Over the past 15 years, CNC machining has undergone technological advancements that allow for faster cuts, reduction in machining errors, better finishes, and even leaner operations. Technology for prostheses and implants has also made dramatic advances. For example, today, surgeons and radiologists are able to get a better idea of what size part they’ll need to order for knee-replacement surgery.
Fitting the Patient to the Part
However, even when implementing the latest in technology, things don’t always work perfectly. What happens when the surgeon has read all of the data correctly, but once he opens up the patient during surgery he finds an unexpected surprise and now has an incorrectly sized part? Typically, there are a few steps the surgeon can take to make the part fit within the patient, but they are not always ideal. When fitting the patient to the part, patients are more likely to experience negative side effects such as a longer recovery time, an increased chance of infection, and decreased range of motion. How can the latest CNC technology help?
Control Technology Customizes the Fit
By cultivating a relationship between medical technology such as MRI, CT scans, X-rays, and ultrasounds with machining technology like the Okuma THINC-OSP control, data can be transferred and interpreted with more precision. By capturing information from the data cloud, translating it via application software, and inputting that information into the CNC control, the machine can make the customized cuts that fit the patient, resulting in outcomes that are more successful. After the CNC control has been told the exact dimensions to cut, the machine’s high accuracy comes into play. In-process and post-process machining metrology equipment is used to ensure absolute precision and accuracy. The patient and medical staff cannot afford any fit or finish mistakes here, as a mistake could result in a need for additional surgery.
The CNC control and metrology equipment are not the only machining technologies that can help create customized prosthetics and implants. Technology such as Okuma’s exclusive Thermo-Friendly Concept minimizes the amount of heat generated during processing so cuts are accurate and stable during long, continuous runs. From the startup of the machine in the morning to the end of a manufacturing day, the machine understands where potential part deformities may occur and automatically compensates for them. Rather than fight the laws of physics, the machine control and the material from which the machine is cast are in harmony so the patient will have a precision-machined implant every time.
While making the most out of the research and advancements in CNC machining technology, opportunities are ever expanding. The trauma caused by invasive surgical procedures to repair what has become diseased or worn out can be stressful to the patient. It behooves the supplier of medical replacement skeletal components to use the highest order blend of machining technologies available. With today’s control technology, patients can enjoy the benefits of customized implants or prosthetics that enhance their way of life, and that fits everyone.
Okuma America Corp.
Charlotte, N.C.
www.okuma.com
About the author: Ted Driggs’ is an applications engineering project manager at Okuma America Corp. and can be reached at tdriggs@okuma.com.
Help rename TMD’s FYI department! What do you think it should be called? Send your suggestion to contest@gie.net by 9/27/13 for a chance to win a new iPad.
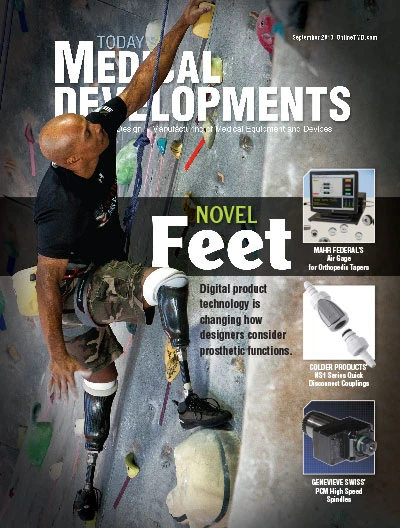
Explore the September 2013 Issue
Check out more from this issue and find your next story to read.
Latest from Today's Medical Developments
- UCIMU: fourth quarter 2024 machine tool orders on the rise
- Thomson Industries’ enhanced configuration capabilities
- Frequently Asked Questions about AM Post Processing
- How new executive orders may affect US FDA medical device operations
- Midwest DISCOVER MORE WITH MAZAK
- Reshoring survey to provide insight for US industrial policy
- NB Corporation of America's ball splines
- AdvaMed seeks medical technology exemption from all tariffs