA-X machinable stainless-steel sets
- #51 - Manufacturing Matters - The Impact of M&A in MedTech 2024
- Visual Components: 25 years of simulation and programming software innovation
- Zimmer Biomet announces definitive agreement to Acquire Paragon 28
- Discover an innovative technology for EMI/ESD/TVS suppression