When the team at Biomet Orthopedics’ facility in Valencia, Spain, was looking to improve the process of rough face-turning in a chromium cobalt prosthesis component, they found that switching to new ISO S geometries from Sandvik Coromant offered dramatic benefits. This included a 100% gain in tool life, far fewer machine stoppages, and greater machining security alongside significant annual savings in production time and costs.
Biomet is a global manufacturer of orthopedic joint replacement products for knees, hips, shoulders, elbows, and wrists among others. The organization employs around 6,700 people and has 16 manufacturing facilities worldwide. With annual sales exceeding $2 billion, the company estimates that its products help one surgeon provide personalized care to one patient around a million times a year.
The Challenge
Biomet’s implants are produced from hardwearing, corrosion-resistant materials such as CrCo (chromium cobalt). This material proves tough and abrasive when machining, and many manufacturers discover that cutting tools do not last long. Until now, Biomet was among this number, particularly for a rough face-turning operation on a prosthetic knee part – the company’s Regenerex Primary Tibial Tray.
One of the most critical components here is the tibial tray central axle, which in generic term consists of a kidney-shaped plate with central post that demands interrupted cuts when face turning. Using a Mazak Integrex multi-tasking machine, Biomet was only achieving five parts per edge (around 25 minutes total tool life) using a competitor’s insert. The component is cut at a speed of 40.0mpm (131.2fpm) with a feed of 0.080mm/rev. (0.003"/rev.), while depth of cut is 1.00mm (0.04"). Looking to improve the process and the performance of its inserts, the company turned to Sandvik Coromant for support.
After a full assessment of the cutting operation, its demands and the desired outcomes, the experience and expertise of Senior Turning Specialist, Jesús López, and Sales Engineer, Oscar Poveda, led to the recommendation of T-Max P inserts featuring ISO S geometries. These special geometries have been designed to operate with low tool pressure to help bring chip control in focus and meet calls from the medical industry for optimized performance, productivity, process security, and surface finish. Capable of performing operations ranging from roughing through to last-cut finishing, the ISO S geometries are adept at handling continuous and/or interrupted cuts.
Impressive Results
While there are four ISO S turning geometries available, the durability, sharp edge line, and chip control capabilities of the -SM geometry made it the first choice for Biomet’s application. The results were impressive. Using a DNMG (rhombic 55°) T-Max P insert based on Sandvik Coromant’s high-performance GC1105 grade, Biomet doubled the number of components per edge from 5 to 10, boosting total tool life to 50 minutes in the process – all without any changes to cutting data. For reference, the time in cut per component is around five minutes (two passes). Additionally, with machine stoppages halved, the company has improved process reliability and achieved greater production uptime – this is important as the company produces around 2,500 tibial tray central axles per year.
As well as attributing success at Biomet to the ISO S geometry, GC1105 plays a significant part. This grade’s PVD TiAlN coating is designed specifically for tough alloys for secure, reliable machining and flank wear.
Further Success
Biomet has now achieved additional gains on a titanium component called a cotyle, essentially a cup-shaped component with a central bore and four peripheral holes. Cotyles are often fitted at the base of the hipbone to accept the ball-shaped head of the femur. Making around 5,000 such parts a year on an Index G300 CNC turning center, Sandvik Coromant again ousted the same previous tooling supplier for this process, which majors on second-phase external roughing (interrupted cut).
A GC1105 grade insert with -SMR geometry helped Biomet increase the number of cotyles completed per edge from 10 to 18, while boosting tool life from 95 minutes to 171 minutes. For reference, cutting data includes cutting speed of 70mpm (230fpm), feed of 0.080mm/rev (0.003"/rev.) and 1.50mm (0.06") depth of cut. Time in cut is around 9.5 minutes (seven passes).
As a result of the trials using ISO S geometry at Biomet, the company has replaced its previous insert supplier with Sandvik Coromant for both applications. It follows previous success against the same competitor for another tibial tray component made from CrCo, where an SNMG (square) insert in the same grade with -SM geometry provided significant gains. In total, across all three applications, BIOMET required about 1,000 inserts a year from its previous supplier. Sandvik Coromant has captured this business, although Biomet obviously now requires far fewer inserts to complete the same number of components.
Designed for all tough alloy-turning applications, more than 300 T-Max P double-sided inserts are offered in the current Sandvik Coromant range, in six styles with nose radii from 0.400mm to 1.600mm (0.015" to 0.060"). As well as GC1105, other available grades include GC1115, GC1125, S05F, and H13A. While -SM geometry is the first choice for many common machining tasks in the superalloy area, and -SMR is preferred where high edge-line toughness is required, other geometries include -SF for chip breaking and -SGF for high precision.
Sandvik Coromant
Fair Lawn, N.J.
www.sandvik.coromant.com/us
About the author: Patrick Loughne (patrick.loughney@sandvik.com) works as a small part machining/turning specialist for Sandvik Coromant Co.
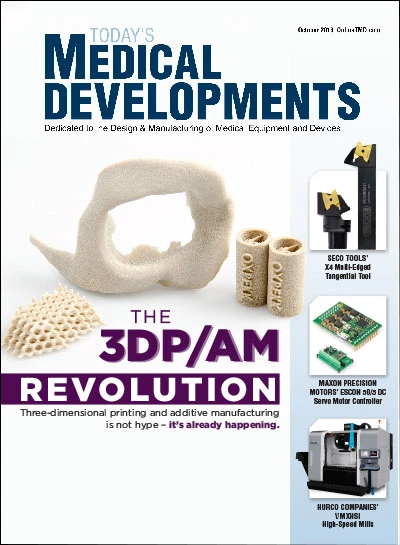
Explore the October 2013 Issue
Check out more from this issue and find your next story to read.
Latest from Today's Medical Developments
- The toolbelt generation
- Covestro's role in transforming cardiac care
- Practical and Affordable Factory Digital Twins for SMEs
- UCIMU: fourth quarter 2024 machine tool orders on the rise
- Thomson Industries’ enhanced configuration capabilities
- Frequently Asked Questions about AM Post Processing
- How new executive orders may affect US FDA medical device operations
- Midwest DISCOVER MORE WITH MAZAK