Newly Formed Company Addresses Five Critical Components
5ME, a newly developed business comprised of the non-machinery units of the former MAG IAS, aims to help manufacturers harvest hidden profits from production operations.
“While manufacturers are under increasing pressure from agile competitors, capacity constraints, material cost increases, and skilled labor shortages, there are still significant opportunities to improve existing operations and return lost profit to the bottom line,” says Pete Tecos, 5ME’s executive vice president for marketing and product strategy. Cost reductions of any magnitude from direct labor, material, or inefficient processes, can yield a substantial boost to the bottom line.”
Led by President Bill Horwarth, and other top managers, engineers, and employees from MAG IAS’ tooling, services, and software businesses, 5ME offers a suite of capabilities – hardware, software, and services applied as an all-inclusive solution.
5ME addresses five critical components – the five “M’s” of man, material, machines, methods, and metrics – to improve a manufacturing enterprise’s efficiency (the “E”). The company focuses on increasing customers’ manufacturing efficiency as a means of building profitable, competitive, and sustainable businesses.
Management operations are in Cincinnati, Ohio, and Detroit, Mich. Detroit is also the home of 5ME’s new technology center, which houses its capabilities in cryogenic machining, tooling/fixturing, process development, asset monitoring, and enterprise software, as well as embedded assistance.
“This is a comprehensive, analytical approach to manufacturing that results in higher productivity, improved quality, and lower working capital. We are brand and process agnostic, and therefore able to work with all types of machinery and manufacturing systems. This gives us the independence to render our best solution and work freely with different system suppliers upstream, as well as end users downstream,” Tecos concludes. https://freedomiot.ai/platform/module/freedom-elog/
Recognizing Outstanding Parts
Metal Powder Industries Federation officials have recognized a range of outstanding parts production in the medical device field that use powdered metal. Highlighted is just one of the winning products produced via metal injection molding (MIM).
FloMet LLC/A QMT Co., Deland, Fla., was awarded the grand prize in the medical/dental category for a 17-4 PH stainless steel jaw made for U.S. Endoscopy and used in a Raptor grasping device. The jaws merge into one design – the features of both a “rat tooth” jaw and an “alligator” jaw – combining the functions of a grasper and a retrieval forceps. The component design is enormously complex due to its small size, thin-wall requirements, and features required for full functionality with the sharp talons and teeth at net shape. The jaw required only minimal secondary processing – coining to help maintain the alignment – and achieved other geometries and tight tolerances in the as-molded condition. MIM is estimated to have saved more than 60% over die casting or machining the parts. www.mpif.org
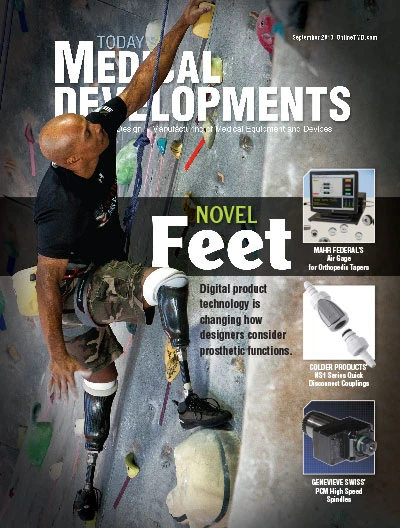
Explore the September 2013 Issue
Check out more from this issue and find your next story to read.
Latest from Today's Medical Developments
- UCIMU: fourth quarter 2024 machine tool orders on the rise
- Thomson Industries’ enhanced configuration capabilities
- Frequently Asked Questions about AM Post Processing
- How new executive orders may affect US FDA medical device operations
- Midwest DISCOVER MORE WITH MAZAK
- Reshoring survey to provide insight for US industrial policy
- NB Corporation of America's ball splines
- AdvaMed seeks medical technology exemption from all tariffs