In today’s competitive manufacturing environment, pressure is increasing to get high-quality products to customers in ever-shorter timeframes, through cost-effective manufacturing processes. Product design and development has changed to emphasize design-for-manufacturability and design-for-cost, where the entire cost of a product during its lifecycle is taken into account. In many cases, the design improvements are related to materials, material properties, and manufacturing techniques.
The need for an advanced approach to manufacturing has been recognized and launched by no less than the Executive Office of the President, National Science and Technology Council in February 2012, with the publication of “A National Strategic Plan for Advanced Manufacturing.” According to the plan, “Challenges to the competitiveness of U.S. advanced manufacturing have the potential to undermine the nation’s ability to create jobs, invent new industries, and protect itself from security threats in the 21st century.” The nation is required, according to the plan, to respond with an “innovative policy for advanced manufacturing.”
The concept of advanced assembly, as implemented by Fabrico, takes a similar approach. It embraces the entire assembly process from design through manufacturing, kitting, packaging, and shipping, looking for ways to enhance materials usage. It’s goal is strengthening the relationship between design-for-manufacturing, design-for-cost, and concurrent engineering principles toward the consistent production of quality, profitable products in a timely manner.
dvanced assembly begins in the design concept stage, where an experienced converter like Fabrico can begin playing a critical role in product development by:
- Enhancing the design;
- Matching the right materials to the product/application;
- Selecting the appropriate adhesives;
- Procuring any additional process materials;
- Rapid prototyping;
- Testing materials for compatibility;
- Fabricating the components; and
- Assembling, kitting, printing, packaging, and shipping finished components.
Enhancing the Design
By taking an integrated team approach and applying advanced, proven methodologies, such as design-for-manufacturing, design-for-cost, and concurrent engineering, an advanced assembly approach can help discover design solutions that will better meet requirements throughout the product lifecycle.
Design-for-Manufacturing
Design-for-manufacturing (DFM) is a process that proactively designs products to optimize every stage in the design process, including procurement, test, assembly, kitting, shipping, service, and repair, to ensure the optimum quality, reliability, regulatory compliance, safety, and customer satisfaction, in the shortest time-to-market, and at the best cost. Following DFM guidelines from the initial design stage has been proven to deliver substantial benefits in reduced costs and shorter time-to-market, plus significant improvements in quality and customer acceptance.
The most innovative design in the world is basically useless if it cannot be cost-effectively manufactured. With Fabrico’s advanced assembly team approach, manufacturing expertise is available to ensure that whether a design uses new materials, adhesives, and processes, or existing ones, all factors are taken into consideration before the design is finalized. Critical considerations include:
- Ensuring the design allows for streamlined fabrication and assembly;
- In-depth understanding of manufacturing processes, including past problems or issues from similar projects;
- Building quality into the process from start to finish;
- Investing up-front labor in a thorough investigation of design and manufacturing alternatives; and
- Testing everything for compatibil- ity and manufacturability.
![]() |
Following DFM principles in an advanced assembly approach includes everything from designing parts/components with symmetry to specifying parts from trusted suppliers.
Design-for-Cost
Why is it important to apply an advanced assembly approach from the start of the design project? According to Dr. David Anderson in the book “Design for Manufacturability and Concurrent Engineering,” 8% of a total project budget has been spent by the time product design is complete, but the design has already determined 80% of the lifecycle cost of the product. Improving manufacturing and product development becomes less tenable once the design is set.
Frequently, a “we designed it, now you build it” mentality often exists between design and manufacturing groups. Now, it is increasingly important that interdisciplinary teams use an integrated approach from the concept stage to ensure that all aspects of product development are understood in the design phase before costs are set in stone.
Design-for-cost (DFC) is one tool in the advanced assembly arsenal that looks at the entire product lifecycle and includes costs from each stage to paint an overall picture of total product cost. DFC can include exploring alternative materials and adhesives to ensure that the desire to exceed specifications and reduce cost is equally balanced in the design stage for successful fabrication and assembly.
Concurrent Engineering
Concurrent engineering replaces a serial approach to design by ensuring that the design of the product and the design of the processes to manufacture that product occur simultaneously and are integrated seamlessly. In some cases, a component might be laser cut, rotary die-cut, or waterjet cut. Which process will suit the application best depends on the material, its thickness, and the tolerances that need to be held. Design and manufacturing engineers can determine in advance the complete process that will work best for an application.
