Three-dimensional printing and additive manufacturing (3DP/AM) is expanding the capabilities of the manufacturing process. It’s not just hype, either. The ability of 3DP/AM to customize and the freedom to create unique relatively cost-effective tradecraft has led to wide use in jet engine manufacturing, cranial and jaw implants, and even the preparation of food.
Standing at the forefront of this manufacturing movement is the medical sector. The same factors that drive innovation and demand in the medical arena – rapid response and personalization – are enabled by 3DP/AM.
3D printing grew out of the market need for rapid prototyping and gave designers and product development teams the ability to create with speed, specificity, integrity, and accuracy. The medical device market values these abilities, and as medicine continues to evolve into personalized solutions, 3DP/AM presents a customized robust product development process for devices.
The advances and benefits of 3DP/AM are dramatic and important to the medical industry. Like 3D imaging, the ability to print patient-specific biological and structural components in three dimensions enables new solutions and faster intervention and repair. However, 3DP/AM will not replace the time-tested methods of the last century nor the innovations of this one. Rather, capability, application, and access will be expanded in conjunction with these tools with a breadth and speed only restrained by imagination and the hours in the day.
3DP/AM is already making an impact on the customization of medicine – a viable route to personalized medical solutions feasible under both cost and scientific analyses. This article will explore where the leading edge casts its shadow now and the legal and regulatory issues demanding answers in the realm of intellectual property, risk assessment, and product liability. Companies that understand and prepare for the legal and regulatory scrutiny for their applications of 3DP/AM will see the scalpel and avoid the ax.
Customizing Technology
The technology’s spotlight has shined brightest on implants (See Today’s Medical Developments article from Aug. 14, 2013, http://bit.ly/1fgD6cs.) In the past year alone, successful cranial, jaw, tracheal, and hearing-aid implants have attracted significant public attention, translating the science-fiction nature of 3DP/AM to practical everyday life. At the same time, researchers around the world are regularly announcing tissues, organs, and surgical and teaching tools, as well as cardiovascular, orthopedic, prosthetic, and other devices generated by 3DP/AM.
Oxford Performance Materials (OPM) has used 3DP/AM to manufacture commercial and military aerospace parts as well as cranial implants for head trauma victims. That marriage of product lines would have been inconceivable for the South Windsor, Conn.-based company without the materials and 3DP capabilities it has developed throughout the past several years. A typical product demand for OPM starts when an automobile accident victim presents in an emergency room with a skull fracture. Doctors at the hospital email a 3D scan of the fracture to OPM, and engineers there use proprietary methods and processes to translate the 3D scan into a precisely sized 3D printed cranial implant made of PEKK (polyether ketone ketone) polymer material. Not only does this thermoplastic outperform metals such as stainless steel and titanium in many applications, but its biocompatibility, texture, and printed porosity generate a surface that allows effective osseointegration and cranial repair.
Another life-changing use of 3DP/AM is illustrated by the success of Robohand, an open-source tool that allows local production of custom prosthetics for individuals with missing digits. This tool fundamentally changes the cost and effort of obtaining a prosthetic, making it practical to replace the device as children grow, and creating opportunities to effectively provide prosthetics to both children and adults in remote regions.
Implants like OPM’s cranial implant, low cost prosthetics likes the Robohand, and high fidelity 3D models of bones, organs and repair sites that enable customized surgical planning illustrate the here-and-now of the technology. Close behind are developments in bioprinting, including scaffolds seeded with stem cells and other tissue-creating elements. Academic and industry leaders contemplate “printing” organs, pharmaceuticals, and more. Just as 3D imaging revolutionized medicine decades ago, 3DP/AM is poised to create innumerable opportunities for personalized solutions and improved health outcomes in the medical arena.
Legal Questions
The legal consequences resonate most distinctly at present in intellectual property and products liability. Protecting your intellectual property (IP) just got a lot harder. How do you protect your patents and brands when someone else – a consumer, prosumer, or distributor does the manufacturing at a local 3D printer? Resist the rising urge to declare the 3D printer the world’s greatest piracy machine. While some aspects of the traditional approach to IP protection may be outdated, the basic tenets will endure. A combination of hard and soft IP skills and experience will still protect the portfolio.
Manufacturers should want to embrace the technology while also protecting their IP. Those serious about gauging the application and ramifications of 3DP/AM will want to consider the short- and long-term options. Based on the scope of the product line and the complexity of the brand needs, their business and legal team should conduct patentability analyses, preliminary clearance reports, trademark analyses, and copyright analysis before engaging the opportunities of 3DP/AM. This groundwork will identify the products that translate best to 3DP/AM and examine anything in the market currently that jeopardizes the brand.
