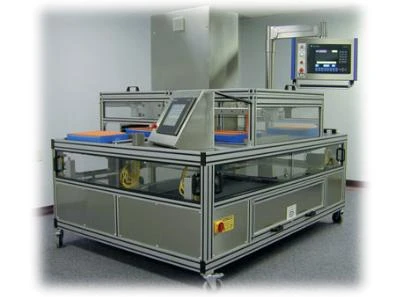
Quality, accountability and product reconciliation are production mandates at Eli Lilly and Company, Indianapolis, IN, which is why the leading pharmaceutical manufacturer has automated its mechanical vial counting process. The company enlisted Clarke Engineering Services Inc., an Indianapolis, INbased systems integrator that specializes in vision system integration, commissioning, installation, and validation for the pharmaceutical and diagnostic industries. Together, Eli Lilly and CES codeveloped a groundbreaking tray inspection system using a color visual inspection process powered by InSight machine vision sensors from Cognex Corporation, Natick, MA. This quality inspection system, dubbed TIS3000, is reportedly the first fully integrated tray inspection system for the pharmaceutical industry that combines machine vision with automatic tray handling, to enable one hundred percent accountability of products.
While Eli Lilly's mechanical counter provided only vial count, TIS3000 uses machine vision to perform a visual inspection that detects fallen vials, identifies missing flipseals, and verifies cap color on each vial. As a result, the tray inspection system improves product quality, in addition to increasing vialcounting efficiency for one hundred percent product reconciliation.
By counting vials in trays at the front end of a packaging line, TIS3000 helps Eli Lilly eliminate countrelated deviations and resultant rework as specific job lots are run. This saves money, time, and resources required for costly reworks. "The TIS3000 establishes the initial count on our packaging line," explained Rob Stapleton, Operations Team Leader at Eli Lilly. "If the numbers do not reconcile at the end of the line, we have to open up the entire job and find out why a discrepancy exists. This can be very costly and time consuming considering packaging order sizes range up to 360,000 vials."
Eli Lilly and Company also noted that the existing mechanical counters that were being utilized were prone to jams and that operators could easily mishandle vials around the counters resulting in a count discrepancy. This made identification of root causes for mechanical counter errors difficult to identify. A major benefit to the new tray inspection system is that root causes to count deviations are easier to identify, correct, and explain.
First a feasibility study
In selecting a vision system, two primary criteria were used, according to CES President Chris Clarke. "First, the system chosen would need powerful vision tools to meet Eli Lilly's demand for accuracy and repeatability to comply with ever more stringent regulatory requirements," Clarke explained. "Second, it had to be very simple to use, so operators with no vision experience could easily modify the inspection onthefly during product changeovers."
Several criteria were needed for the system to be successful in meeting Eli Lilly's requirements. The vision system would have to establish a tray count, look for vials that have fallen over, check that flip seals are in place, and inspect for vials with the wrong color caps, called strangers. After evaluating a number of systems, CES selected the InSight 1000C color machine vision sensor from Cognex. The sensor combines a DSPbased visionprocessing unit with a 640 x 480, 8bit progressive scan digital vision camera in a compact housing with built in communications, and a library of vision software tools.
"We tested several systems to prove which could do the job, then selected the vision system based on the results," said Clarke. "Cognex tools were more robust for this application than the other vision tools we evaluated, and the powerful preprocessing filters helped us achieve the desired inspection results. The Cognex vision tools provided the most robust solution." The image preprocessing filter tools that other systems offered were not extensive enough to accomplish the inspection goals for the vial trays used by Eli Lilly. The total count of each tray was not repeatable and therefore not reliable. Filter tools could not easily be referenced together in order to obtain a refined preprocessed image. Also, to obtain realtime counts of a tray being inspected, additional frontend programming would be required within the other systems evaluated.
Due to Cognex's unique spreadsheet interface the user can also use one filter to look through another filter resulting in a further preprocessed image for blob counting. The software is user friendly to navigate through and making changes to the program, or adding a new product.
System set up
To set up the application, CES used the InSight vision spreadsheet interface. The process involved selecting vision tools and parameters from dropdown menus. The vision spreadsheet then automatically generated tool results into worksheet cells, which were then linked together to set up the inspection.
CES used InSight's blob analysis tools to count the number of vials and determine cap shape, and color histogram tools to verify cap color in order to identify strangers. Additionally, the vision sensor was trained to distinguish specific colors using hue, saturation, and intensity.
The TIS3000 features AllenBradley controls. A SLC5/04 PLC handles sequential control and logic. Communications are handled via hardwired discrete I/O (Input and Output), serial data transfer and DataHighway Plus. A PanelView 1000 mounted on a pivoting arm serves as the main operator interface for program selection, fault display and maintenance functions.
At Eli Lilly's request, the TIS 3000 also incorporates an industrial PC from Advantech, Cincinnati, OH. Mounted within the inspection hood, the industrial PC runs a custom Visual Basic frontend interface developed by CES.
