More and more motion control systems are dedicated to the precise movement of liquids, particularly for industries such as laboratory automation, healthcare, pharmacology, chemicals, scientific instrumentation, and packaging.
There are two overall motion-control tasks related to liquid handling. First is the actual movement/control of the fluid itself. Second is the movement of the containers that hold these fluids, such as test tubes, microscope slides, and a variety of other carriers. Although we don’t normally think of moving fluid as a motion control problem, as we shall see, it most certainly is. So sit back, relax, and pour yourself a tall glass of fluid as we look at automated liquid handling.
![]() |
I Bet You Say That to All the Liquid-Handling Robots
At the core, all liquid handling automations share some common characteristics. They move to various points on a work surface, draw in (aspirate) fluid from a container, and deliver (dispense) this liquid to some other container.
Figure 1 shows the liquid handling portion of such a system schematically. The major elements are the pump, the connective tubing, the working fluid, and the aspirate/dispense head (often called the tip).
Along the way, we need to control the amount of liquid being drawn in or dispensed accurately, and isolate this liquid sample from previously handled samples to avoid contamination. In addition, many liquid handling systems support multiple tips, so liquid can be drawn in and dispensed to more than one port at a time. Some models provide more than 1,000 such ports.
![]() |
We Want To… Pump You Up
Pumping liquid in accurate measures is at the core of our handling system, so let’s look at a few different pumps that might be used. Figure 2 shows one of the most common types of pumps for high-precision liquid handling, the piston, or syringe pump.
Piston pumps are capable of very high precision. Most use a lead screw driven by a step motor or servo motor. The higher the motor’s positioning resolution, the finer the dispensing resolution. A single-piston pump has a fixed total displacement. While liquid can be ejected or drawn in, the total volume of liquid transfer is limited to the volume of the syringe.
For continuous flow, piston pumps can still be used, but two or more pistons must be arranged so that as some pistons are dispensing, others are drawing in fluid. Devices known as check valves, properly arranged in line with the pistons, limit flow to one direction to provide continuous flow.
![]() Figure 4 |
Can You Draw Me A Diaphragm?
A variation of the syringe pump (perhaps more of distant cousin) is the diaphragm pump, shown in Figure 3. The similarity to the syringe pump is that a seal moves in and out, thereby displacing the liquid. The difference is that the seal is driven in a reciprocating manner, similar to a gasoline engine, alternately drawing fluid in, and dispensing fluid out. Check valves are used to maintain fluid flow in one net direction.
Because a simple spinning motor can generate the reciprocating motion needed for this type of device, diaphragm pumps are very popular. They have even been used in artificial hearts, although in this case external air pressure rather than spinning motors cause the diaphragm to move in and out and thereby pump blood.
Coupled with positioning motion controls, diaphragm pumps can deliver reasonable accuracies of measured liquid. However, for our general-purpose liquid handling system described, a major disadvantage is that liquid flows in only one direction. So for bi-directional pumping, two diagram pumps, one to draw liquid in, and one to dispense liquid, are used.
![]() |
You Had Me at Peristaltic
Figure 4 shows a completely different kind of pump, known as the peristaltic pump. This type of pump uses a roller to squeeze a liquid-containing flexible tube, thereby displacing the liquid in the direction of the roller movement.
The advantage of this type of pump is the separation of the pumping mechanism (the roller) from the medium (the tubing) that holds the liquid. This is ideal for applications where liquid contained in sterile tubing, catheters, or other packaging must be pumped without contacting the contents of the packaging. Dialysis machines, blood transfusion machines, and many similar applications use these pumps for this reason.
The disadvantage of peristaltic pumps is a lack of accuracy. Flexible tubes are elastic, which means their volume may vary. In addition, liquid is delivered in packets consisting of the space between two roller engagement points. So, the fluid flow tends to be pulsed.
![]() |
We’re Operating in a Vacuum
Finally, for precision liquid handling, it is possible to use general purpose air pumps coupled with sensors to deliver surprisingly precise measures of fluid. This type of arrangement is shown in Figure 5.
Here’s how it works: A general-purpose air pump that can create positive or negative pressure is connected to the working fluid tube. Sensors measure the actual air pressure imparted by the pump. To determine the amount of liquid transferred, the air pressure is monitored at regular intervals and a previously created lookup table that converts pressure differential to flow rate is used to sum the total amount of liquid transferred. The advantage of this arrangement is compactness and low cost. Air pumps are inexpensive and come in a wide range of shapes and sizes. At the same time, electronic pressure sensors are continuously becoming smaller and less expensive. So, for many applications, this basic pumping system is perfectly adequate.
![]() |
May I Have 1,000 Samples Please?
Now that we have looked at how we can pump fluids, let’s focus on what we are pumping them into and how we are moving them from point A to point B.
