![]() |
Since the dawn of recorded history, there have been references to amputation and prosthetic limbs. The earliest evidence can be tracked back to cave paintings in France and Spain approximately 36,000 years ago. Thirty-two thousand years later, between 3000 and 1800 B.C., Sanskrit writings of the Rigveda recount the story of a queen warrior Vishpala who, when she loses her leg in a battle, is soon returned to the fight with the help of a fitted iron prosthesis.
Since those early times and heavy, clumsy iron limbs, the medical device industry has made enormous strides. Breakthroughs from the aerospace, transportation, and military industries have advanced the use of lightweight metallic and composite materials such as titanium and carbon fiber. Surgical techniques have also been refined to allow residual limbs that are more functional and thus adaptable to advanced prosthetic designs. It is a result of those improved designs that amputees today are better able not only to do everyday tasks with ease, but even excel so far as to become professional athletes.
One company at the forefront of prosthetic design is Warren, Mich.-based College Park Industries. Products and innovations from the company have changed how the industry officials thought a prosthetic foot could function, resulting in a wide range of prosthetic feet suited for very diverse activities.
Initial Design
After becoming an amputee in 2001 due to a hang gliding accident, Scott Sulprizio, a designer and business owner, began tinkering with his own prosthetic foot. His interest in obtaining the best function from the feet available to him turned into a passion to design and build his own. After much iteration, Sulprizio successfully designed and patented a novel foot concept in 2005 that contained a new, dynamic propulsion ability. Months later, College Park purchased the technology from Sulprizio and began the intense design work to take it from a prototype to a production-ready product for sale.
The main design challenge was making the original concept durable enough for everyday use. The initial design had superior performance, but was not optimized for long-term durability. College Park spent two years further developing the design to maintain the superior functional characteristics of the original design, while incorporating the durability necessary to achieve the 2 million cycle testing required to pass ISO requirements. The end result was the Soleus foot, named after the Soleus muscle in the lower calf, and introduced to the market in 2009.
![]() |
Since then, College Park has continued to innovate. The company’s iPecs (Intelligent Prosthetic Endo-Skeletal Component System) is the world’s first wireless six-degree-of-freedom transducer specifically designed for measuring amputee gait. This unique device measures forces, moments, and acceleration when mounted within the prosthesis, allowing researchers to collect wireless telemetry from their test subjects while performing everyday activities. For the first time, gait labs are able to evaluate what the prosthesis user feels when wearing a prosthetic device, and to do so objectively.
Concept to Market
One way that College Park fosters such design breakthroughs is its use of a nontraditional approach to concept design. Anyone, not just the engineering department, can propose ideas. The company uses CAD design software from PTC to help enable easy, innovative design. Specifically, PTC Creo enables College Park to take any new concept to the market quickly. The company can take ideas or sketches, create 3D models within days, review the industrial design aspects, tweak them, and then prototype it all within PTC Creo. The team can even share its digital 3D models or physical prototypes with customers to gather initial feedback to the different concepts, sometimes looking at 10 or more varying concepts in a prosthetic foot design. They then refine and optimize the 3D models, making sure they meet the design requirements. Then, the engineering team presents the concepts to the management team, which decides whether to pursue the product design or not.
Importantly, College Park never forgets for whom it is designing its products. The level of the patient’s amputation needs to be accommodated, but there are many other factors built into a life-changing prosthetic. The company considers the person’s age, foot size, side, level of activity, and impact level, leading to hundreds of thousands of product combinations. In fact, one product line alone has more than 400,000 viable combinations that allow the foot to be custom-built for each person. That’s part of the reason College Park uses PTC Creo to design and model its products. With the parametric design approach provided by PTC Creo, the team can scale the design for sizes, stiffness, and other variables. As the flexing force changes with each combination, the team can account for all of that in its designs, tooling, and assembly processes. Using PTC Creo Simulate, College Park can simulate and predict stresses and strains within the 3D models it has designed, finding failure modes without building physical prototypes. That cuts many months off the typical design timeline.
Beyond parametric design and simulation, the College Park team uses PTC Creo across its entire product development process: testing, tooling and molding design, and manufacturing. PTC Creo is used to design and manufacture the jigs, fixtures, tools, and mold assemblies needed to manufacture all the components.
![]() |
PTC Creo also provides tailored apps for all the key team members and roles across the product development process, in the same software family. There’s no downtime and no data translation. It’s a seamless transition through every stage, from first concept to full production, ultimately making College Park more competitive. In a recent redesign of the company’s Soleus line, College Park developed and introduced a new product in record time. With PTC Creo, the company optimized the design to reduce weight by 10% and increased strength by 40%. The result is the Soleus Tactical, specifically engineered for extra agility and durability. And while that’s important, it’s not the result that matters most in the end. Each person wearing College Park foot is unique.
Real Life Success
Take Reggie Showers. Showers has been a bilateral amputee since the age of 14 when he was electrocuted in a freak train yard accident. He suffered extensive burns on both of his arms and legs, which ultimately rendered his feet beyond repair. After his double amputation and several months of healing, he was fitted with the standard foot used at the time, called a SACH foot or “Single Axis Cushion Heel Foot.” Although these were state of the art in the 1970s, Showers remembers these SACH as being very heavy and lacking in terrain compliance and energy return.
However, he was determined to live life to the fullest, and over the years, Showers has become an extreme athlete, with two IDBA Motorcyle Drag Racing World Championship victories. He is also an avid rock climber and adaptive snowboard instructor. And he has tackled those challenges with the help of the College Park Trustep feet. Showers found the Trustep provides him the right amount of energy return or propulsion for toe off. Because this foot is very modular in design and has the ability to be adjusted by trained prosthetists, Showers took a training course in 2001 to make adjustments to his new Trustep feet on his own. He can now service his own feet and has several modified specifically for his passion – racing motorcycles. In his case, Reggie is definitely using grit and technology to the fullest, as he likely has the fastest prosthetic feet in the world. In fact, recently racing with his Trustep feet, Showers reached 195mph in a quarter-mile heat. That’s a long, long way from an iron prosthetic.
PTC Inc.
Needham, Mass.
www.ptc.com/product/creo
College Park Industries
Warren, Mich.
www.college-park.com
About the author: Brian Thompson is the vice president, Creo Product Management at PTC. He can be reached at brthompson@ptc.com.
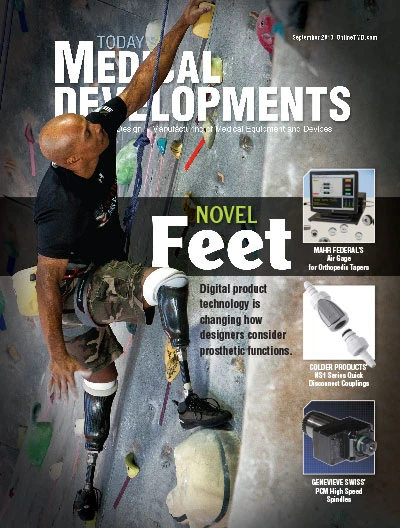
Explore the September 2013 Issue
Check out more from this issue and find your next story to read.
Latest from Today's Medical Developments
- UCIMU: fourth quarter 2024 machine tool orders on the rise
- Thomson Industries’ enhanced configuration capabilities
- Frequently Asked Questions about AM Post Processing
- How new executive orders may affect US FDA medical device operations
- Midwest DISCOVER MORE WITH MAZAK
- Reshoring survey to provide insight for US industrial policy
- NB Corporation of America's ball splines
- AdvaMed seeks medical technology exemption from all tariffs