The result is a flexible vial counting and tray inspection system that can be run by a single operator with minimal machine vision knowledge, and handles a wide range of tray sizes with minimal mechanical changeover. The TIS3000 can run Lilly's largest tray configuration at over three trays per minute which equates to over one thousand vials per minute. The system speed capabilities are well within the packaging line speed requirements of 320 vials per minute.
Easytouse tray inspection
During the inspection process, the operator first selects the program and inputs the data required for a given product run and then loads a tray onto the load station. The TIS 3000 uses three counting programs; each designed to handle a different type of count. The most common is a fixed tray count where the operator selects tray style, the specific count for that tray type, and cap color. "Trays that don't meet these test criteria, would be rejected," explained Clarke.
Operators can also choose a manualinput program scripted for counting new tray styles that aren't yet programmed into the system. For example, if the manufacturer comes out with a new style tray designed to hold 100 vials, the operator programs the system to handle this count by selecting manual count, and entering 100. Once again, if the count isn't met, the tray is rejected. The third type of count handles random counts, such as when the operator must establish counts for various tray styles each containing a different number of vials. In this instance, the system inspects as usual, but accepts all counts, while recording individual tray counts as well as the total count of all of the trays in the production run. After selecting the count type, and entering the necessary data for a given product run, the operator places a tray onto the load station.
An indexing conveyor belt with cleats carries the tray full of capped vials into the inspection area. Inside the hood, linear highfrequency fluorescent lamps, complemented by a custom designed dome, provide cloudy day illumination to enhance the features of interest. A single InSight vision sensor, suspended in the hood above the tray, captures the image of the tray and vials.
After applying filters to preprocess the image, an onboard microprocessor analyzes the image, compares it with stored data that comprises a standard, and makes the passfail decision, which is output to the main system controller. If the tray contains the correct number of vials, it passes the inspection area, and is indexed to the unload station. A second PanelView 1000 mounted on the back end of the machine downstream of the unload station displays the actual tray count data. The operator verifies this count with the expected total, which is printed on a tag attached to the tray. Once verified, an operator lifts the passed tray off and places it onto an accumulator table for further processing.
If the tray fails, a servocontrolled reject arm transfers it to the reject conveyor, unless cap of the wrong color is identified. "If a stranger is detected, the system locks up and requires supervisor intervention in order for the tray to proceed to the reject station," said Clarke. "This is an important feature in order to errorproof the process to prevent the wrong medication from being packaged into a lot."
Trays that fail due to a wrong count or downed vial error are automatically cycled back to the load station operator on the reject conveyor. As the tray returns, the operator can see the cause of failure on the pivotarm display. For example, it will say either down vials or incorrect tray count so the operator can correct the problem and send it through again. "Defective trays do not make it past the inspection station if it doesn't meet the test criteria," Clarke said.
System Benefits/Applications
The first systems that have been installed are being used for accountability purposes on packaging lines to reconcile incoming lot counts with final order counts. Additional applications for the TIS3000 include 100% accountability of vials, syringes, cartridges, and ampoules for controlled substance manufacturers that are required by law to account for any product diversion during the manufacturing and packaging processes. The TIS3000 concept can be utilized to establish initial lot counts and monitor lot counts throughout the controlled substance manufacturing/packaging process steps. The TIS3000 enables 100% accountability of all products throughout the process. Where manufacturers have colorcoded product vials the system can be utilized for Nude Vial (Bright Stock) Identification.
Clarke Engineering Services, Inc. has also developed a smaller footprint Tray Inspection System (TIS2000) that is approximately half the footprint of TIS3000 but does not incorporate a reject conveyor system. This system can be used for slower speed lines and offline inspection activities. In addition, an online printer to print and apply labels to product trays is available as an option.
System Validation
A comprehensive validation package including engineering, functional and computer system validation documentation was developed for Eli Lilly and Company. The TIS3000 has been tested and validated down to unit level testing and has successfully passed Eli Lilly's stringent validation requirements. Two TIS3000 systems have been installed and validated at Eli Lilly's Indianapolis, Indiana manufacturing facility.
Business Benefits
A significant improvement in vial accountability on both lines where the TIS3000 systems have been implemented has been demonstrated and measured in the parenteral packaging area. The tray inspection systems have also eliminated the need for inprocess "count checks" required as part of the mechanical counting process resulting in less documentation requirements and improved line efficiencies.

Explore the May 2005 Issue
Check out more from this issue and find your next story to read.
Latest from Today's Medical Developments
- Tariffs threaten small business growth, increase costs across industries
- Feed your brain on your lunch break at our upcoming Lunch + Learn!
- Robotics action plan for Europe
- Maximize your First Article Inspection efficiency and accuracy
- UPM Additive rebrands to UPM Advanced
- Master Bond’s LED415DC90Med dual-curable adhesive
- Minalex celebrates 60 years of excellence in miniature aluminum extrusions
- Tormach’s Chip Conveyor Kit for the 1500MX CNC Mill