![]() A formed part for a medical device enclosure shows the possibilities of depth of detail. |
In recent years, there has been a considerable increase in the use of thermoplastics in medical devices. All signs indicate that this growth will continue in lockstep with the global expansion of the medical device market. Advances in custom color matching, new breakthrough materials, forward-thinking technology, improved processes, and increased collaboration allow continuous innovation that brings tremendous opportunity for designers and engineers to advance design aesthetic and performance in medical devices.
This article looks at what’s trending right now, and offers predictions for what will take hold and expand in the next several years.
Human Factors Engineering
To remain viable in the competitive healthcare market, facilities are being designed or redesigned from the ground up to create patient-centered environments. The days of unintentionally building stark, sterile, intimidating, and uninviting healthcare facilities are behind us. As the worlds of people, technology, policy, and work are studied by engineers using human factors engineering, the industry is slowly seeing medical devices more commonly considered an important part of the overall design of an environment in the pursuit of elevated patient care.
Keys to Advancements
Thermoplastics have been a natural choice for medical devices because they are particularly well suited to withstand the rigors of healthcare’s traffic and constant use. Their performance is a given, but certainly not to be taken for granted. They are durable, chemical-resistant, and virtually seamless. Also, because color is integral to the material and there is no paint or laminate to chip away, it stays beautiful longer. A key driver for a fresh paradigm in design using thermoplastics is new raw materials including resins, pigments, and modifiers. For example, now, with the introduction of advanced polymers, many thermoplastics meet the challenges brought by high-heat, autoclave, or gamma ray and e-beam sterilization.
The supply chain is also spurring innovation because specialization and branding are easier to accomplish. Somewhat remarkably, in the past 10 years, minimum required volume for pigments has decreased from a whopping 5,000 lb to 5 lb to 10 lb for premium pigments. Lower cost for custom color and new color engineering processes and techniques allow designers to experiment with hues and saturations that traverse diverse palettes, settings, cultures, and brands worldwide.
Not surprisingly, manufacturing efficiencies are also contributing heavily to innovation. Given the many years, the enormous capital, and human investment to bring a device to market, many designers and engineers are turning to thermoplastics to meet the demand for shorter development cycles, custom solutions, and small runs for piloting product examples to fulfill a speedy device-to-market strategy.
Catalyst for Special Effects and Texture
Manufacturing efficiency exists hand-in-hand with progress in technology. Recently, there has been a lot of traction in pressure-forming technology, and analysts predict significant expansion as designers and engineers realize the reliable results they can achieve, and continue to push the possibilities of this technology.
Pressure forming integrates design with the forming process, which produces low-cost, aesthetically refined parts that compare to those made from injection molding. The combination of air pressure and vacuum – with more sophisticated processing controls for tool and heat temperatures – master traditionally difficult features such as depth, functionality, elegant branding with embedded logos, reverse angles and undercuts, and fewer seams – all without wall thinning and additional processing common in other types of forming.
More rigorous environmental demands (REACH and RoHS, for example) have forced newly sourced materials and coloring systems that meet regulatory requirements while adding dimension to color through effect and texture.
![]() KYDEX XD03 Color Library |
Bigger Role in Design
What goes on inside a medical diagnostic or monitoring device is often breathtaking technology. Shouldn’t the outside reflect that? Color, special effects, and lighting can enhance a device design, reinforcing and mirroring the state-of-the-art technology inside, and conveying confidence in patients that they’re receiving world-class care. More and more often, color is being used to affect how an object’s shape is perceived, using the amount of contrast that is visible across the object’s surface to achieve a perception of smaller size. Clever use of color accentuates features, drawing attention to them, or minimizing others so they aren’t so readily noticed. Transparent thermoplastics can reveal the inner structure of devices to achieve a subtle and beautiful effect or a dramatic wow.
