
Nearly all medical devices require cleaning during manufacturing to remove particulate, oils, or inorganic contamination resulting from manufacturing processes. The challenge is finding a cleaning process that can handle complex assemblies, intricate shapes, and delicate parts.
Vapor degreasing had been the cleaning method of choice because solvent-based cleaners were effective and easy to use, consistently achieving the high levels of cleanliness required. This changed about 20 years ago when solvents raised environmental concerns. Device manufacturers were forced to switch to water-based cleaning systems and many vapor degreasers were tossed into dumpsters simply from a lack of cleaning solvents.
Today, many new solvent options are available, and they are highly effective, safe, environmentally friendly, and affordable. In response, medical device manufacturers are once again realizing that vapor degreasing is becoming an effective method for critical cleaning.
Solvent technology advancements are leading to environmentally acceptable cleaning options that greatly minimize bioburden issues. Many manufacturers and engineers are discovering that a properly designed and maintained vapor degreaser can be more environmentally friendly than an aqueous system, offering effective cleaning with a lower cost.
Bioburden risk
Medical device components are getting smaller, and more capable, more complex, and more precise – increasing the challenges of cleaning them enough to satisfy regulatory requirements. A well-engineered process is easy to validate and will reduce costs associated with medical device sterilization by removing bioburden sources from the manufacturing process.
Many factors can cause bioburden in a manufacturing process, but one of the biggest is cleaning with water. Water is the primary growth medium for bacteria. This is one of the main reasons solvents are becoming the preferred choice for cleaning. They are hostile to pyrogens, which simplifies process control requirements for eliminating bioburden.
A solvent-based cleaning process with submicron filtration can run at high production volumes while significantly reducing bioburden. Other benefits include lower energy consumption, a smaller footprint on the cleanroom floor, and lower up-front-cost than water systems.
Vapor degreasing uses low-boiling synthetic chemistries, usually halogens such as the fluorine found in toothpaste, the chlorine found in bleach, and iodine. Typically, these chemistries have high density, low surface tension, and low viscosity compared to water. These factors contribute to the desired cleanliness achieved by vapor degreasing systems.
Other benefits include:
Fast drying – Solvents are very pure, leaving no moisture or residue on parts after exiting the vapor degreaser
Immiscible with water –Solvents won’t mix, so water floats off the surface
Constant recycling – Cleaning fluids are usable hundreds or thousands of times as the solvent never wears out, eliminating expensive surfactants and saponifiers that are never recycled in aqueous systems
With aqueous systems, relatively complex processes must be established to ensure the cleaning water does not harbor bioburden, requiring water-cleaning machines that can be huge – sometimes 15m or 20m in length. The rinsing and drying processes are also complex because a great deal of energy is needed to heat and then evaporate water. Blowers or heated dryers are often used to reach all crevices, and even then, spotting or corrosion of parts can be a problem.
A general rule in cleaning is that you cannot clean if you cannot wet, as better wetting means better cleaning. The relative ability of a fluid to wet a surface can be measured by a composite, scaleless value – the wetting index. The wetting index combines the relevant chemical characteristics to predict the quality of cleaning. The wetting index of water is 14 while the wetting index of modern, non-flammable solvents is 100 or higher (see Figure 1 above).
Aqueous systems’ molecular characteristics significantly increase process validation and process control costs. Air knives and heating systems are also large users of energy and expensive to operate. These characteristics are inherent to water – no amount of pumping, heating, filtration, and treatment is going to prevent water from becoming a growth medium for bacteria.
Even trace amounts of moisture can allow the growth of bacteria and create related bioburden issues, compromising the ability to properly sterilize the device. The liability risks alone justify the expense of investigating vapor degreasing.
Ins and outs