![]() |
For one manufacturer of high-performance engines for electric and hybrid vehicles, a simple change in the design of straps that allow access to the power electronics unit resulted in increased productivity, improved product consistency, and increased process efficiency. The straps were originally designed from tape and intended to be made by production workers during the assembly process. By testing several plastic materials and die-cut patterns, a solution was implemented using 0.014" Mylar that increased productivity, improved product consistency, and delivered better process efficiency. In this case, by working early in the design phase, the design could be enhanced by using a different material and being better aligned with an automated manufacturing process. The parts were designed with fixturing in mind to match the process, saving 5 minutes on each strap assembly.
Choosing the Right Material
In some cases, a manufacturer may have a material already specified into the design. In other cases, a design may meet application specifications using several different materials. Fabrico explores material alternatives before the design is finalized, and suggests the best possible solution to meet all client requirements. Specifying quality materials from reliable sources is key to discovering the right material for each application.
With Fabrico’s extensive supplier network, several electrical insulation materials can be tested from different manufacturers, early in the design stage. In an electric vehicle (EV) application where electrical insulation was required for the traction motor, Fabrico tested several different materials and laminations using an in-house lab.
Typical insulating materials for a conventional gas engine might require lamination that combined an aramid paper, adhesive, and a polymer material such as polyethylene napthalate (PEN) or polyethylene terephthalate (PET). This laminate will withstand motor temperatures up to 155°C. In the case of an EV, the operating temperatures can reach 180°C, requiring an H-class material. Typically, the adhesive and PEN/PET material will fail at this temperature. Fabrico suggested an adhesive-free lamination that used the same aramid paper and layers of a polyphenylene sulfide (PPS) plastic. Like the aramid paper, PPS has excellent thermal performance, inherent flame retardance, good chemical resistance, and high dielectric strength. The laminate is very light and thin, has enhanced heat dissipation, and high slot fill to meet the application requirements.
![]() |
In a second example, Fabrico tested several different electrical insulation materials for an LED lighting system enclosure. The customer specified an insulated box that would totally enclose its lighting circuit boards, yet still provide easy access to the wire terminals and a 120V/277V dipswitch setting. In addition, the box needed an interlocking mechanism that would make installation easy, and allow for operation and warning information to be printed on it. By die-cutting the insulation into a distinct box shape, printing appropriate information on the boxes, and scoring and folding the boxes for flat shipment, the insulation box was designed and fabricated for immediate inclusion in the customer’s assembly line. Having the insulation box designed with the right material for the application as well as the assembly process provided the company with a competitive advantage for this product line.
Choosing the Right Adhesive
Choosing an adhesive that works with the material and application specifications is essential to the success of any assembly project. Is liquid, tape, or film adhesive the right selection? Will the adhesive need to bond with a low surface energy (LSE) plastic? Will it be used in a harsh environment, or need to adhere to a large surface area? Using an advanced assembly approach allows for testing and exploring different alternatives based on cost, ease of integration into the final assembly process, long life, and other critical characteristics. Adhesive alternatives are thus tested, used in prototypes, and implemented or rejected before a design is finalized.
For one electric servo motor manufacturer, a two-part liquid acrylic was originally selected to fix motor magnets to a steel housing. The manufacturer was looking to improve the efficiency of its servo motors by positioning the magnets as close as possible to the rotor.
As the design was being finalized, testing showed that the adhesive would vary in consistency and thickness. This caused problems with motor efficiency, quiet operation, and durability. Too much adhesive between the magnet and the armature impaired electrical performance; too little and the magnet flew off, ruining the motor.
![]() |
A pressure-sensitive tape solution appeared to solve the consistency problems, yet no PSA provided the necessary strong bond to metal. Through investigation into different tapes from different manufacturers, a thermosetting, modified epoxy structural adhesive in film form was eventually procured. The tape was originally used in avionics but proved perfectly suited for this motor application. It had durability, resistance to heat, a short cure time, and, best of all, it increased motor efficiency from 40% (typical of servo motors) to 97%.
Rapid Prototyping
Rapid prototyping (RP) is an important offering in advanced assembly technology. It encompasses a group of techniques that are used to quickly and efficiently fabricate a sample three-dimensional part to exact specifications using a combination of engineering expertise, software, and machining systems.
