The emergence of 5-axis laser texturing made some people think that innovative technology would significantly reduce the use of, if not completely replace, the traditional process of photo-printed acid etching. However, at Custom Etch, that prediction could not be farther from the truth.
Custom Etch Inc., in New Castle, Pa., is a 30-person shop that specializes in photo-printed acid etching, and has done so since its establishment in 1982 by Henry Melonio and his brother Don Melonio. However, the shop recently invested in 5-axis laser-texturing technology, and instead of replacing the shop’s legacy processes, two laser systems have proven perfect partners to Custom Etch’s chemical etching and engraving operations.
As a result of marrying together the chemical and laser processes within its operations, Custom Etch engineers can generate virtually any desired surface pattern or texture faster than those shops relying solely on chemical processes, and do so more precisely and efficiently. Additionally, laser texturing significantly boosts Custom Etch’s flexibility when it comes to imparting complex organic textures and geometric patterns onto complicated mold cavities, cores, mandrels, embossing rolls, and profile embossing wheels. The shop’s textures and patterns can be found on everything from medical components, housewares, building products, and automotive parts to lawn and garden equipment, toys, and more.
“When coupled with our experience, efficiency and excellent customer service, 5-axis laser-texturing technology enables us to further help our customers discover and explore unique design opportunities,” says Don Melonio, vice president of Custom Etch. “The technology propels forward the development, prototyping, and manufacturing of our customers’ products. It also provides levels of accuracy, detail, and repeatability – especially helpful with mold repair areas – that are unachievable using conventional etching processes.”
Precision Machining
Custom Etch’s laser systems are GF AgieCharmilles LASER 1000 5Ax and LASER 1200 5Ax 5-axis laser-texturing machines that provide fully digitized manufacturing processes for generating detailed and nuanced texturing, microstructuring, engraving, marking, and labeling. The technology is faster and quieter as well as more repeatable, flexible, and environmentally friendly when compared with conventional processes, both mechanical and chemical.
Both LASER 5Ax systems machine from high-quality digital images and CAD data, allowing for completely reproducible results in both large and small job lot sizes. The mapping systems of the machines use a 50W Ytterbium pulsed laser to render the desired patterns or textures. Moreover, while chemical etching can only produce in three to five layers, GF AgieCharmilles’ laser-texturing technology can achieve 30 to 50 layers to provide much higher levels of detail.
The machines also come standard with programmable, tilting laser heads, high-resolution cameras with integrated illumination for fine positioning, integrated touch probes, dust exhausts, central lubrication systems, and lenses of varying focal strengths. In addition to being a faster and more precise means of producing patterns and textures with increased reliability, laser texturing offers pollutant-free operation, producing no fluids, slurry, or chips. Dust particles produced by the process are automatically extracted by vacuum to guarantee a clean process.
“The LASER machines are basically 5-axis milling machines with lasers instead of milling heads,” Don explains. “However, GF AgieCharmilles created a completely new proprietary software to run the laser heads from common IGES and STEP files. Programming is easy and basically requires only the same programming skills as would be needed to machine a simple component on a conventional CNC machine tool.”
Rhinoceros software, from Robert McNeel & Associates, is Custom Etch’s preferred mapping/imaging software used to create surface designs and transfer them to mold cavity surfaces for laser texturing. These same files are the ones used by the machinist that cut the tool cavity shape on milling machines.
According to Don, the key to the laser-texturing operation is positioning the laser’s focal point at the correct distance from the workpiece surface. The material laser-texturing rate is based on the frequency and power setting of the laser. Power settings can be adjusted anywhere from 0 to 100%, and the frequency from a level of 10 to 90, for instance, to determine how fast the laser will ablate/cut material.
Because they use fiber lasers, the systems are extremely precise and can remove microns at a time. This allows Custom Etch to make very light and shallow cuts or make no cuts at all, but instead use the lasers to change only the color of a part’s surface strictly for aesthetics if so desired.
With its most recently acquired LASER 1200 5Ax, Custom Etch increases the range of part sizes to which it can apply surface texturing. The machine’s table measures 31.5" in diameter and handles workpieces weighing up to 3,747 lb.
Custom Etch’s LASER 1000 5Ax is fully automated with an integrated GF AgieCharmilles pallet changing system that accommodates six modular pallets from System 3R. And, according to Don, automation is the one factor that definitely makes the technology economical for the shop and justifies the investment.
The pallet system uses six 11.02" square pallets that each hold workpiece fixtures an outside shop developed for Custom Etch. As opposed to vises, the adjustable fixtures allow Custom Etch to load and unload workpieces with little effort.
In operation, the laser machine runs an automatic probe cycle, and the part program is such that every part locates in the same place on the pallet, thanks to the custom fixtures. Removing parts is as simple as loosening a couple of screws, sliding the finished part out, and placing a new one into the fixture.
