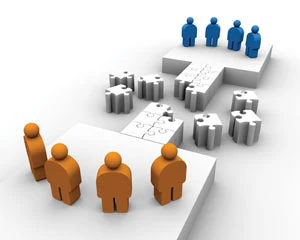
If necessity is the mother of invention, Johnson Medtech can make the case that technological expertise is the sire of spin-offs in the medical device industry.
From large global firms to small innovative startups, medical device manufacturers have access to high-quality, end-to-end design, prototyping and manufacturing capabilities from Johnson Medtech. And all because micro-motors, solenoids, switches, sensors, flexi-circuits and device assembly, just some of Johnson Electric's areas of expertise, helped spawn its newest division.
"What we discovered is in our various businesses throughout the world, we had basically gotten into the medical device industry in a big way, and we decided to really focus on that as a long-term strategy for the company," explains Jim Dick, senior vice president, Johnson Electric. "Most medical companies are spending too much time managing multiple suppliers, navigating the complexities of outsourced manufacturing, and making engineering compromises. This impacts their time to market and profitability. Johnson Medtech provides the solution for medical device manufacturers. Our local consulting and engineering services, combined with the most advanced manufacturing and prototyping processes, provide our customers with a competitive edge. Our focus is on design for manufacturability and complete vertical integration."

Clinical measurement and laboratory solutions are another specialty that have seen increased time-to-market when utilizing the VIP Center.
Reflecting that is Johnson City, a five million square foot, 35,000+ person facility in Shajing, China. A huge production complex running 24/7, 330 days a year, it boasts the capability to produce a product from start to finish, and now has the addition of Value Innovation Process Center (VIP Center) in the middle of it all.
The VIP Center looks more like a world-class hospital than a production facility; this hospital look-alike boasts ISO 13485 approval.
Speeding Development
Leveraging the variety of system and component design facilities Johnson Electric has around the world is the name of the game. The capabilities range from medical innovation centers, to subsystems and sensors, to tooling and prototyping technology. The ability to machine and make parts right on the spot enables faster time-to-market when working at the VIP Center. From prototyping and engineering phases through the final product, there is a competitive advantage to the customer, as well as a cost-effectiveness inherent in the product.
So, what began as internal product development process improvements for many of Johnson Electric's other businesses, has turned into the basis for the VIP Center in China.
"The uniqueness about the VIP Center is because we are so vertically integrated, we bring in engineers from our customers and we might start off with them wanting seven design concepts," explains Dick. "Some companies want to send their engineers over for a couple of days to ‘walk through' the project with us. However, when we tell them to send the engineers for two or three weeks, they think it's a little strange at first, but then they do send them for that long and the end results are just tremendous."

Precision grinding equipment enables Johnson Medtech to rapidly deliver prototypes, increasing the efficiency of production.
First, Johnson Medtech brings in their process engineers, component engineers – whether it's the metals guys, the plastics guys, the tooling guys, the fixturing engineers, etc. – and they start looking at all the concepts the engineers have brought over to figure out how to make them better. The huge benefit here is that the VIP Center, sitting in the middle of a huge production complex, enables those engineers to start making samples immediately.
When the concepts are finalized, the next step is to make soft tools, investment dies for castings, etc. This is all done overnight so the samples are available for review the following day. If the engineers find it might take longer to make a tool, it is sent to the EDM or the CNC shop for production.
"We typically find the best process of bringing everyone together where they have immediate access to any technology they like to make their component," says Dick. "We are able to get samples of parts in the customer's hand very quickly, and once they start working with that, you can really start refining the design process."
Once the design process is chosen, the next step is to move to One Piece Flow — another step used for process improvement that originated in Johnson Electric's mass-production facilities. One Piece Flow is like Just In Time or Kaizen, only this is for engineering and nothing moves to the next station unless it's perfect.
