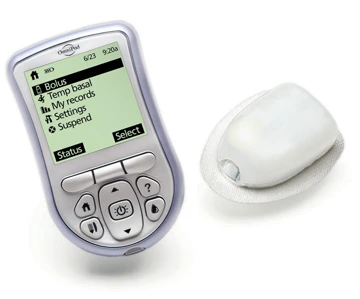
The treatment of diabetes has advanced so much in recent years that it's making the process of controlling the disease a much more refined battle. What used to be three, five, seven, or more insulin injections per-day is changing with the help of a less-invasive, easy-to-use insulin delivery system, the Insulet OmniPod Insulin Management System - a collaboration between Insulet Corporation and Phillips Plastics Corporation.
By working together to make the process of controlling diabetes less invasive and easier to manage, Insulet Corporation is partnering with Phillips Plastics Corporation to manufacture the OmniPod Insulin Management System -- a system with only two components:
- The OmniPod, a small, lightweight device worn on the skin like an infusion set. The OmniPod delivers insulin according to pre-programmed instructions transmitted wirelessly from the Personal Diabetes Manager.
- Personal Diabetes Manager (PDM) is a wireless, handheld device used to program the OmniPod with custom insulin delivery instructions, monitor the operation of the OmniPod, and check blood glucose levels using blood glucose test strips.
This innovative system eliminates the need for daily insulin injections, via a needle or syringe, and does not require the patient to be tethered to a conventional insulin pump via tubing. It makes intensive insulin therapy easier to prescribe, teach and learn. In addition, the integration of the blood glucose monitor into the PDM enables the patient to check blood glucose levels with test strips, but without the need to carry a separate blood glucose meter.
Having come to Phillips with a design for the system, Insulet chose the Company to do rapid models, rapid prototyping, prototyping, and production of the components. According to Insulet's Vice President of Manufacturing, Kevin Schmid, "I had prior experience with Phillips and they are a first class supplier. Philips was engaged early in the product design process, ensuring we would achieve the most effective component and system design with respect to design for manufacturability and assembly (DFM/DFA), process control, and component cost. Phillips is a onestop- shop and the Company's diversified capabilities were a huge benefit to us."
Phillips was able to provide a variety of solutions for the complex requirements of the device -- multishot molded housings to provide a watertight seal; micro molded internal components for precise geometry and to reduce overall size of the device, plateable grade materials, insert molding, and pad printed windows, just to name a few. According to a Phillips engineer, "This program is a well-rounded example of our offerings, but our experience working with thousands of medical programs in the past has also allowed us to flex our engineering muscles with anything that may have presented itself."
Another Phillips team member adds, "We have been able to utilize a variety of our capabilities on this program. The term one-stopshopping really is emphasized for this program. We offered everything from a variety of prototyping options to our focused factories including medical molding, clean room, micro molding, painting, window decoration and assembly. Rather than Insulet having to go to a handful of molders to complete all of these requirements, they came here and we did it all for them."
One of the main internal components of the OmniPod, the chassis, is a critical feature that holds many of the smaller internal components together. So to ensure the part held up to its promise of containing the smaller parts and providing a plateable electrical pathway for the circuit board, Insulet and Phillips worked together to create a solution.
This solution turned out to be a multi-shot part, with a first shot of polycarbonate and a second shot of plateable PC/ABS. "We realized right away that the geometry was complicated as we knew we had to create 12 separate areas of plateable material to provide 12 separate electrical pathways for the circuit board," explains a Phillips project engineer. "The challenge was figuring out how to gate and fill the part, because normally, everything would be connected and would fill at one time. In this situation, we have twelve separate areas that could not be connected."
OmniPod's small, lightweight design, integrated automated inserter, and lack of tubing, allow the user to wear the pod in a broad range of infusion sites, comfortably and discreetly beneath clothing. An adhesive, similar to the adhesive used on popular insulin infusion sets, holds the OmniPod securely against the skin.
With the press of a single button, the PDM wirelessly activates OmniPod's automated cannula insertion system, which safely and consistently inserts the cannula beneath the user's skin. Once the cannula is inserted insulin enters the body according to the pre-programmed basal rate the PDM has wirelessly transmitted to the OmniPod.
After the OmniPod is set up, the patient uses the PDM to check blood glucose levels, give bolus dosages, and adjust basal rates. The OmniPod is designed to be worn for up to three days.
To carry out the task, Phillips' team got to work devising a process to mold the part. "We mold the first shot. Then for the second shot we use a three-plate mold where we drop into a runner and it splits off and has fifteen drops come down and hit the twelve areas on the part to fill. We did numerous MoldFlow analyses because we knew each of the twelve areas is a different volume and some we had to gate with two gates, and some one gate and we had to balance the runner system to get everything to fill uniformly. Critical shutoffs were also important because we couldn't have any flash of the plateable material because of the electrical current," explains the team members. "Bondability to the first shot was a concern due to the size of the 12 small areas. In the end, all twelve islands fill fairly close to the same time, the runner splits into fifteen drops, these drops feed the part geometry, we open up the mold and it's done."
With an approaching launch, it was essential Insulet got the parts they needed, when they needed them. According to Phillips, being able to get the initial samples to Insulet very quickly was paramount. We'd sample the parts, get them to Insulet, they'd test for functionality, and come back to us with any changes they had. From day one, it's been an ongoing, team effort. TMD

Explore the June 2006 Issue
Check out more from this issue and find your next story to read.
Latest from Today's Medical Developments
- Birk Manufacturing achieves ISO 13485 recertification
- SW North America's BA 322i twin-spindle CNC
- The role of robotics in precision medical device manufacturing
- Swiss Steel Group’s UGIMA-X machinable stainless-steel sets
- #51 - Manufacturing Matters - The Impact of M&A in MedTech 2024
- Visual Components: 25 years of simulation and programming software innovation
- Zimmer Biomet announces definitive agreement to Acquire Paragon 28
- Discover an innovative technology for EMI/ESD/TVS suppression