Integral special effects, such as metal-look and pearlescent finishes are also making inroads in thermoplastic sheet. These treatments are popping up in a wide array of applications and industries, including building and aviation interiors, and medical devices. These effects formerly required the application of a special metallic cap, which required additional processing and cost. Now, a monolithic sheet with pearlescent or metal-look finish can be used to achieve the same effect without any additional processing. It is also more durable and will stay like-new longer than a capped sheet – representing a significant potential savings from lower replacement costs.
White, cream, and beige have dominated medical device housings for decades with little-to-no indication of brand other than a logo affixed somewhere on the device, even though two related machines from one brand might look entirely different from each other. Our engineers are seeing a trend in the development and integration of suites of devices featuring embedded logos and branded color details delivering a uniform look among the different machines.
Lighting is also playing a key role in the design and effectiveness of thermoplastics. In this age of thermoplastics, design engineers have the ability to include a variety of effects, that while not being visible to the naked eye, play a significant part once formed into a shape to convey a look and feel, or a mood, when paired with types of lighting. By these means, the enclosure isn’t a solid mass but is imbued with a fluid effect as light flows through it, from it, or changes to convey progress during a procedure.
Color as a Whole Experience
There has always been a trend in using color as code in healthcare, from user interfaces to enabling wayfinding, to alerting staff to emergency. In one outstanding project in Europe, entire rooms were designed in modular thermoplastic components using color to distinguish between hospital staff areas and equipment, and those for patients. Color and effect convey movement, achieving an environment that is gentler and more soothing than flat expanses of color, or lack of any.
Earlier Design Collaboration
The worlds of design and manufacturing are intersecting more powerfully than ever before. Collaboration is happening earlier between designers, technicians, and engineers. That allows manufacturers to innovate with new materials or processes to realize or expand on a design vision.
In the thermoplastics industry, these partnerships enable the achievement of better results, and often in a shorter timeframe. From color and texture to special effects, or the process of forming the part itself, the development of solutions that fully integrate into the design means delivery of a compliant product with refined aesthetic that at once reinforces confidence in state-of-the-art technology, patient experience, and brand. This whole-design approach crosses boundaries of industry and roles and brings about refreshing ideas. Designers take inspiration from consumer goods. Industrial designers are paired with engineers and social scientists to leverage the most from design thinking, human factors engineering, and evidence-based design. Possibilities expand. New roads are taken.
The next few years – and those beyond – promise to be exhilarating in the medical device industry. Advances in materials and manufacturing will influence design innovations, while designers and engineers will continue to inspire manufacturing. As collaboration occurs more closely and more frequently, the industry will witness new special effects, color, and texture playing a larger role in medical devices, more suites of medical devices reflecting their brands or the brands of their customers – all working together to create a better patient experience.
Sound utopian? We’re confident it’ll happen.
Kydex LLC
Bloomsburg, Pa.
www.kydex.com
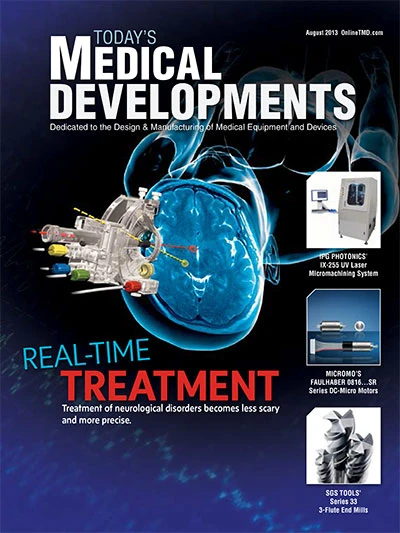
Explore the August 2013 Issue
Check out more from this issue and find your next story to read.
Latest from Today's Medical Developments
- Tariffs threaten small business growth, increase costs across industries
- Feed your brain on your lunch break at our upcoming Lunch + Learn!
- Robotics action plan for Europe
- Maximize your First Article Inspection efficiency and accuracy
- UPM Additive rebrands to UPM Advanced
- Master Bond’s LED415DC90Med dual-curable adhesive
- Minalex celebrates 60 years of excellence in miniature aluminum extrusions
- Tormach’s Chip Conveyor Kit for the 1500MX CNC Mill