"Customers that come to Johnson City's VIP Center get their own laboratory, their own office, their own management room, etc.," Dick explains. "Also, they are working with the same staff on that same project from phase one to phase 20, or phase 100. So, once the sample is approved, we set up a station with a sample of what we want to deliver and One Piece Flow begins."
Accountability
All of the components, the deliverables are put on this station and there's a timeline of when each component needs to be delivered. There's also a manger that watches each project and if any dates are missed then everyone involved is accountable – from the customer, down to the sales person, and everyone in between.
"If the One Piece Flow breaks down, then everyone involved in the project must report to the station the next day. Once together you can face-to-face discuss the problems and come up with a resolution, which is where the huge timesavings is seen," says Dick. "This is one of the main benefits of this VIP Center, you avoid two weeks of emails, phone calls and lost production time because everyone comes together to work together and correct issues, immediately."
One example Dick shares is a company that agreed to send its engineers for the three weeks versus the two or three days. When they first got to Johnson Medtech, they had a timeline that was measured in many months. After the three weeks working in the VIP Center, utilizing the One Piece Flow, Johnson Medtech got the part down to a number of weeks.
"Another added benefit to the customer was they had originally assumed they would have eight suppliers," says Dick, "However, we got that down to one supplier, eliminating the whole supply chain management issue if something doesn't work with one of your suppliers. This is how Johnson Medtech is able to gets things done at least 50% faster."
Since the production engineers enter the picture at the very start, and don't leave the process until the project is complete, there's the continuation of One Piece Flow into the full production of the finished project. Known as Johnson Electric Production System (JEPS), once a product is actually in production and you begin to have usual logistic problems arise, the production engineers that have been on the project since day one talk directly to the customer's production people. "At this point, there is no longer a middle man in between the communications of our factory people and our customer's factory people," explains Dick. "Everyone is always talking to one another throughout the process, so even though this is post-design, the VIP process, the One Piece Flow project management, and the JEPS are all working together to increase time to market, from the very start, to the very end."
Business Innovations
In addition to capitalizing on Johnson Electric's expertise in the Shajing facility, Johnson Medtech also utilizes the knowledge of the other business groups under the Johnson Electric umbrella.
Johnson Motor specializes in DCmicro- motors and gear motors for precision medical applications. Ledex works in precision solenoids for medical device and other industries. The company that develops and manufactures ceramic servomotors, precision positioning systems and piezo motion solutions is Nanomotion. Parlex offers design, prototyping, assembly and custom manufacturing for flexible circuits and non-invasive sensors for hundreds of medical devices. Saia is a leading brand of stepper motors and micro-switches for medical subsystems.
Citing the success of the VIP Center in Shajing, and having these distinct divisions around the world, has led Johnson Electric to plan on opening additional VIP Centers in conjunction with these industry divisions in the near future.
The problems customers bring to Johnson Medtech to solve are always unique. Quite often, they require re-engineering and re-design aspects. Most customers have the clinical experience, but not all have the engineering or design know-how. Perhaps they need to change the motion of the pumps, or the control device; they might want something smaller, quieter and more efficient. Perhaps it's making a device more portable. Whatever the need, Johnson Medtech works from the subsystem level up, to deliver the quickest time-tomarket product.
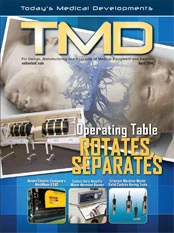
Explore the April 2008 Issue
Check out more from this issue and find your next story to read.
Latest from Today's Medical Developments
- Humanoid robots to become the next US-China battleground
- Air Turbine Technology’s Air Turbine Spindles 601 Series
- Copper nanoparticles could reduce infection risk of implanted medical device
- Renishaw's TEMPUS technology, RenAM 500 metal AM system
- #52 - Manufacturing Matters - Fall 2024 Aerospace Industry Outlook with Richard Aboulafia
- Tariffs threaten small business growth, increase costs across industries
- Feed your brain on your lunch break at our upcoming Lunch + Learn!
- Robotics action plan for Europe