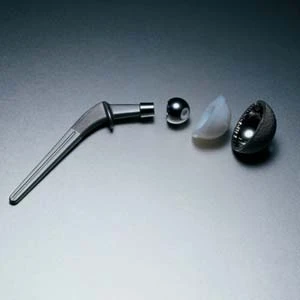
Within the medical machining and technology sectors, new developments are being made to improve the quality, reliability, functionality, and design of medical implants. One of the prominent examples of this increased investment into medical implants is in the machining and implementation of ball and socket joints, specifically for hip replacement. With nearly one million individuals a year replacing malfunctioning hip joints, the market for machined implants is steadily increasing. The technical aspects behind the workings of a naturally occurring hip joint consist primarily of the movement of a ball and socket. The joint links the top of the ball-shaped thigh bone with the cup-socket of the pelvic bone. A hip replacement entails surgical implants to replace any damaged bone of the hip joint, and the procedure consists of three basic parts; ? A new cup is added to replace the hip socket. Lately, these machined cups are being produced from super-alloys in order to ensure lasting life. ? A metal or ceramic ball is introduced to replace the top of the thigh bone. ? A metal stem is attached to the bone to add stability. This newly machined socket is implanted into the patient and the metal stem is inserted into the thigh bone. These artificial components are fixed in place and muscles and tendons are surgically replaced against the pelvic and thigh bones. With so many hip joint replacements being performed, the medical manufacturing industry for these parts is expanding and looking for competitive means to manufacture components. As with other areas of manufacturing, advances made in other fields, such as aerospace and power generation, can sometimes be introduced and used in different ways. Fortunately, this holds true in the development of ball and socket joints. Implants produced today are usually made of durable materials, such as cobalt or titanium based alloys. The fact that these same materials are used in the aerospace machining industry is no accident. These metals are designed to stand up to extreme conditions in both medical and aerospace applications. To make matters difficult, these highly advanced materials are also some of the toughest to machine. Cobaltchromium alloys are highly wear and corrosion resistant, and suitable for castings, forgings, or bar stock. The alloys are relatively hard and mechanically strong, resulting in short tool life if tools and methods are not adapted to these specific conditions. For example, if the approach of the cutting edge of the tool is incorrect, the result is rapid tool wear, typically in the form of mechanical notch wear, concentrated on where the edge meets the material at the depth of the cut. Titanium machining of parts is somewhat easier if the correct requirements are met. The chip being machined contacts a relatively small area on the tool face, resulting in high loads. Titanium also has strong chemical reactivity with tool materials at high machining temperatures, which can promote rapid tool wear. Poor thermal conductivity is another property which produces high heat concentration on the tool. It is important to understand that above all, the right tool material, tool path, and cutting data are vital to success in this type of machining. Sandvik Coromant has recently taken a new approach in attempting to provide an effective means for machining hip joint components, based partially on experience from solutions involving roundinsert technology. Hip joint cups vary in radius however, leading to different solutions for insert shape and geometry for roughing, semifinishing, and finishing operations. Where the radius of the hip-joint cup is restricted, the round insert solution may be limited to roughing insert providing the right nose radius. In addition, there may be different solutions for machining hip-joint heads depending on if forged or bar stock material is used. There are benefits in using the round-insert technology. With a radius representing the approach of the round insert to the material, the chip thickness is reduced in relation to the feed rate (compare this to a straight, perpendicular cutting edge, where the chip thickness equals the feed value). As a result, the round cutting edge engagement is longer, leading to lower machining temperatures. This provides a scope for higher cutting data, leading to higher productivity and a more reliable tool life. The development of insert- geometry and-grades as well as the development of machining solutions for aerospace materials has contributed greatly to advancements in medical applications. Both coated and uncoated cemented carbide grades are suitable for medical implants, depending on operational requirements. Recent developments have incorporated the use of such grades as GC1105, a unique PVDcoated grade, where the coating has very strong adhesion to the insert substrate. This property has proved beneficial for the sharp but positive cutting geometries needed for demanding alloys. Correct cutting data, including cutting speeds, temperature, feed rates, and wear must all be looked at to develop a successful application. Sandvik Coromant Company Fair Lawn, NJ coromant.sandvik.com/us

Explore the September October 2006 Issue
Check out more from this issue and find your next story to read.
Latest from Today's Medical Developments
- HERMES AWARD 2025 – Jury nominates three tech innovations
- Vision Engineering’s EVO Cam HALO
- How to Reduce First Article Inspection Creation Time by 70% to 90% with DISCUS Software
- FANUC America launches new robot tutorial website for all
- Murata Machinery USA’s MT1065EX twin-spindle, CNC turning center
- #40 - Lunch & Learn with Fagor Automation
- Kistler offers service for piezoelectric force sensors and measuring chains
- Creaform’s Pro version of Scan-to-CAD Application Module