Edited by Elizabeth Engler Modic
Developing a new product via consultation, design, production, testing, logistics, integration, and support can be challenging for even the best original equipment manufacturers (OEMs). In highly regulated industries such as medical, security, and defense, products must not only meet stringent regulations, they also must perform in extreme environments where resistance to temperature fluctuations, humidity, and vibration shock is critical.
Methodologies
So how does one go about choosing a methodology that is quick to adapt to change, yet thorough enough to cater for quality control and planning?
Project management methodologies can be categorized into two areas. First are the traditional formal methods, which include Products in Controlled Environments (Prince2), Six Sigma, product management body of knowledge (PMBOK), total quality management (TQM), quality function deployment (QFD), and the waterfall model. The second, emerged from this, includes lean, agile, just in time (JIT), Toyota Production System (TPS), and Kanban.

Suit up
The formal methodologies all prescribe a holistic, start-to-finish approach to process-driven environments where quality of output must be maintained while reducing the variability of each output. Whether it’s business or manufacturing, formal methods are all about measurable, quantifiable, result-oriented outcomes. This includes cost reduction, optimized time management, and a deep understanding of inherent risks and benefits of each action.
Great for large-scale, often multinational projects, formal methods can be difficult to administer. They are usually resource intensive, inflexible, and bureaucratic, making them difficult to roll out in smaller projects.
Going lean
At the other end of the spectrum are the lean methodologies – all about reducing a process to its core activities, improving efficiency, and reducing waste in the process. Lean systems add value by reducing costs and improving delivery times while maintaining quality.
One of the biggest criticisms of lean is that it focuses on optimizing a single activity, often leading OEMs to lose sight of the bigger picture. Scope-creep can mean projects lose direction strategically and inaccuracies in lean processes can magnify across the project if not managed carefully. A lack of documentation can lead to traceability problems when things go wrong.
Pick your poison
To establish which is best, consider three issues – external environment, internal setup, adaptability. Take Accutronics, for example. The company’s external environment operates in many highly regulated, life-critical, and extreme environments – designing and manufacturing batteries and chargers for medical and healthcare, security, and defense. For the company, it’s important to demonstrate traceability, documentation, and thoroughly tested products while hoping to achieve a competitive advantage by understanding the subtle demands of customers.
In the second and third stages, OEMs must ensure that physical resources, infrastructure, and human expertise are leveraged in such a way that they can adapt to market changes quickly and smoothly, and to changes in legislation, innovation in materials research, or technological obsolescence.
Accutronics Ltd.
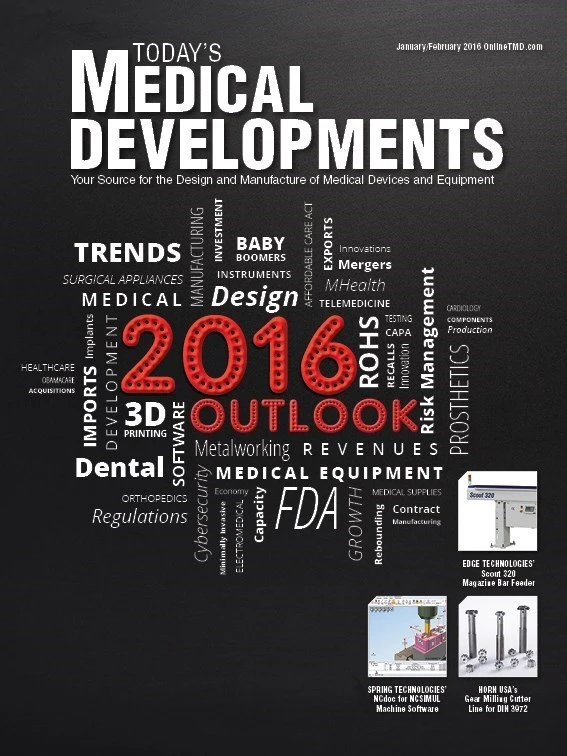
Explore the January February 2016 Issue
Check out more from this issue and find your next story to read.
Latest from Today's Medical Developments
- Best of 2024: #4 Article – Sticking to the basics
- Best of 2024: #4 News – Point of care manufacturing
- Best of 2024: #5 Article – Accelerating medical device development with freeform injection molding
- Best of 2024: #5 News – Complexity, the enduring enemy of medical cybersecurity
- Best of 2024: #6 Article – Closing the global product information gap
- Best of 2024: #6 News – NUBURU enters medical device market with order Blueacre Technology
- Season's greetings
- Best of 2024: #7 Article – Synchronized machining processes for medtech