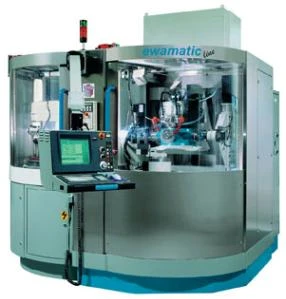
More often than not, shops manufacture complex tools, screws, inserts, and other medical/dental parts in two or more stages using processes such as EDM followed by finish grinding. However, with such conventional methods, tolerances can degrade as a result of multiple chucking from one machine to another. This is why the sixaxis CNC Ewag ewamatic line toolgrinding center's line approach combines both spark erosion and grinding in one machine for eliminating multiple part setups.
The ewamatic line accurately grinds complex tools like step reamers, drills, and milling cutters as well as circular and angular PCD and PCBN indexable inserts for medicalparts manufacturing. It also handles convex radii and tangents with equal or unequal clearance angles.
For versatility, the machine's starshaped turret grinding head features up to six independent spindles for rotary applications from 0.1 to 35 mm in diameter. Changing one work head lets users grind peripheries, cutting angles, and edge chamfers. Or they can use spark erosion before finish grinding complex cylindrical and conical tools with straight and spiral teeth made of tungsten and other tough materials.
The ewamatic line readily accepts automation. As a fully automated cell, it includes loading/ unloading by a Scara fouraxis robot, part sorting, multiple pallets and pallet stacking functions, and an ultrasonic cleaning station.
An automatic, swiveling, 3D measuring probe inspects tool cutting edges to be ground and transmits compensation data relative to infeed rates. This measuring cycle repeats several times during grinding (depending on the workpiece) and follows a measuregrindmeasure principle until required tolerances are met.
A Num 1050 CNC on the ewamatic line speeds setups and changeovers, while Windowsbased NumrotoPlus software permits conversational or realtime programming of standard and special tools. An integrated datamanagement system stores grinding features, parameters, cycles, and routines and lets users simultaneously program different batches with differing geometries.
A standard simulation program displays grinding wheels during operation in relation to grinding paths. With this program, shops analyze and verify the process prior to actual grinding to ensure desired finish results.
Walter Grinders Inc.
Fredericksburg, Vir.
waltergrinders.com
Circle 53

Explore the May 2005 Issue
Check out more from this issue and find your next story to read.
Latest from Today's Medical Developments
- Tariffs threaten small business growth, increase costs across industries
- Feed your brain on your lunch break at our upcoming Lunch + Learn!
- Robotics action plan for Europe
- Maximize your First Article Inspection efficiency and accuracy
- UPM Additive rebrands to UPM Advanced
- Master Bond’s LED415DC90Med dual-curable adhesive
- Minalex celebrates 60 years of excellence in miniature aluminum extrusions
- Tormach’s Chip Conveyor Kit for the 1500MX CNC Mill