Q: What is laser sintering, and how does it differ from traditional manufacturing?
![]() |
A: The most important difference is in the unique parts laser sintering creates, which are completely free from the manufacturability constraints of conventional processes.
Imagine that you are reviewing a design for a titanium dental implant. You look at the 3D CAD model, wondering if there has been a mistake. The implant incorporates threading, but its surface also has precisely defined cavities, 2µ to 200µ in size, to promote osseointegration and accelerate bone healing after surgery. It is a marvelous idea, but is such a surface even possible; with normal manufacturing and finishing methods, the answer is no.
Yet, as a laser-sintering system is used, you watch as software divides the CAD model into thin cross-sections. The system lays down a single, uniform stratum of powder onto a build platform. The data then guides the laser across that layer, melting the powder in the shape of the first cross-section. The platform lowers a pre-set distance and repeats these steps, layer-by-layer, until the implant is completed.
Laser sintering is additive, which is its greatest advantage over subtractive methods like machining or grinding. No shape is too complex; designers can focus solely on functionality without any compromises for the fabrication process.Multiple designs, either customized or completely dissimilar, can grow in the same batch.
Q: Why are certain medical applications particularly suited to laser sintering?
![]() |
A: Many medical devices are an excellent fit for this manufacturing method, especially if they are low-volume, and if the company makes a variety of different products. Laser-sintering systems are flexible and can switch from design to design as needed, with next to no tooling, fixturing, or other expenses.
Laser sintering can also build complex geometries that conventional processes cannot. For example, a European Union-funded project called Custom-IMD is developing a PEEK plastic cranial implant. The new design incorporates a lattice structure that promotes improved bone growth and optimizes infiltration with a hydroxyapatite-filled, bio-absorbable polymer.
The ability to build parts with lattices and hollows also reduces weight in a way that is not available using other methods. You can laser-sinter a lighter hip stem by introducing hollows and cavities similar to those in human bones; the only way to mill a lighter one is to make it smaller.
Q: Are other businesses and technologies working in conjunction with laser sintering to create advanced applications?
A: For obvious reasons, EOS works closely with a wide range of 3D CAD software programs. Materialise Interactive Medical Imaging Control System (MIMICS), and similar tools, translate medical data such as CT and MRI scans from 2D DICOM files into the 3D STL files needed to guide laser sintering. In addition, we have several partnerships with software and hardware companies, as well. For instance, Within Technologies in the U.K. uses their powerful optimization software in conjunction with laser sintering to create strong, yet lightweight structures. Their software can also control the stiffness or flexibility of a design.
Finally, because these parts often have complicated shapes, we are exploring new finishing techniques both to clean them and, in some cases, to provide mirror-smooth surfaces, such as for trial plate implants, which require removal and therefore should not integrate with the patient's body. The Swiss company BESTinCLASS, and its U.S. counterpart MicroTek Finishing, are working on this with EOS.
Q: What are the materials available, and what are their useful characteristics?
A: Presently, for medical products, we offer two stainless steels, two cobalt chrome alloys, and a titanium Ti64 alloy. The most promising plastics for medical applications are our PA 2200/2201 polyamide and PEEK HP3. The stainless steels and the polyamide are appropriate for surgical instruments and other instrumentation. The cobalt chromes, titanium, and PEEK are very suitable for implants.
All of these materials are strong, corrosion resistant, sterilizable, and biocompatible – though biocompatible means many things depending on the end use of the device.
Q: What other medical applications would benefit from laser sintering?
A: Prostheses would be interesting, as would the clamps, screws, and other instrumentation that go with implant surgery. An extremely intriguing area would be durable medical equipment, the kind that provides greater quality of living for patients. Imagine the increased comfort levels possible with customized, patient-matched interfaces for these devices, ranging from cups with handles tailored to individual hands and crutch covers that match armpit and shoulder contours.
![]() |
Q: How will laser sintering transform the business of medical design and manufacturing?
A: The most important transformation will be the new advantages for the patient: reduced surgery and recovery times, less invasiveness, and an increased lifespan for implants. Hospitals will benefit as well from how cost-effective the shorter procedures and subsequent hospital stays are.
For the makers of medical products, one of the greatest changes with the new technology will be the end of the bidding war at the hospital. Right now, if Company A and Company B is making nearly identical knee implants, the only difference between their offerings is price. That sort of competition reduces profit margins, and there is no value added to the customer's final choice. In this environment, individualized laser-sintered implants would provide a competitive edge for manufacturers and a clear-cut preferred choice for hospitals, surgeons, and patients.
Q: What other medical applications for this technology do you see in the near future?
A: There are a number of possibilities, and at present, it is uncertain which company will release its product first. Because the validation path is so lengthy, most companies begin considering laser-sintering when they have a new design, rather than replacing a previously certified process and part – unless, of course, they can achieve manufacturing costs that are 20%, or more, lower than those for the already-approved device.
That said, this past year Morris Technologies Inc. announced that, in collaboration with Kapstone Medical, they are filing 510(k) pre-market notification with the FDA for the first DMLS-generated titanium implant. I believe that the first mass-customized laser-sintered implants will be on the market within the next few years – possibly as soon as next year. Some aspects of formal approval, particularly in the United States, will need to be adapted for mass customization. After all, you cannot re-initiate validation every time a prosthetic limb or a knee implant receives modification for best fitting to a new patient. Nevertheless, I suspect that the certification agencies, worldwide, will rapidly modify their specifications to accommodate patient-matched products. The demand will be great, and the benefits enormous.
EOS of North America Inc. Novi, MI
eos.info
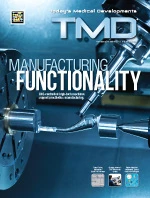
Explore the November December 2011 Issue
Check out more from this issue and find your next story to read.
Latest from Today's Medical Developments
- Betacom, Siemens launch 5G network platform to accelerate manufacturing innovation
- Starrett’s AVR400 CNC vision system
- US cutting tools orders decreased 2% from November 2024
- SMW Autoblok's Manual Jack connection kit
- MedTech Innovator welcomes five new industry partners
- First Article Inspection for quality control
- The manufacturing resurgence is here – are you ready?
- Workholding solutions for your business