Vapor degreasers come in many sizes and shapes, from benchtop units to those requiring two trucks to move and a third truck for solvent. Systems usually consist of a top-loading machine composed of two chambers, both filled with the non-flammable solvent. It’s a closed-loop system, has few moving parts, and ensures that the solvent is reliably clean for ongoing cleaning needs. Figure 2 (page 26) highlights the basic design of a traditional vapor degreaser.
Cleaning fluid is heated to a boil in the first chamber or sump, which then generates a vapor cloud that rises to meet two sets of cooling coils condensing the vapor back to liquid state. This liquid is then channeled back to the second (rinse) chamber until it is full, then the fluid flows back into the sump.
A basket containing dirty parts is lowered through the vapors into the boil sump where the primary cleaning occurs. Then the basket is lifted into the rinse sump, which always contains clean, distilled solvent that has been condensed from the vapors, providing a final cleaning to the components. The parts then are slowly removed from the machine and on to the next process. Normal cleaning cycles are 8 to 15 minutes per batch, faster than aqueous cleaning systems. The parts come out clean, dry, and immediately ready for packaging or further processing.
Options to enhance cleaning:
- Ultrasonics to further ensure residue-free, clean parts
- Superheat to reduce solvent losses
- Programmable computer controls for process control, repeatability
- Automatic hoists to free up workers, reduce solvent losses
Greener cleaner

It would be perfectly understandable to assume aqueous cleaning would be the environmentally preferred method of cleaning. However, aqueous cleaning systems generate a waste-water stream that requires treatment before discharge. Many aqueous detergents contain non-biodegradable ingredients, making discharge to sewer systems or surface waters problematic. Cleaners that are biodegradable when new may become contaminated during use; the systems recycle the water but not the detergents.
In aqueous systems, water always needs to be pre-cleaned to ensure there are no trace materials, minerals, or pre-existing bioburden that would compromise its effectiveness. In contrast, solvents come ready-to-use and require no mixing.
Waste water treatment is energy-intensive, and having a large machine emitting large quantities of warm water into the atmosphere of a plant also burdens a facility’s air conditioning system. The energy required to operate a vapor degreasing system is far lower than that required for an aqueous system.
Today’s solvents are much improved compared to products used 20 years ago. New products must meet strict environmental standards and regulations. Those containing environmentally unfriendly chemicals including HCFC-225, nPB, and TCE have been or are being phased-out and cleaning methods are migrating to newer, better, safer alternatives. The solvents available today are not only gentle on the planet but also deliver consistent and reliable cleaning with low overall costs.

A clean choice

As medical devices are evolving into more compact and complex components, cleaning becomes more difficult. Perfecting and validating a cleaning method that works effectively is vital to ensure patient safety. Vapor degreasers are smaller than aqueous systems but have equivalent throughput, are simpler to use, and less expensive to operate.
MicroCare Corp.
www.microcare.com
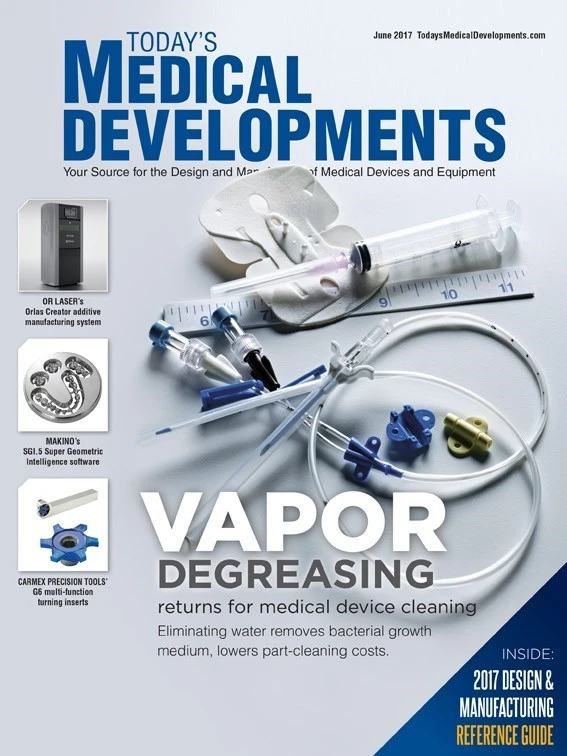
Explore the June 2017 Issue
Check out more from this issue and find your next story to read.
Latest from Today's Medical Developments
- The manufacturing resurgence is here – are you ready?
- Workholding solutions for your business
- ZOLLER events will showcase the company’s cutting-edge innovations
- THINBIT’s MINI GROOVE ‘N TURN Acme threading inserts
- CMMC Roll Out: When Do I Need to Comply? webinar
- Metabolic research uses Siemens gas analyzers to deliver results with 99.9999% resolutions
- Mazak’s SYNCREX 38/9 Swiss-type production turning machine
- Current economic and geopolitical realities demand decisive action