![]() |
Billy Crump works as a programmer/machinist for Scinomix, a relatively small but rapidly growing high-tech manufacturing company. His work life is fast-paced. He divides his time between setting up and operating a Haas 3-axis vertical CNC mill, and programming a steady stream of prototype and production parts continually fed to him by the company's two founders and principal designers.
As such, he spends a lot of his time making design changes, which happen frequently, as the company specializes in prototyping. In the past, design changes occurred in SolidWorks, with reconciliation with the machine cutting programs created in Mastercam CAD/CAM software from CNC Software Inc., Tolland, CT. This was costing at least one day per workweek, and slowing the company's productivity. Scinomix solved the problem by giving their programmer/machinist a seat of a single product called Mastercam for SolidWorks, which integrates both programs in one seamless environment.
So Much Happening
Scinomix, located just west of St. Louis, MO, designs, develops, and manufactures flexible, modular automation and product solutions for laboratory research and drug discovery in the pharmaceutical, agrochemical, and healthcare industries. Founded in 2001 by two pharmaceutical industry veterans, Scinomix has grown steadily due to the company's commitment to quality, reliability, and customer service.
Scinomix is currently developing its own product line of fully automated systems, which integrate many of its own products with other manufacturers' instrumentation, to provide complete solutions for its customers. However, the industries Scinomix serves are very proprietary and competitive, so many of the products the company manufactures are custom one-of-a kinds.
Powerful, Automated 2D Machining
3D Roughing, Finishing, and Cleanup Machining
|
"This is such an exciting place to work," Crump says. "There is so much going on. Both of the owners are designers, and they continually send me new designs and redesigns of parts for custom orders or our own line of equipment. I was seeing a steady flow of SolidWorks files, which I would quickly import into Mastercam as parasolid files for programming."
Crump had only about four months of experience programming with different CAM programming software when he came to Scinomix several years ago. At that time, he was in charge of programming and operating a Haas 3-axis vertical milling machine. With some short training sessions from the Mastercam Reseller, QTE Manufacturing Solutions, Charles, MO, Crump was able to get a quick grip on the basic skills he needed for programming the Haas. QTE also rewrote the post-processor to make it perform exactly the way Scinomix wanted it to, and was always available to answer Crump's questions when he had to master new skills.
With that assistance, Crump was able to keep up with his workload. After a couple years, however, frequent design changes were becoming burdensome. During the early stages of the development process, some aspect of the part design could change four, five, or even six times. Every time that occurred, Crump would either import the changed parasolids file and reprogram the part entirely, or redraw the changed geometry in Mastercam and then regenerate those portions of the toolpaths. In either case, it would cost him a couple hours of programming time.
Cleaning Dirty Operations
Based on information they received from QTE, the owners learned of a new Mastercam programming module that resided within SolidWorks itself – Mastercam for SolidWorks. Users can create CAM programs directly in the SolidWorks environment, using toolpaths and machining strategies developed and continuously refined by Mastercam. QTE confirmed that this would eliminate many of the steps that Crump was dealing with to regenerate CAM programs after design changes. Therefore, Scinomix purchased a seat.
It was easy for Crump to get used to generating Mastercam programs inside of SolidWorks. The new module has the same look and feel, and the same Mastercam machining tree, which delivers quick access to any point in the machining process. Mastercam for SolidWorks also incorporates the same machining strategies that were available to Crump in the stand-alone program, including high speed machining (HSM) along with a powerful set of automated, feature-based toolpaths that get parts off the machine faster, with little or no handwork.
"I do not know much about SolidWorks," Crump states. "At the moment, I know just enough to draw some basic geometry. I do everything else in Mastercam inside of SolidWorks. I do not have to import parasolids files anymore. I program inside of SolidWorks and if anything in the design changes, Mastercam will flag these areas as dirty operations. To clean these up, I simply select the geometry and hit regenerate and Mastercam automatically regenerates the toolpaths. I still have to reselect a few things, like depth of cut, but there is very little additional work."
One prototype Crump manufactured recently went through five design changes. He said that regenerating the program in Mastercam for SolidWorks saved him at least half a day of additional programming. There are other ways that this integrated suite saves him time. For example, he can quickly determine if a dimension is critical by looking at the solid model and seeing how the part fits within the entire assembly.
"Now I can work seamlessly between the design and the toolpath within the same software program, which is very convenient," Crump says.
Of course, Crump is not a designer. However, the two partners will frequently ask Crump's opinion about how various geometries could change to make the part more manufacturable without having to sacrifice part performance. Facilitation of these discussions is because the designers and CAM programmer are working in the same integrated programming environment.
Crump estimates that the ability to automatically identify dirty operations and regenerate toolpaths, and the convenience of having the model close at hand for a fast check of dimensions or fit to assembly, has reduced the time he spends writing CAM programs by about 20%. That translates into getting more parts on the machine, and quickly into the mix for assembly.
Scinomix Inc. Earth City, MO
scinomix.com
CNC Software Inc./Mastercam Tolland, CT
mastercam.com
Haas Automation Inc. Oxnard, CA
haascnc.com
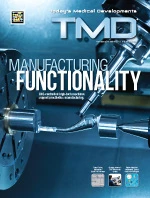
Explore the November December 2011 Issue
Check out more from this issue and find your next story to read.
Latest from Today's Medical Developments
- Betacom, Siemens launch 5G network platform to accelerate manufacturing innovation
- Starrett’s AVR400 CNC vision system
- US cutting tools orders decreased 2% from November 2024
- SMW Autoblok's Manual Jack connection kit
- MedTech Innovator welcomes five new industry partners
- First Article Inspection for quality control
- The manufacturing resurgence is here – are you ready?
- Workholding solutions for your business