With the emphasis on advanced process solutions and ever more demanding workpiece material, the mandated initiatives of lean, green, and blue, plus the perpetual search for increases in productivity and cost-effectiveness, have manufacturing companies scrambling for innovative process solutions.
Within manufacturing, chip making is subjected to scrutiny in cost, quality, and time, and parts are machined either dry, with water-soluble emulsion cutting oil, or with minimum volume lubrication (MVL).
When a study by Mercedes Benz, a few years back showed that 16% of their total production cost was directly related to coolant (just 2% for cutting tools by comparison), they began switching over to MVL or outright dry-machining.
![]() |
Another study by the University-Dortmund just recently brought to light that up to 60% of the total energy used for machining parts directly relates to traditional coolant usage.
The customary alternatives, dry and MVL, have significant, process-based shortcomings in that the former is limited relative to part material and application and very costly (tool life), while the latter is just for lubricating the cutting process with very limited cooling.
![]() |
Recently there have been stepped-up efforts to develop the use of nitrogen into a viable substitute. However, there are seemingly insurmountable obstacles, mostly due to the extreme cold operating temperature of -150°F, calling for special and costly spindle design, and making retrofitting existing machines uneconomical.
Today, crystal-based ChilAire technology, developed by Cool Clean Technologies, with support from the National Science Foundation (NSF) and the U.S. Department of Energy (DOE), looks to be the answer for clean, cool, productive, and cost-effective machining.
The patented working principle is as follows:
Internal Supply (through the spindle) – Refrigeration of compressed gaseous CO2 into the liquid phase
The chilled liquid travels through a capillary tube to the spindle, while compressed CO2 gas goes to the nozzle. The mixture travels through the spindle, out to the tip of the cutting tool and, as it exits into the atmosphere, the liquid expands into crystals for delivery to the cutting zone. (Note that the system can also deliver another medium like oil in a tri-axial delivery.)
External Supply – Refrigeration of compressed gaseous CO2 into the liquid phase
![]() |
The chilled liquid transports through a capillary tube to the nozzle where liquid CO2 and compressed air are mixed. The CO2 then expands into crystals that arrive at the cutting zone.
So, what really happens when CO2 hits the cutting edge? The ice-crystals melt and flash back to CO2 gas in a process called sublimation – a physical state conversion, capable of absorbing significant amounts of heat. This is equivalent to the simultaneous thawing and boiling of ice in warm water, generating steam from ice.
Operating between 400psi to 500psi, and a temperature of about 50°F in the spindle, the system installs easily in new machines and as retrofits within hours. If desired, the system can run alternatively to coolant by installing a T-connection above the spindle, where the unit's M-functions connect to the machine's control system.
What makes this crystal-technology so remarkable is that it thrives when applying it to difficult-to-machine material as well as regular material. The harder the part material, the better the outcome, most notably high-nickel high-temp alloys, steel, titanium, cobalt chrome, CGI, composites, stacked, Teflon, rubber, Inconel, etc.
The ChilAire system installations demonstrate its superior performance characteristics in terms of un-heard of tool life extension, up to a factor of three, and productivity increases up to 50%. It compares very favorably to dry, MVL, and water-soluble.
A bonus besides productivity increase and extended tool life is that there are always dry chips, no sticky oils, no fogged-up machine compartments, no air contaminations, and no health issues.
In addition, what one might not expect is that CO2 is part of the environmental solution. (See sidebar on page 16)
Now, Cool Clean does not claim that their innovative ChilAire technology is the cure for all machining. There are a few application limitations and they are relative to extreme high chip volume (medium operating pressure), deep hole drilling (access to the tool tip), large tooling with dozens of coolant ports (CO2 consumption), and soft material (low heat generation).
Besides that, this evolving technology makes inroads in the medical, aerospace, energy, and general machining industries, offering a fast return on investment.
CO2 – Technology is Part of the Solution Produced and captured as a by-product of natural and industrial processes, recycled CO2 is a valuable resource. By using this waste by-product, it turns into a net benefit in terms of energy conservation, pollution reduction, and societal applications. The EPA clearly states that users of recycled CO2 do not fall under the term of CO2 generators. One of the most important reasons for using recycled CO2, is that it replaces industrial processing agents such as water, solvents, lubricants, and coolants, in turn, eliminating their negative effects within manufacturing. Recycled CO2 conserves natural and human resources – water, oil, energy, time, capital, and labor. Producing, transporting, and consuming less processing agents eliminates production of associated environmental pollution and waste by-products, solid waste (e.g. filters, sludge), liquid waste (e.g. spent oils, wastewater), volatile organic compounds, and greenhouse gases. CO2 is an integral part of the basic life cycle. When breathing out, humans and animals give off CO2, which plants use for their growth, giving off oxygen, in turn, upon which we depend for survival. |
Dr. Bert P. Erdel;
bert.erdel@comcast.net
CoolClean;
http://www.coolclean.com
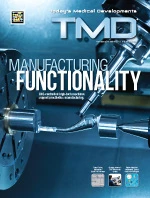
Explore the November December 2011 Issue
Check out more from this issue and find your next story to read.
Latest from Today's Medical Developments
- Zimmer Biomet to acquire Paragon 28
- Industrie 4.0 award for Paul Horn GmbH
- CMMC requirements and your business
- Stryker exiting spinal implant business
- Perfecting the manufacture of microscopically thin films for tech, medical applications
- Find out what 2025 holds for design and manufacturing
- Montagu to merge Tyber Medical, Intech and Resolve Surgical Technologies
- Americhem’s EcoLube MD PFAS-free internally lubricated compounds