![]() Editor |
Three-dimensional printing – additive manufacturing – is starting to become the big buzzword not only the medical design and manufacturing sector, but also in everyday conversations. However, about 19 years ago it was very much not on my radar. From the time I entered this sector, my editorial responsibilities were always geared toward covering new technology, medical manufacturing, and software. So, in 1995, I headed off on my first business trip and it happened to be up in Minnesota to visit Stratasys. A group of editors was invited to learn about a new technology hitting the scene. I mean, there was all this 3D printing chatter going on, so of course I wanted to see it up close in order to understand how it was going to influence the industry. The printing technology sure wowed me then, but to where it has evolved in 2013 is enough to amaze anyone – even those not involved in the medical manufacturing sector. It all started as a technology that would allow design engineers to hold a prototype in their hands. They could see the intricate details they had designed, see what was working, where improvements could be made, and how it would affect the final product. Most important was that the cost to print an updated prototype, as design iterations came around, was minimal – and the ability to help improve a design before going into production was monumental in getting to market with just the right product. As we sit here in 2013, 3D printing is producing more than just prototypes. News stations across the world are broadcasting how this technology is being used in patients almost on a daily basis. Arcam’s 3D technology has enabled almost 30,000 hip implants to be manufactured and implanted in patients. 3D Systems offers technology that allows orthodontists to print Invisalign teeth straighteners. Then there’s the heartwarming story from May 2013, of the tracheal splint printed for the then-infant Kaiba Gionfriddo. Born with a condition that frequently collapsed his windpipe, doctors received special approval from the FDA to save this infant’s life by 3D printing a custom splint out of a material that would eventually dissolve safely into his body. These are just some of the examples of how 3D printing is speeding along in medical manufacturing. Work continues to make headlines on researchers printing body parts from biomaterials in order to reduce rejection rates. Adding importance to this market is the backing it’s getting from our government. The recently opened National Additive Manufacturing Innovation Institute (NAMII), headquartered in Youngstown, Ohio, is a public-private partnership with member organizations from industry, academia, government, and workforce development resources. NAMII – the pilot institute for up to 15 National Network for Manufacturing Innovation (NNMI) institutes across the country – is working to transition additive manufacturing technology to the mainstream U.S. manufacturing sector and yield significant advancements throughout industry. The latest report from Transparency Market Research predicts that the global medical applications market for 3D printing stands to reach $965.5 million by 2019, up from its 2012 value of $345.5 million. Numbers like those reaffirm 3D printing’s place as the wow technology that is here to stay. What do you think – is 3D printing a popular fad or does it have staying power? – Elizabeth |
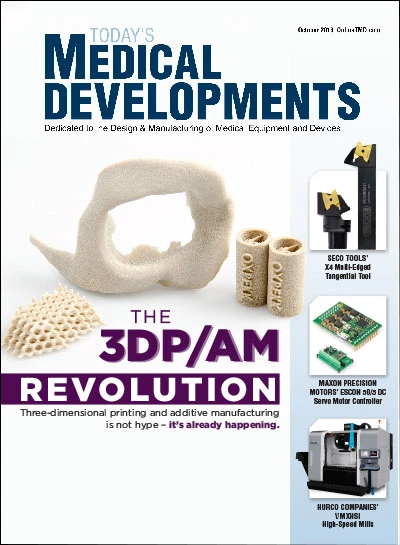
Explore the October 2013 Issue
Check out more from this issue and find your next story to read.
Latest from Today's Medical Developments
- The toolbelt generation
- Covestro's role in transforming cardiac care
- Practical and Affordable Factory Digital Twins for SMEs
- UCIMU: fourth quarter 2024 machine tool orders on the rise
- Thomson Industries’ enhanced configuration capabilities
- Frequently Asked Questions about AM Post Processing
- How new executive orders may affect US FDA medical device operations
- Midwest DISCOVER MORE WITH MAZAK