
Flex (formerly Flextronics) builds an insulin pump – about 4cm x 3cm x 1cm – that attaches to the patient’s skin. A program running on the patient’s personal digital assistant (PDA) controls the pump and keeps track of when an insulin injection is needed. When the PDA gives the command, a small needle pops out of the device and injects insulin into the patient. The device typically remains attached to the patient for about three days and while attached, the patient can shower or swim. Inside the device is a complex mechanism that safely inserts the needle into the patient’s skin. Six different areas of the pump interior need close-tolerance inspection to ensure safe operation.
When production began, 20 to 25 quality control inspectors with microscopes manually inspected the interior of the insulin pump just before the case was sealed. Inspections include the position of the needle, the track that the needle rides on, and the mechanism that traps the needle. With the inspection criteria primarily subjective, it was possible for one inspector to pass a part that another inspector would reject. The product’s critical nature makes it essential to reject assemblies if there is the slightest possibility they might not perform their function. The result is that only 85% of production initially passed manual inspection.
Vision system required
Flex and the insulin pump company agreed to develop a vision system to ensure inspection to an objective standard to reduce manufacturing costs. Engineers first considered using conventional cameras, frame grabbers, and writing software but determined it would take 18 months to develop.
“The program needs to be written from scratch, which can be very time-consuming,” says Pablo Espinosa, senior design engineer for Flex in Aguascalientes, Mexico. “Usually the most difficult part is writing an algorithm that identifies a reference point on the part from which to begin the inspection. This must be done before beginning the inspection because each assembly will be in a slightly different position when its image is acquired.”
Instead, the company used six Cognex In-Sight vision systems that Flex engineers programmed using a graphical interface to select pre-built algorithms.

Pre-written algorithms save time
Espinosa started by contacting the Cognex Latin American (LATAM) group who helped determine the field of view, working distance, and resolution required for each inspection operation. Cognex LATAM recommended the use of three In-Sight 1100s, two In-Sight 1402s, and one In-Sight 1403 vision system. While he was awaiting delivery, Espinosa worked on the vision programs using a camera borrowed from Cognex. Espinosa used the Cognex In-Sight Explorer software to select and configure the algorithms needed to inspect the part.
“All of the algorithms are pre-built so I was able to build the code in much less time,” Espinosa notes. “I started each inspection operation by using the PatMax algorithm to identify the location of the assembly. Then I used blob tools to check for the presence of specific parts, edge tools to identify the location of the part, and caliper tools to measure the distance between two edges.”
Espinosa dragged these tools into a spreadsheet to create each of the inspection operations, having the basic program ready in four weeks. Once the cameras arrived, he spent two weeks fine-tuning and finalizing the code.

Operation of dial machine
The rotary dial machine is controlled by a programmable automation controller (PAC). The operator loads a part into the first station and hits the start button. The machine indexes, and the part moves to station number two where a vision system inspects a corner of it. Each time the machine indexes, the PAC sends a command to each vision system to acquire and process an image. Each camera sends its inspection results to the PAC. The part then indexes to station three where another vision system inspects the top of the part. At station four, two vision systems simultaneously inspect two sides of the part. In this station there was not enough room to mount the cameras aiming directly at the product so right-angle mirrors mounted near the sides of the part reflect images to cameras mounted above. At station five, two additional vision systems inspect the other two sides of the part. The six vision systems inspect every area of the part except for the bottom, which does not require inspection.
If the product passes all six inspection operations it is loaded onto a conveyor where it travels to final assembly. The human machine interface (HMI) identifies products that fail inspection, which are then removed by an operator, placed in a container, and taken for repair or disposal. At the end of each inspection operation, the file transfer protocol (FTP) tool in the Cognex cameras sends images to the computer that runs the HMI. The inspection images for each camera are displayed on the HMI and operators can call up earlier images to investigate problems and identify root causes to improve the manufacturing process.
The indexing machine, vision systems, PAC, and HMI were all shipped to Asia for installation in the manufacturing site. Espinosa and Marco Esquivias, the engineer leading mechanical design of the test station, spent only two weeks in China supervising the installation of the machine. When Espinosa returned, he helped resolve issues that arose during the prove-out stage by logging into the HMI and viewing live inspection images on his desktop computer.
“We were able to program six extremely complicated inspection operations in only six weeks by making use of Cognex pre-built algorithms,” Espinosa says.
Flex
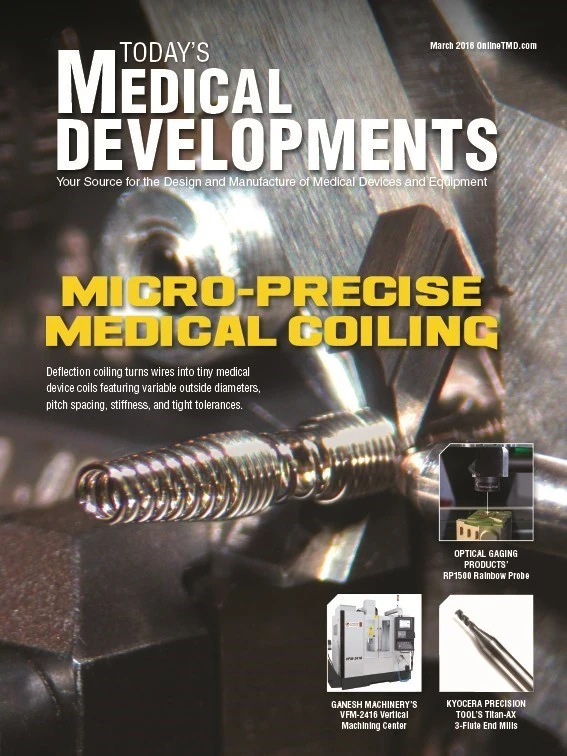
Explore the March 2016 Issue
Check out more from this issue and find your next story to read.
Latest from Today's Medical Developments
- MedTech Innovator welcomes five new industry partners
- First Article Inspection for quality control
- The manufacturing resurgence is here – are you ready?
- Workholding solutions for your business
- ZOLLER events will showcase the company’s cutting-edge innovations
- THINBIT’s MINI GROOVE ‘N TURN Acme threading inserts
- CMMC Roll Out: When Do I Need to Comply? webinar
- Metabolic research uses Siemens gas analyzers to deliver results with 99.9999% resolutions