There are two overall strategies here – you can move the robot to the fluid, or you can move the fluid to the robot. Most systems choose the former. The portion of the liquid-handling system that draws in and dispenses fluid dispensing moves, and the containers that store the liquids stay stationary.
Machines that can move slides, test tubes, or special carriers called micro-plates – which can hold as many as 1,536 separate liquid samples each – tend to be mechanically complex and on the large side, in the range of breadboxes to full-sized refrigerators.
The more complex the mechanics and the heavier the load, the greater the importance of minimizing vibration, because vibration is the enemy of reliability and accuracy. Figure 6 shows a stylized mechanism with an actuator, an end effector, and a mechanism base.
As Sir Isaac Newton taught us, every action has an equal and opposite reaction, so if the motor drives the end effector with a given force, an equal and opposite force will be injected into the mechanics that support the end effector.
To get a handle on the overall mechanics, it’s a good idea to perform a resonance scan of the mechanics. Hopefully, your motion control vendor provides software for this, but if not, the basic idea is to operate the motor in a sinusoidal back-and-forth motion, sweeping from a low frequency to a high frequency, and observing the response in the mechanics.
I Think Therefore I S-Curve
Once we are ready to optimize controls, the first step is to select motion profiles that minimally excite resonances in the mechanics. How do we do this?
The answer is that we minimize jerk. Change in the rate of acceleration, or jerk, is a primary source of vibrational energy injected into the mechanics. So less is more.
By adding an S-segment, which is an interval over which the acceleration transitions from one value to another, the total vibrational energy as well as the frequency range of injected vibration is reduced The trick is to add a small amount of “S” so that the total move duration is not unduly lengthened, while still dramatically reducing the mechanical vibration.
It is worth noting that the very same concepts apply both for step motors and servo motors.
![]() |
FeedForward Me!
With our profiles optimized to minimally inject vibration, we are ready to add one more control element that is important for servo-based machines. This control element is feedforward.
For a Cartesian X-, Y-, Z-type motion system, applying feedforward is simple. We want to inject an acceleration-proportional signal directly into the position loop that offsets the inertial (read that Newtonian) forces our load and end effector will experience. The simplest procedure is to use trial and error to determine feedforward values. Start with small acceleration feedforward values and increase until you notice the servo error is minimized. Don’t forget to check out the move forward and backward. Some sample capture traces are shown in Figure 8.
Finally, if you have a Z-axis under servo control, consider using your motion controller’s PID bias setting (sometimes called a motor bias or motor command offset) to feedforward a constant value that counteracts the force of gravity.
Summary
Moving liquid, and moving containers that hold liquid, represent two critically important tasks in the fast-paced field of laboratory automation.
The keys to design success are understanding what type of fluid pump will work best in your application, and selecting motion controls that give you the pumping accuracy you need.
When you are building your robotic mechanism, focus on reliability and performance by optimizing the mechanics using resonance analysis, minimizing injected vibration by tuning the profiles, and selectively useing feedforward to make the job of the PID loop as easy as possible.
Motion Cards Learn New Tricks Prodigy/CME cards utilize PMD’s Magellan motion processors and are available in a number of formats including PCI, PC/104, and stand-alone. They provide Ethernet, CANbus, and serial communications and are programmed in standard C language. The C-Motion Engine code execution unit operates at 96MIPS and allows easy integration of user application code onto the card using PC-based development tools. |
Performance Motion Devices Inc.
Boxborough, Mass.
www.pmdcorp.com
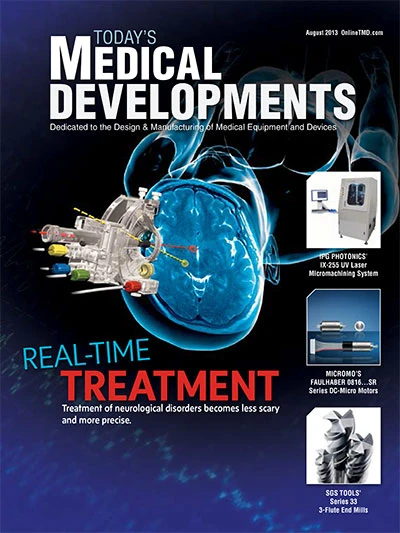
Explore the August 2013 Issue
Check out more from this issue and find your next story to read.
Latest from Today's Medical Developments
- Tariffs threaten small business growth, increase costs across industries
- Feed your brain on your lunch break at our upcoming Lunch + Learn!
- Robotics action plan for Europe
- Maximize your First Article Inspection efficiency and accuracy
- UPM Additive rebrands to UPM Advanced
- Master Bond’s LED415DC90Med dual-curable adhesive
- Minalex celebrates 60 years of excellence in miniature aluminum extrusions
- Tormach’s Chip Conveyor Kit for the 1500MX CNC Mill