“For our type of work, it would be tough to make money with the laser machine if it didn’t have the pallet system. Without such automation, parts would have to be manually loaded one at time into the machine, which would add huge labor costs and time to the process,” Don explains. “Plus, once pallets are loaded, the system basically runs unattended.”
Increased Production
To illustrate the value of the pallet system, Don cites having to produce 40 molds – a job that entailed texturing 80 mold halves (cores and cavities) and 40 base pushups. For this particular job, the shop had to process all 80 halves and all 40 base pushups through the GF AgieCharmilles 5-axis laser-texturing machine in a matter of three days to make the required delivery time. Don says the only way the shop accomplished the task was being able to have only one person load and unload pallets while the machine continued to work non-stop and unattended.
Typical part sizes run on the LASER 1000 5Ax machine measure up to 8.5" x 10.63", so the shop uses every workable inch of its pallets. Approximately 200 molds per week are processed through the laser machine, and the system has increased the shop’s throughput month after month without the need to increase shop floor size or workforce dramatically.
However, it should be noted that Custom Etch uses its laser machines to impart complete surface textures only some of the time. Instead, Don explains, the lasers will most often be used first on a part, followed by the acid etching process. The reason, he says, is that imparting an 0.008"-deep pattern in a mold, for instance, would take about 1.5 hours per one mold-half using only laser texturing. Such a processing time is reasonable for one or two parts, but consider if the job required 60 molds with a total of 120 halves.
For its dual texturing technology processing, Custom Etch will apply an acid-resistant paint on to the mold cavity surfaces. It then laser textures the desired pattern onto the parts, but in such a way as to only remove the paint, not actual part material. The operation takes only minutes as opposed to hours, and basically serves the same purpose as the wax transfer does in traditional chemical etching.
“We’ve paired the two processes together – mapping the texture with the laser system, and then removing the material with the old acid process,” Don comments. “The combination allows us to cost effectively process our large volumes of parts, and as quickly as possible. It (the combination of technologies) also, like the pallet system, further increases the ROI of the laser technology as well.”
Additionally, Don says that the laser texturing systems actually helps improve the accuracy of the acid etching process.
“It also improves the repeatability,” he adds. “With the old pottery tissue method, acid etching a pattern on 40 different parts would result in many pattern variations from part to part. However, with the lasers used instead, the surface patterns will look exactly the same from the first mold to the 50th to the 100th; identical to the point that even if the mold is damaged, a weld spot could be applied and the GF AgieCharmilles 5-axis laser systems could impart the exact same pattern feature in the exact same place on the cavity.”
Don also explains that the decision to use chemical, laser, or both technologies is based on the requirements of the pattern design. The more intricate and complex a pattern, the better a candidate it is for 100% laser texturing.
In those rare occasions when Custom Etch doesn’t use the laser-texturing machines, it is usually because the job involves short programs and only a couple of mold components. The small volumes and simple patterns make such jobs more cost-effective to process the traditional way and, according to Don, do not justify tying up the laser systems.
Custom Etch’s business has grown about 40% during the past two years, and half of that can be attributed to the GF AgieCharmilles 5-axis laser-texturing machines – the high-end capability they provide together with the speed to process jobs faster working in tandem with traditional processes.
GF AgieCharmilles
Lincolnshire, Ill.
http://us.gfac.com
Custom Etch Inc.
New Castle, Pa.
http://custometch.com
Elizabeth Engler Modic can be reached at 330.523.5344 or emodic@gie.net.
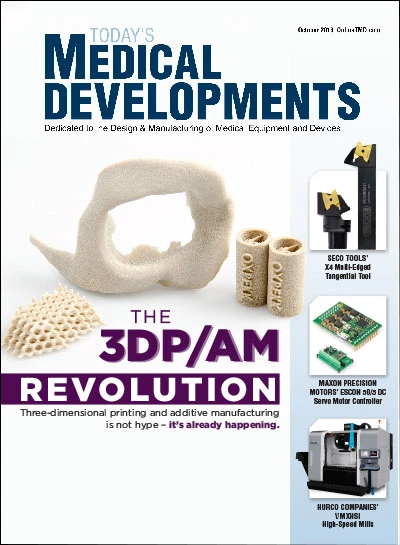
Explore the October 2013 Issue
Check out more from this issue and find your next story to read.
Latest from Today's Medical Developments
- The toolbelt generation
- Covestro's role in transforming cardiac care
- Practical and Affordable Factory Digital Twins for SMEs
- UCIMU: fourth quarter 2024 machine tool orders on the rise
- Thomson Industries’ enhanced configuration capabilities
- Frequently Asked Questions about AM Post Processing
- How new executive orders may affect US FDA medical device operations
- Midwest DISCOVER MORE WITH MAZAK