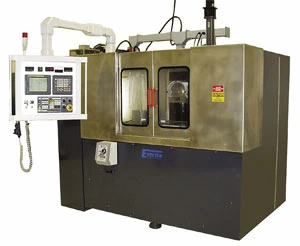
Scientific and metallurgical developments have placed unusual demands on the metalworking industry. The challenges include modern materials with high strength-to-weight ratios, and new fabrication requirements that demand greater precision and surface integrity.
Electrochemical Grinding Equipment (ECG) is a machining process that provides a better, faster, and more cost-effective metal cutting and grinding solution for today's toughest materials. Unlike conventional grinding techniques, Electrochemical Grinding offers the ability to machine difficult materials independent of their hardness or strength. This is because Electrochemical Grinding is an entirely different machining process in which electrical energy combines with chemical energy for metal removal. Since Electrochemical Grinding Equipment does not rely solely on an abrasive process, the results are precise cuts free of heat, stress, burrs and mechanical distortions.
ELECTROCHEMICAL REACTION
Electrochemical oxidation and reduction
occurs on the surface of electrodes
when an electric current is passed between
the electrodes, through an electrolyte
fluid. An electrochemical potential
between the electrodes causes current
to flow from the anode to the cathode in
the DC circuit. In Electrochemical Grinding,
the anode is the workpiece, and the
cathode is the conductive grinding wheel.
A continuous stream of electrolyte flows
at the interface of the grinding wheel and
workpiece, and conducts the current in
the circuit. The electrolyte fluid is a conductive
aqueous solution consisting of a
mixture of chemical salts and other additives.
As the positive electrode, or anode,
oxidation of the workpiece dissolves the
surface of the metal, it forms a metal oxide
film. The film is electrically insulating, and
acts as a barrier against the electrochemical
cutting action of the process.
The abrasives in the rotating grinding wheel continually remove this film and expose a fresh surface for oxidation. Metal deposition on the grinding wheel (cathode) is avoided by proper choice of electrolyte. Dissolution of the metal, combined with the mechanical removal of the oxides, results in an efficient, low-stress cut.
ELECTRICAL ENERGY
According to Faraday's Laws, the
quantity of chemical change occurring
at an electrode is directly proportional to
the amount of current passing between
the electrodes. Low voltage and high
current electrical energy supplied by a
properly designed DC power supply is
central to the Electrochemical Grinding
process. Since the voltages are low, spark
discharge and the associated heat are
avoided. In addition, the low voltages
used prevent any electrical shock hazard
to the operator.

Everite's most popular ECG machines.
PRODUCTIVITY FACTORS
With Electrochemical Grinding, the rate
of metal removal is directly proportional
to the current flowing across the contact
surface between the wheel (cathode)
and workpiece (anode). The higher the
amperage, the faster the rate of chemical
change and stock removal. "Machinability"
of a metal depends more upon its
conductivity and electrochemical reactivity
than its hardness or strength. Electrochemical
Grinding Equipment can be
used successfully on all electrochemically
reactive and conductive materials.

Explore the March 2007 Issue
Check out more from this issue and find your next story to read.
Latest from Today's Medical Developments
- Tariffs threaten small business growth, increase costs across industries
- Feed your brain on your lunch break at our upcoming Lunch + Learn!
- Robotics action plan for Europe
- Maximize your First Article Inspection efficiency and accuracy
- UPM Additive rebrands to UPM Advanced
- Master Bond’s LED415DC90Med dual-curable adhesive
- Minalex celebrates 60 years of excellence in miniature aluminum extrusions
- Tormach’s Chip Conveyor Kit for the 1500MX CNC Mill