This disruption in manufacturing generates a concomitant disruption in the product liability risks our industry faces and raises many questions: Who or what is a manufacturer? How does the manufacturer control risk? How will new technologies be regulated? Are there new participants that can share the risks? Some of those questions may be answered by looking at how the FDA has suggested it may approach smartphone medical devices applications.
In considering the medical-app device world, the FDA has targeted the entities that create and control the software as the manufacturers of the app. Traditionally, manufacturers bear the primary and exclusive liability for defects and compliance for regulations. However, the question, “Who is a manufacturer?” is now much more complex. Besides software designers and programmers, manufacturers include the companies that develop the specifications for the apps and contract with others to perform the programming. In fact, the providers who link to a website may also fall into the definition now as well.
However, the FDA does not consider hardware manufacturers the same way. The FDA considers hardware makers as component manufacturers, which do not fall under the same strict regulations.
If this analysis is extended to 3D printing, we can expect to see that the entire chain may be proposed as manufacturers: that is, the design owner, the CAD software company, the 3D printer company, and possibly even the filament source manufacturer, as well as the actual original maker may be identified as contributing to manufacturing and associated product risk.
To address some of these problems, the industry needs new analysis aimed at tightening risk management, the virtual distribution chain, and quality control. As 3DP/AM technology spreads and is applied, the distribution channel from manufacturer to end-user will become populated with entities the commerce chain has never seen before. The distribution chain will be upended, and costs will shrink for the right products. The product channel has already started to shrink from manufacturer to authorized 3D printer to consumer, and eventually from manufacturer direct to consumer or prosumer. This will completely alter shipping, warehousing, and obsolescence, but more importantly, it will also forever change the approach to quality control, risk management, and consumer warnings – and manufacturing defects will be a concern as more control passes from manufacturer to end-user. Ultimately, the integrity of the manufacturing distribution chain will need to be airtight, which includes the software down to the clickwrap [See Hotmail Corp. v. Van Money Pie Inc., et al., C98-20064 (N.D. Ca., April 20, 1998), http://bit.ly/18Cn4LM]. Most significantly, the number of entities in the chain of liability will increase, which raises the exposure risks.
Like any opportunity, 3DP/AM comes with risks. However, these risk should not deter companies from pursuing these technologies, and delaying or ignoring this revolutionary shift in the industry could be an even bigger risk. The risk and consequences are simply issues to be analyzed and problems to be solved before joining the revolution. Companies adopting these tools will want to be aware, craft a reasonable plan for protection, and execute it. Analyzing the market, the product lines, and the protections, as well as the transformative application potential of your products is the first step as you bring your business and products into this brave new world.
3D printing will not only affect product and service offerings, it will also impact both intellectual property and product liability law. Innovators can learn from past technology upheavals, but should recognize that in many ways, the advent of direct digital manufacturing by 3DP/AM is unlike anything the business or legal world has seen before. Now is the time to craft your strategy and execute.
McCarter & English
Boston, Mass.
www.mccarter.com
Exponent Inc.
Bowie, Md.
www.exponent.com
About the authors: Patrick J. Comerford is special counsel in the Products Liability Group resident in the Boston office of McCarter & English. Maureen T.F. Reitman, Sc.D., is a principal and practice director for Polymer Science & Materials Chemistry at Exponent Inc., in Bowie, Md. They can be contacted at pcomerford@mccarter.com and mreitman@exponent.com.
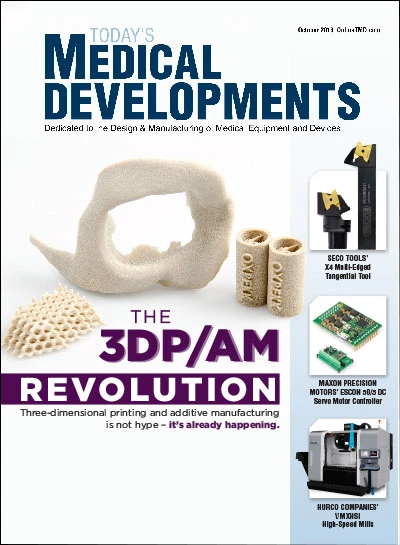
Explore the October 2013 Issue
Check out more from this issue and find your next story to read.
Latest from Today's Medical Developments
- The toolbelt generation
- Covestro's role in transforming cardiac care
- Practical and Affordable Factory Digital Twins for SMEs
- UCIMU: fourth quarter 2024 machine tool orders on the rise
- Thomson Industries’ enhanced configuration capabilities
- Frequently Asked Questions about AM Post Processing
- How new executive orders may affect US FDA medical device operations
- Midwest DISCOVER MORE WITH MAZAK