Rapid prototyping enhances design-for-manufacturability principles by:
- Decreasing development time;
- Reducing costly mistakes;
- Minimizing engineering changes in the final stages of development; and
- Extending product lifetime by adding necessary features and eliminating unnecessary features early in the design phase.
Working with client requirements, an engineering team can use the appropriate software, which can include CAD, CIME, Impact, EngView, Artis-BARCO, Ashlar, and Arden to design a part to specifications. Prototypes are much closer to a finished product, allowing for effective testing and evaluation.
From the software design phase, to prototype production, production systems can include Zund prototyping machines, waterjet cutters, laser cutters, and more.
Testing for Compatibility
Testing is a critical element in advanced assembly technology. This requires an in-house test lab that can provide results on adhesive, material, and electrical tests to characterize an adhesive or material, compare the results with specifications, and explore alternatives.
Testing might include:
- Temperature resistance
- Shear, tensile, and peel strength
- Performance at upper temperature limits
- Outgassing
- Dielectric strength and electrical conductivity
- Thermal conductivity
- Slitting widths and tolerances
Fabricating
Fabrication capabilities should include precision die-cutting using rotary or laser technology, waterjet cutting, and die-less cutting. In addition, precision slitting and rewinding, laminating, and printing are also critical capabilities. Multi-ply laminations of film, paper, and foam, plus customized laminations with in-line die-cutting and narrow/wide web capability are also critical.
Strong fabricating and converting capabilities provide a strong core for advanced assembly focused on materials. In addition, a converter like Fabrico will engage in ongoing materials and adhesives research to discover new solutions that work best for specific customer applications.
Assembly, Kitting, Printing, Packaging
At the end of the process, customer-defined assembly, kitting, and packaging remains. Here, the converter ensures that the finished part, component, or product is handled and shipped exactly as required and delivered in a timely fashion to customers for inclusion in their manufacturing process.
Kitting can be used to reduce materials picking time and improve productivity on the line by consolidating multiple parts into a single, customer specified unit. Kitting can eliminate pre-stage operations and inventory shortages. A converter can accommodate a variety of sizes and materials, as well as virtually any volume.
Printing is often a critical component in the final assembly process, and the ability to offer multi-color printing on different materials, including labels, wrappers, and tape is part of advanced assembly’s core capabilities.
Fabrico worked with a company on a healthcare product from initial design to delivery to the pharmacy shelf. Fabrico suggested the appropriate materials and adhesives, using a cold-seal adhesive that adheres only to itself, used ultrasonic welding to create an anti-microbial pouch for the product, designed, die-cut, and printed each product package, and kitted and assembled 10 individual product packages into a final, consumer box for shelf-display. From soup to nuts, Fabrico worked with the client to streamline the product and process to meet market and industry requirements.
Summary
From start to finish, advanced assembly technology can help ensure that quality is built into a customer project from design through manufacture, enhancing the design, using the best materials and adhesives available, and creating a part that meets specifications and application requirements.
Fabrico
Kennesaw, Ga.
www.fabrico.com
About the author: Rob Fischer is a product development manager at Fabrico and can be reached at rfischer@eis-inc.com.
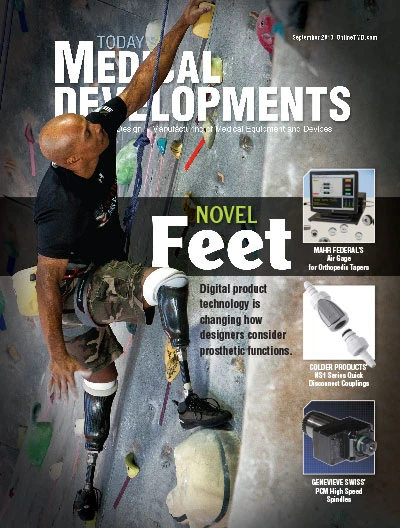
Explore the September 2013 Issue
Check out more from this issue and find your next story to read.
Latest from Today's Medical Developments
- UCIMU: fourth quarter 2024 machine tool orders on the rise
- Thomson Industries’ enhanced configuration capabilities
- Frequently Asked Questions about AM Post Processing
- How new executive orders may affect US FDA medical device operations
- Midwest DISCOVER MORE WITH MAZAK
- Reshoring survey to provide insight for US industrial policy
- NB Corporation of America's ball splines
- AdvaMed seeks medical technology exemption from all tariffs