Progress is constant, and new technologies and product advances are arriving faster than ever in the medical devices industry. Paving the way for this innovation are lithium-ion batteries, a market that is projected to double in size within the next three years. Already used in more than 95% of mobile phones, their application in medical devices is surging as the medical world becomes more portable.
The interest in lithium-ion batteries for medical devices is attributed to the evolution of secondary (or rechargeable) technology. As a result, these batteries provide increasingly greater energy density, longer life cycle, improved reliability, and performance standards. When it comes to the medical industry, lithium-ion batteries are powering a range of diagnostic equipment, including patient monitors, handheld surgical tools, and portable diagnostic equipment.
Given the critical importance of lithium-ion batteries to medical devices, it is imperative to advance battery standards, maximizing safety as well as safeguarding the adoption of new applications and uses. While their rate of failure is small, there have been incidents that call attention to their potential risks. These concerns for safety must be addressed, and standards have been enacted to mandate a number of tests designed to assess specific safety risks associated with their use, thus ensuring minimal risk and maximum efficiency.
Implementation of Safety Standards
When it comes to product safety standards and testing protocols, these are developed through a consensus process, relying on collaboration from regulatory bodies, manufacturers, industry groups, consumer advocacy organizations, insurance companies, and other key safety stakeholders. The technical committees developing requirements for product safety standards rely less on prescriptive requirements and more on performance tests simulating reasonable situations that may cause a defective product to react.
For example, through our extensive research at UL, we identified an internal short circuit (ISC) as one of the root causes of failures, and developed a simple and repeatable way to induce these failures. The ISC testing enables us to study battery behaviors when an ISC occurs, making it possible to create more stringent safety standards that will be employed within enhanced and original medical devices. While knowledge about potential failure modes is still growing as the complex technology continues to evolve, UL is continuously working on developing new research to better understand standards development worldwide, participating in leadership and expert roles on several national committees and maintenance teams associated with lithium-ion battery technologies.
When the widespread commercial use of lithium-ion batteries began in the 1990s, designs were developed to meet an array of product demands. The choice of battery is normally driven by considerations such as application requirements for power and energy, the anticipated environment in which the battery-powered product will be used, and battery cost. Generally, lithium-ion batteries are more expensive than alternatives, but offer significant advantages including high energy, greater density levels, and low weight-to-volume ratios.
Challenges in performance and safety still exist for all batteries in various applications, including lithium-ion batteries used in medical devices. Manufacturers of batteries and battery-powered devices design products to deliver specified performance characteristics in a safe manner under anticipated usage conditions. This means failure can be caused by poor execution of a design, or an unanticipated use or abuse of a product. To avoid these failures, manufacturers should conduct a risk assessment as part of the product development process, involving tools such as failure modes and effects analysis (FMEA), and fault tree analysis (FTA).
The Aging Process
Lithium-ion batteries are also increasingly being expected to last for longer periods of time. Some lithium-ion cells used in large format applications such as electric vehicles (EVs) may be considered for reuse in energy storage applications since they often still have as much as 80% of their usable capacity left, and there are lithium ion battery applications that have an expected battery life of five to 20 years. These long-term usages are important to consider when developing safety requirements for these applications, because failures may be dependent on how the state of the lithium-ion cell changes over time. Current safety standards either do not address the potential impact of battery aging or do not go far enough in the aging process to understand the effects on safety for long-term usage.
A common belief is lithium-ion batteries become safer over time because aging tends to degrade performance, draining energy storage capacity as well as some of their efficiency in discharging energy. But another school of thought is the aging and degradation of these battery materials would give way to a higher risk of failure. Given the trend toward lithium-ion battery long-term usage and potential for reuse, the effects of aging needs to be studied to understand how it affects battery failure.
UL developed a first-stage research study to understand the potential role aging played in lithium-ion battery field failures. Our research identified two critical safety concerns: the polarization effect on aged batteries, and the lower thermal stability of active materials in aged batteries.
Polarization can be detected from temperature and cell voltage profiles during overcharging. With polarization, a higher voltage plateau can usually be observed under charging, while a lower voltage plateau can be observed under discharging. An increased thermal effect results from the increased cell impedance and the decay of charging and discharging efficiency. An increased thermal effect can lead to a greater risk of side chemical reactions that are unfavorable to the safety performance of a lithium-ion battery. A failure as a result of polarization may become the root cause that eventually leads to a catastrophic thermal runaway.
The effect of lower thermal stability of active materials in aged batteries was demonstrated when UL conducted a hotbox test on aged and fresh samples. Thermal runaway was triggered earlier in the aged samples when compared with the results of the test on fresh cells. In aged cells, internal protection mechanisms such as separator melting (affecting separator shutdown) and venting were delayed when compared with that of a fresh cell during the test. Research identified this as a critical safety concern, with data from a differential scanning calorimeter suggesting that heat-generating reactions within the cells occur earlier for an aged cell.
Research to assess the effects of aging on lithium-ion batteries is still in its early stages, and will need to move beyond the single chemistry studied so far into other common cell chemistries. Research also will be extended over more cycles and conducted on large-format lithium-ion batteries such as those in stationary energy storage applications. Discovering the full impact of aging on lithium-ion battery safety will allow independent standards organizations like UL to update safety standards and help ensure the safe use of lithium-ion batteries over time.
Innovation allows greater efficiency and productivity, but along with innovation comes risk. As the development and proliferation of lithium-ion batteries within the medical devices industry continues, the need for rigorous safety standards is greater than ever. UL is conducting research, developing new methodologies, and updating standards to help ensure the safety of lithium-ion batteries. Devices powered by lithium-ion batteries offer tremendous opportunities for the medical industry, and address the trend toward mobile healthcare. As manufacturers respond with new portable devices, there is a need to put safeguards in place that ensure they are reliable, particularly when human health and lives are at stake.
UL (Underwriters Laboratories)
South Bend, Ind.
www.ul.com
About the author: Since 2003, Laurie Florence has been the principal engineer at UL for batteries, among other areas. With more than 20 years of experience in testing and certification, she has responsibility for technical competency criteria for UL staff and supports UL certification programs. Florence also represents UL on many domestic and international technical committees and organizations. She can be reached at newscience@ul.com. For more information on UL research, go to www.UL.com/newscience.
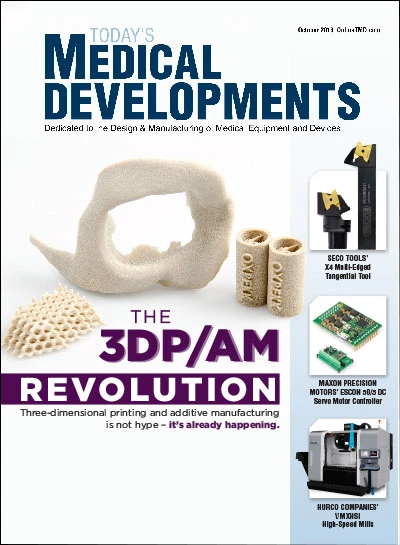
Explore the October 2013 Issue
Check out more from this issue and find your next story to read.
Latest from Today's Medical Developments
- The toolbelt generation
- Covestro's role in transforming cardiac care
- Practical and Affordable Factory Digital Twins for SMEs
- UCIMU: fourth quarter 2024 machine tool orders on the rise
- Thomson Industries’ enhanced configuration capabilities
- Frequently Asked Questions about AM Post Processing
- How new executive orders may affect US FDA medical device operations
- Midwest DISCOVER MORE WITH MAZAK