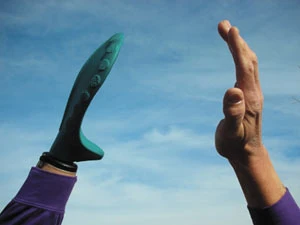
While some companies focus on aesthetically-pleasing prosthetics, TRS Inc. delivers recreational prosthetics that - in some cases - look more like sporting equipment than an actual limb.
Bob Radocy lost his arm 4" below the elbow in 1971. So, who better to design and produce upper limb prosthetics than an individual who knows exactly what others are looking for in a prosthetic - form, fit, function and, most importantly, freedom to return to everyday life.
After more than five years of trying the range of prosthetics available on the market, he was never completely satisfied and felt none met his desire to remain active in sports - and just everyday activities.
"The hook-type technology I had been exposed to, and had used for more than five years, I literally felt it was holding me back," explains Bob Radocy, TRS Inc. president and CEO.
"That led me on my own personal project to research prosthetics, review ideas that had been patented, develop my own personal criteria, put some designs down on paper, find a local machine shop, and go out and have my own device built." In 1979 he formed TRS with an instructor from the University of Colorado and in 1980 they began manufacturing one-style of an upper limb terminal device. "At first we had just a single, all-metal, prehensile device we called the Prehensile Hand, which has ultimately evolved into our GRIP prehensor technology over the last 30 years," Radocy explains. "After three years, we developed the first pediatric version of our technology - something that previously had not existed for children.
We still primarily focus on upper limb prosthetics, though we do offer Little Feet - pediatric infant foot prosthetics - and the Eldorado Z-Axis highperformance climbing foot."
FUNCTIONAL USE
While many prosthetic professionals strive for the latest technologies, the most aesthetically-pleasing and anatomically- correct limbs, Radocy and his partners took the functional route. "We do produce some cosmetically-, anatomically- correct biomechanical hands, which are unique and have been accepted, but we are more interested in providing something that delivers function and performance," Radocy states.
The devices that TRS has developed are activity-specific for a range of recreational arenas - they are designed to really target function and performance in order to provide amputees competitive two-handed capability in whatever recreation they choose. TRS prosthetics are available for golfing, hockey, basketball, baseball, swimming, and more.


But, it does not stop at just sports being considered recreation, as there are prosthetics for use when playing the guitar, the drums and even the violin.
"Our goal has been in trying to make people bi-manually functional and competitive, as opposed to just being 'participants' in recreations," Radocy explains. "These prosthetics are not high-tech, electronically-controlled, motion-controlled prosthetics but rather high-tech, body-powered prosthetics that functionally complement the other hand." Enabling this body-powered functionality is the voluntary closing design, which allows for energy transfer to the prostheses without any external power supply. As Radocy explains, it is similar to how a hand-brake functions on a bicycle. Based on TRS's ADEPT System (Anatomically Designed Engineered Polymer Technology), the user creates energy with their body, consciously, and by manipulation of the arm and torso, that energy allows the user to basically squeeze and close the prosthesis, just like when you pull on the brake lever of a bicycle.
ADEPT is a combination of synthetic materials with internal structural components that emulate the function of the hand with voluntary closing body power. Because of this body power, and the omission of motors, the user "feels" how much pressure is being applied - not feeling it as a finger-tip touch, but rather they pick up a resistance in their harness and cable system and in the pressure against their arm, where the socket interfaces with the skin.
Adding to this functionality is the newest development, the Sure-Lok, which enables prosthetic users to "lock" onto an object with their prehensor or biomechanical hand and then relax, while still holding on. The manner in which Sure-Lok works is similar to a rope cam-cleat system on a sailboat.
"A person pulling closed around an object merely flips a small switch on the side of their prosthesis and this enables the cable to be engaged and the gripping pressure adjusted, while the user is able to relax their body-power since the prosthesis is locked and holding the object," Radocy explains.
Taking this one step further, Radocy noted that while this primary Sure-Lok system is currently available, TRS is already moving forward with a hybrid version of the Sure-Lok; one that will be electronically-triggered by the users muscles.
MATERIALS, DESIGN
TRS prosthetics are designed using a broad range of materials - from basic metals like titanium and surgical grade stainless steels to high-strength aircraft aluminum. Polyurethane is a key material used in the body and matrix of the prosthetics - where the polyurethane is injection molded over a structural core or in some designs, molded to replicate human joint-like elements and characteristics.
"We began experimenting with polyurethanes in the early 1980s and found that they had an excellent application to prosthetics because they offer tremendous strength and flexibility and have excellent chemical resistance and resistance to environmental factors. They resist hysteresis - the breakdown of the molecular level inflections - and this is what allowed us to design products that had never before been conceived," Radocy explains.
"Everything in prosthetics - as far as prosthetic joints go - were purely mechanical. Mechanics allowed for rotation or angulations, but what we found, while exploring polyurethanes, is that we could replicate some of the functions that exist in the human body, for example the wrist, in an 'energystoring' joint." Energy-storing with prosthetics means that the energy created externally from the prosthesis, such as from your torso, is transferred to the prosthetic and released at the right time. An example Radocy gives is with the swing of a baseball bat. When you swing the bat back, energy is created from your torso and actually is captured in the polyurethane. So, when you swing the bat forward, instead of just transferring energy through the joint, power is coming through the torso, then through the polyurethane prosthetic device engaging the bat and then is released to hit the baseball.
It is with these materials and TRS' designs that Radocy feels confident to say that the longevity of their prostheses is years and years. There is certain minimal maintenance required, but TRS designs their prosthetics to pretty much be a "tool" to last a life time. "I do not want to have a 'tool' at the end of my arm that is going to fail, so if I am out on a five-day hike or climbing rocks, I do not want to have to worry about failure," Radocy says. "Being a user of our technology enables me to help design products for high functionality and good longevity. If you buy something from TRS, expect to get years and years of life out of it. That is just my personal perspective, being the designer and a user, but that is the way it should be."

Explore the May 2009 Issue
Check out more from this issue and find your next story to read.
Latest from Today's Medical Developments
- Methods Machine Tools, Multiaxis, announce AI solution investment
- MGS to showcase global expansion and healthcare CDMO expertise
- Medtronic: 5 healthcare tech trends for 2025
- Norman Noble launches enhanced laser welding capabilities; expands micromachining in Florida
- What you need to know about CMMC requirements
- CO2 footprint of a machine tool
- Ainos unveils AI Nose for robotics
- Keep up with the latest in design and manufacturing through free webinar